Sand has traditionally been obtained from natural sources such as rivers and coastlines. However, new regulations have been enacted to protect these sources in many countries across Africa and the world at large. Given these realities, the construction industry has been forced to adopt a suitable and sustainable alternative fine aggregate, better known as manufactured sand.
Considering the depletion of natural sand reserves and the stringent regulations on sand mining, demand for manufactured sand is projected to witness significant growth in the next few years. Factors such as urbanisation and the ultimate growth of construction activities will further drive demand.
Despite the scourge of illegal mining in many parts of the continent, the migration to manufactured sand has taken root in many countries. To provide context, several quarries in South Africa already report that a large share of their sales is attributed to sand. Given this rising demand, it is important that quarries and sand producers deploy the right equipment to produce high-quality manufactured sand.
Wayne Warren, Africa sales manager at Pilot Crushtec International, says manufactured sand has become a hot topic in several African countries with quarries striving to fill the gap created by the loss of natural sand reserves. In many instances, he says, the VSI has become the go-to crusher due to its ability to produce high-quality, cubical and well-graded sand, an application where traditional solutions such as cone crushers have proven uneconomical to use.
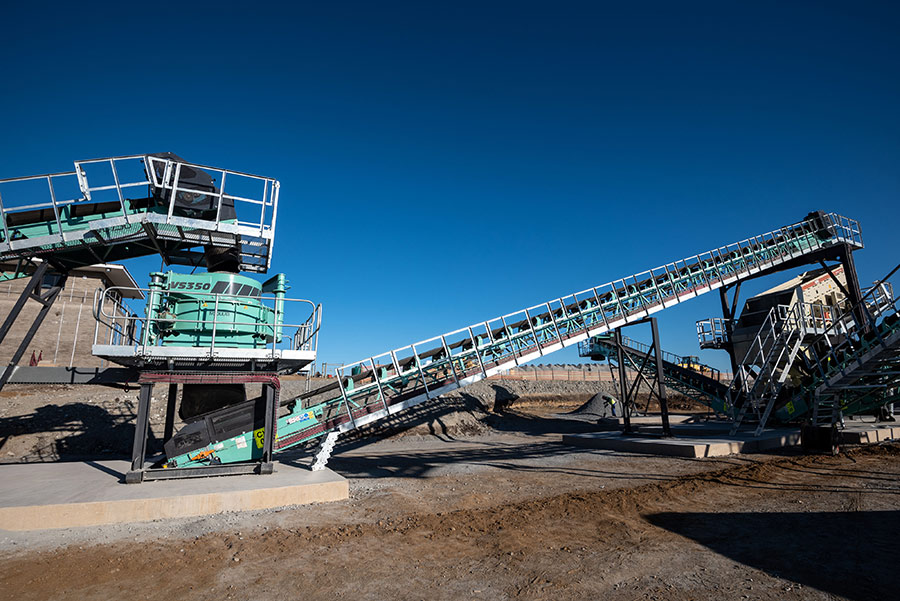
Why VSI?
Before VSIs became as common as they are now, says Warren, cone crushers were preferred, but they are an uneconomical way of producing sand. The downside is that for cone crushers to produce sand, one needs to crush with a very tight closed side setting (CSS), which by its nature is not economical because of the extremely high wear it causes.
“When using a cone crusher to manufacture sand, the crusher needs to be closed down to a very tight CSS, resulting in liner-on-material crushing. This is not ideal because the wear rate increases dramatically, and the shape is generally poor. The crusher works effectively in liner-on-material, on-material, on-liner crushing,” explains Warren.
The VSI’s rock-on-rock crushing principle is more efficient in producing high-quality manufactured sand as it directly crushes the rocks without any intermediate crushing stages.
“The VSI makes use of material-on-material crushing – the stone is accelerated at high speed into a rock box of the same hardness material, resulting in maximum breakage of the feed material,” explains Warren. “Depending on the speed, this can accomplish two things: stone shaping with some sand generation or, on a higher speed, a higher percentage of sand.”
