The critical role of quarries and mines in advancing economic development cannot be reiterated enough. At the same time, sustainability has become an underlying principle, with environmental, social and governance (ESG) performance considered the new currency in the industry.
In order to help support global sustainability goals, quarries and mines have in recent years accelerated their sustainability efforts. In a one-on-one with Quarrying Africa, Nishen Hariparsad, GM Technology & Marketing at BME, says beyond usual compliance imperatives such as health and safety, pro-sustainability actions have taken root in the industry’s quest to validate its social licence to operate, with blasting service providers being expected to contribute to customers’ efforts to lower their carbon footprint.
Delivering sustainability
As the first unit operation with a significant impact on downstream mining processes, blasting plays a big role in reducing a quarry’s overall carbon footprint. Through a full basket of complementary blasting technologies, coupled with advanced low-carbon emission emulsion explosives, BME continues to pave the way on the industry’s sustainability journey.
BME constantly innovates its explosive solutions and technology to provide customers with more efficient and productive operations – thus helping to reduce their energy consumption as well as the carbon emissions generated.
“As blasting and blasting technologies continue to evolve, we have encapsulated a suite of products, systems and services into a sustainable ecosystem of solutions that meets our customers’ needs,” says Hariparsad.
Building on the flexibility and accuracy of electronic detonation, BME’s digital tools can make quarrying more efficient and less carbon-intensive through controlled blast energy, minimal waste, improved safety, lower energy consumption and optimal fragmentation. For example, with the use of flagship products such as BME’s premium electronic detonation system, AXXIS, together with the company’s BlastMap blast design software, whether independently or as a package, unlocking sustainable benefits for quarries and mines is made easier.
To provide context, while the AXXIS Titanium allows for large blasts of up to 20 000 detonators, the AXXIS Silver is designed for up to 1 600 detonators – 800 per blast box, which is more than enough for the quarrying industry’s blasting requirements. The accuracy of detonation delays has been enhanced, reaching 0,0067% firing accuracy for consistent quality blasting that results in optimal rock fragmentation and consistency. The programmability of 15 seconds with 1-millisecond intervals allows for blast designs to be precision-designed, resulting in better fragmentation.
The benefits of good fragmentation are well documented, says Hariparsad. Firstly, it eliminates the need for costly secondary blasting or mechanical breaking of oversize material. Secondly, there is a positive impact on downstream processes such as load and haul. Crusher throughput also increases due to improved overall particle size distribution. The overarching benefit from all this is reduced energy consumption in the mining value chain, which in itself constitutes a sustainability effort achieved.
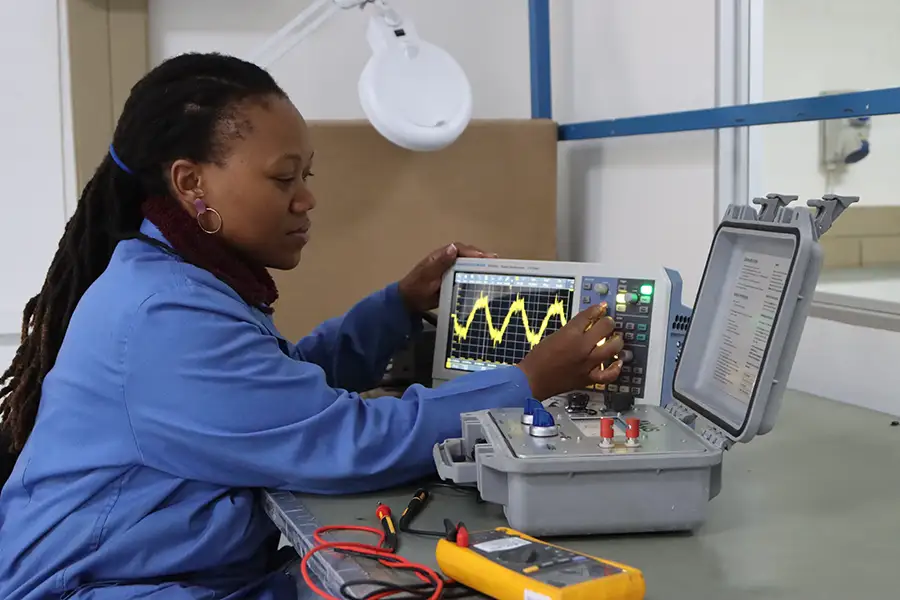
More sustainable initiatives
Over the years, BME has pioneered the inclusion of used oil in its emulsion explosives and is said to be the largest consumer of used oil in the explosives sector. This initiative contributes to a circular economy by safely disposing of used oil in a responsible manner, while preventing any of this oil from contaminating water or land.
It is estimated that it takes only a litre of oil to contaminate a million litres of water, making the safe disposal of oil a strategic global imperative – especially for water-scarce countries. BME’s used oil initiative is aligned with the United Nation’s Sustainable Development Goals (SDGs) – which focus on goals such as access to clean water, food security and eradication of pollution.
In South Africa alone, the company consumes almost 25-million litres of used oil annually and plans to increase its collection and processing capacity steadily over the next few years. The company’s oil collection network has evolved over time – aligning each phase with its ISO 9000 quality certification. It is also registered as an approved collector and processor with the Recycling Oil Saves the Environment (ROSE) Foundation.
In addition, BME is pioneering the use of dual salt emulsions in blasting operations. Dual salt emulsions are less harmful in terms of nitrate contamination and greenhouse gas emissions than single salt emulsions. These emulsions can be transported long distances, pumped multiple times, and still provide improved performance, such as high energy in a blast.
The recent acquisition of a minority stake in Swedish-based Hypex Bio Explosives Technology by BME’s parent company, Omnia Holdings, further positions BME ahead of its competition in terms of sustainable emulsions. Hypex has developed the first nitrate-free explosive emulsions in the market and reduced the carbon content by 90% over traditional sources. This technology has the potential to completely change the explosives supply industry.
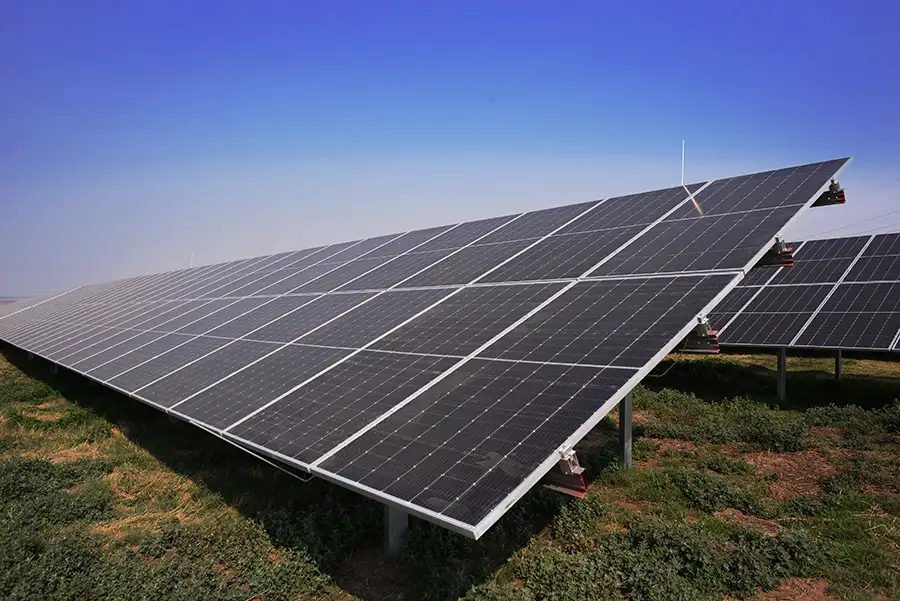
Innovation
The mining industry of today, says Hariparsad, is dependent on technology and innovation to improve efficiency, safety and environmental sustainability. Consequently, BME believes in incessant innovation to continue delivering on the evolving technological needs of the industry.
“As mining companies shift their strategies and operating models to leverage digital transformation and cloud-based technologies, we see blasting technologies playing a critical role in delivering bottom line improvements for the mining value chain, more so for quarries that are cost-sensitive by their very nature,” he says.
For BME, adds Hariparsad, innovation in various technologies across all streams of the company’s product stack is not about feature benefits, but rather a strategic imperative to remain relevant through industry-leading technologies that provide data, analytics, digital connectivity and integrated automation across all functional streams.