Charl Marais, sales manager at Pilot Crushtec, says another major advantage of using a VSI over a cone crusher is the ability to achieve constant product grading. “If you feed a VSI constantly, it yields a constant grading. On the contrary, with a cone crusher there is inconsistency in quality because of the way the liners wear. As soon as you have an uneven wear pattern on your mantle and bowl liners caused by intermittent feed conditions, your grading fails as well. It is also difficult to rectify intermittent feed conditions and to supply a cone crusher with a constant feed to keep the cavity full; surge bins are installed which drives up capital expenditure,” says Marais.
Warren agrees, saying that with a cone or a horizontal shaft impact (HIS) crusher, there is constant variability, completely the opposite of the VSI, which does not have any variability because of the fact that there is no CSS to wear out and change the grading. Even though a VSI makes use of a rotor, which is a wearing component, the gradation of the sand does not change.
This, adds Marais, makes the VSI the crusher of choice for processing the material used in building bridges and dam walls, where constant grading is a principal parameter.
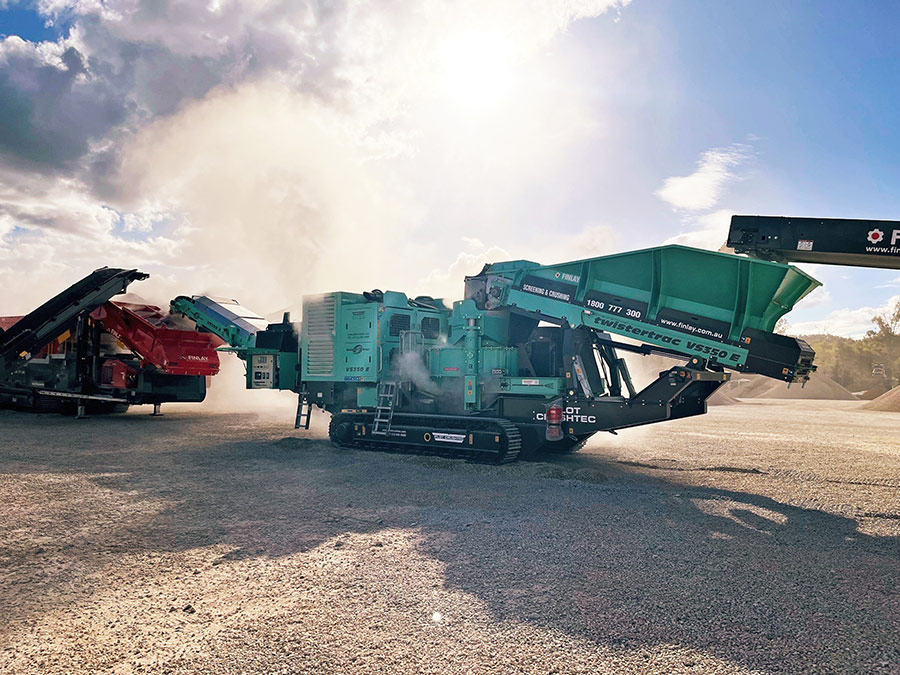
Full range
With a rich heritage in the design and manufacture of VSIs, which dates back to over 30 years ago, Pilot Crushtec has established itself as a major player in the international VSI market, with key successes recorded in markets such as New Zealand, Australia and selected European countries. More recently, the company has also introduced its VSI offering in the United States. “As the success story grows, so does the demand in outlying areas. The majority of our mobile track-mounted VSI crushers are therefore being exported,” says Warren.
Pilot Crushtec’s VSI models cover a broad range of kilowatt (kW) units in three shells, from 45 kW to 315 kW. The three base models comprise the VS100, VS200 and VS350 (up to 350 tph), covering five different rotor diameters and 14 different configurations to suit varying customer needs.