One of the key pillars of BME’s innovation roadmap has been digitalisation which, according to Hariparsad, has played a transformative role in improving blast outcomes, enhancing safety and efficiency as well as achieving environmental sustainability. By integrating advanced digital technologies, quarries and mines can optimise blast designs, reduce waste and minimise their environmental impact. BME’s digitalisation seeks to decrease inputs and increase outputs and raise safety levels in mining processes.
One of the design focus areas for BME has always been the integration of its own systems, also incorporating third-party solutions that customers might have at their operations. For example, BlastMap, the company’s blast design software now integrates with Xplolog, a system for capturing and analysing data on blast holes and decks, which further integrates with BME’s mobile manufacturing units (MMUs), allowing the operator to charge and top up holes accurately from the source application. This, says Hariparsad, represents an ecosystem of blasting software and digital technologies providing real-time data at various levels of the blasting value chain.
With digitalisation comes a lot of data which, according to Hariparsad, has become ‘king’. However, he highlights the importance of understanding the data to address customer pain points. “We are therefore building a repository of information that targets key elements of not just the blasting process, but the mining value chain at large, because we acknowledge that these are all interconnected,” he explains.
“Our blast design data can ‘talk to’ drilling data, which in turn ‘talks to’ geological data. Utilising this data across all streams of the mining value chain, including crushing and screening, allows us to better paint a complete picture. Operations can only realise value downstream if they understand what their pain points are. Having access to data and making sense of it makes it possible,” he states.
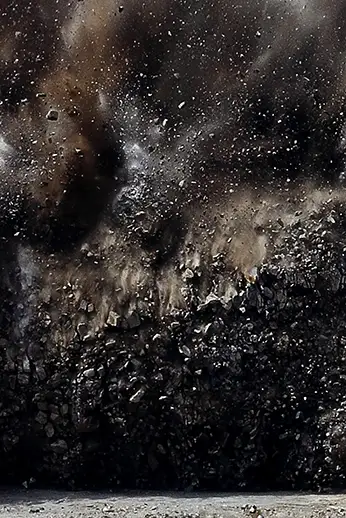
Security of supply
Apart from technological advances, Hariparsad believes that one of the key trends to emerge in the aftermath of the Covid-19 pandemic is a re-focus on the security of supply for key mining inputs such as explosives.
The industry’s supply chains, he says, had been honed for many years to become as cost-efficient as possible, often driven by the ‘just-in-time’ philosophy. The economic lockdowns, closure of borders and logistical disruptions worldwide have led to a re-evaluation of this approach.
Customers now tend to be more concerned about security of supply, and often adopt more of a ‘just-in-case’ attitude. It was interesting to note that, throughout the Covid-19 disruption, BME was able to continue supplying its customers within and across borders without a single stock-out.
“The Omnia Group’s focus over the past two years has been to strategically strengthen security of supply, all the way from sourcing of raw materials to the storage of finished products. We have multiple suppliers of raw materials, various transporters and plants, to ensure that all possible risk is sufficiently mitigated,” says Hariparsad.
Omnia Group is the only producer in South Africa that has a dual supply of ammonia, a key feedstock for all emulsion blasting providers, which ensures security of supply. “We have redundancy of supply, not just at our operations, but also at customer sites to ensure that we keep minimum stock levels all the time.”
In addition, BME’s sustainable manufacturing processes ensure security of supply. Its initiatives in green hydrogen, green ammonia, water recycling, grey harvesting and a 100 MW solar plant all contribute to sustainable sourcing, which in turn delivers security of supply for customers. These projects are particularly significant in South Africa, where the company has to grapple with power shortages, constraints in water infrastructure and challenges in logistics infrastructure.
Leveraging lessons from its home market of South Africa, this approach has been replicated in international markets where BME has a presence as part of its globalisation strategy. Over the years, BME has developed a well-crafted globalisation strategy which has strategically positioned it in growing markets outside of its home base of South Africa and Africa. Its growth strategy in markets such as Australia, Asia and the Americas hinges on the expansion of its manufacturing footprint to ensure security of supply.
In summary, Hariparsad says the company’s growth strategy and its business imperatives are interconnected. “We do this to remain inoculated against the challenges of the system, while promoting the greatness of the values that we offer, namely sustainable solutions, integrated ecosystems of products and services, resource efficiency, contribution to the circular economy, responsible business partnerships, as well as safety and reliability for our people and the communities in which we operate,” concludes Hariparsad.