The rotor sizes are 600 mm, 700 mm, 800 mm, 900 mm and 1 000 mm, as well as the open top rotor option. On the small kW units, the 600 mm rotor is ideal, and as the feed size increases, the bigger rotor sizes are the standard. The open top rotor is generally used with anvil rings, where the feed size is slightly larger.
In addition to the three base models, Pilot Crushtec offers the mobile TwisterTrac VS350E, a diesel-electric version of the hydraulic mobile TwisterTrac VS350. Being a bi-powered machine, the VS350E provides increased operational efficiency, while reducing the carbon footprint. With this model, customers can expect to reduce their cost per tonne by up to 50%, while increasing throughput by 15-20% compared to the hydraulic version.
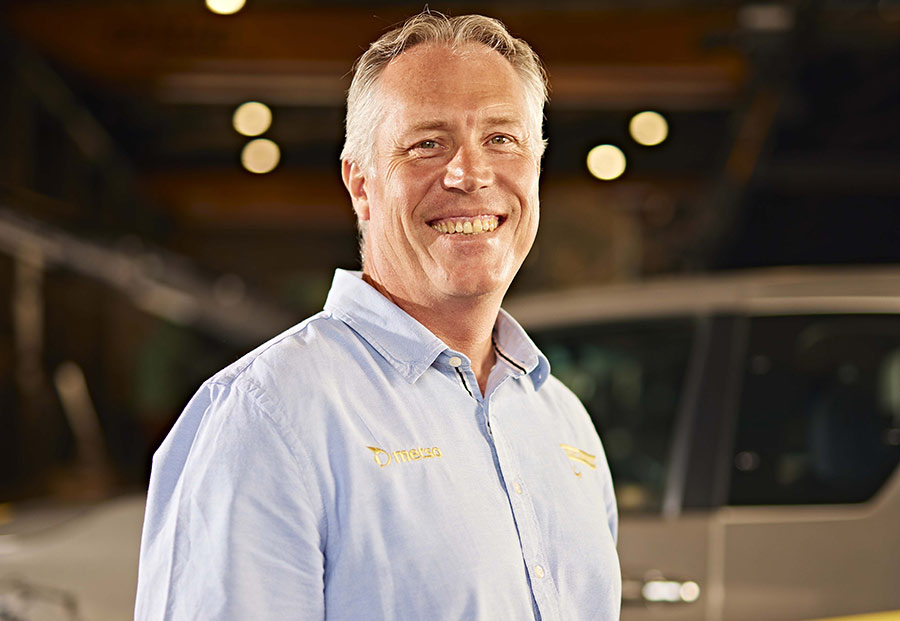
New solution
While the VSI has proved itself as the ultimate sand maker, it is not without its limitations. According to Warren, one of the downsides is that a VSI by its nature is a power-hungry machine. “The VSI gives you high-quality manufactured sand with a consistent shape and gradation, but it uses a fair amount of energy and has high wear, especially when the feed has a high silica content, which is often the preferred material in sand making,” says Warren.
In addition, with the machine highly dependent on constant feed material, there is a high possibility of excess fines. This, says Warren, can be difficult to overcome when generating sand. In a standard crushing plant, fines generation is often higher than recommended, calling for blending of material to meet requirements for concrete production, for example. To mitigate excess fines in sand, washing has become a go-to solution for ultra fines removal. Given the water shortages in southern Africa and several other regions on the continent, washing is often out of the question.
Considering these challenges, Pilot Crushtec believes it has a perfect solution to complement the VSI crusher where fines generation cannot be controlled. In March this year, the company will be introducing the Metso HRC8 high pressure grinding roll (HPGR) for manufactured sand and aggregate production. Metso has traditionally used this technology in mining applications, but has recently adapted it to suit the aggregate market.
“The HPGR’s adjustable pressure allows you to vary the curve grading for finer or more coarse grading. Based on available data from other regions, the machine consumes about 50% less power in sand production compared to other technologies for the same volume of net product. We have been watching the results from many installations across the globe and based on that, we have decided to add this technology to our regional offering,” concludes Warren.