Mining conveyors are typically massive, powerful systems that can move tonnes of material per hour, often configured in complex networks and over long distances, thereby minimising costs while performing work that would otherwise create both labour and logistical nightmares. But their size, speed and power also present the risk of a catastrophic injury that can occur in the blink of an eye.
Even the reaction time of a highly-trained professional athlete is no match for a bulk material conveyor. Conveyors apply large amounts of mechanical energy to what is essentially a giant elastic band, stretched tight and threaded through a maze of components.
This stretched band is often loaded with tonnes of material, sometimes using drive motors as large as 600 hp (450 kW). A typical conveyor belt moves at a relatively constant speed, commonly running between 0,5 to 10 m per second. Given the weight, speed, inertia and kinetic energy, enormous forces are involved. The human body, able to generate less than 1 hp (0,75 kW), simply cannot compete.
Training challenges
One of the challenges facing conveyor operations is the expertise and knowledge leaving many industries through retirements. A deep understanding of how conveyors function may not be handed down through basic on-the-job training passed from worker to worker. Although valuable, this type of training cannot be vetted to be sure that the underlying concerns are understood by a learner, nor does it allow for adjustments that may need to be considered with changes in production or auxiliary equipment.
In addition, information that is transferred to new employees may not reflect industry best practices. When mines take a “here is how we do it” approach, they are vulnerable to past workers’ teaching techniques that may not be the best long-term resolutions. This introduces risks to the mine in terms of safety hazards, inefficiency and premature equipment failure.
In many mines, there is a lack of qualified conveyor trainers. Most conveyor training comes from vendors of systems and components. Suppliers can train very well on how their products should be maintained and installed and what problems they can solve. But much of this type of training is done from the vendor’s or manufacturer’s own point of view. Rarely is training available that addresses the mine personnel’s perspective. This can tarnish training effectiveness, reducing the learner’s interest if it does not speak directly to the worker’s recognised needs.
There are also generalisations that are accepted as truisms and seemingly require no proof due to their long-standing use in conveyor operations. But it is easy to perpetuate bad habits unless operations personnel have solid, real-world knowledge in bulk material handling and can make educated decisions when addressing problems. With the ‘old salts’ who developed and handed down these practices fast retiring, there is a need to provide knowledge to the younger operators and maintenance workers to avoid the trial and error associated with applying many of the handed-down approaches.

Loss of ‘tribal’ knowledge
While the loss of ‘tribal’ knowledge is an issue, it also creates an opportunity to significantly improve operations through third-party expert training. Factory-trained specialists who focus on overall conveyor performance and safety rather than just component function can deliver thorough, objective instruction that is untainted by a “we have always done it this way” approach.
Training based on a combination of deep industry experience and modern engineering will greatly improve operating decisions, resulting in higher productivity, fewer safety incidents and reduced unplanned outages.
Dealing with complex and changing regulations can present additional challenges. Some regulations may not fully protect a worker, depending on an individual mine’s circumstance, so local governments and corporations often add their own requirements in an effort to improve productivity and minimise injuries.
In addition, new conveyor systems are increasing in size, speed, complexity and sophistication, with automation playing an ever-increasing role. The move toward automation was originally targeted at reducing labour costs but is now focused more on productivity improvements. As systems start to “run themselves”, the reasons for unplanned shutdowns can be misunderstood and not addressed, and systems may be bypassed, resulting in going back to the same old procedures. Maintenance is becoming more driven by data knowledge and less by ‘wrench smarts’.
Updated design and control philosophies are becoming more critical for making informed operating and repair decisions, and conveyor operators and maintenance personnel are increasingly in need of a deeper understanding of the entire system. All these factors indicate a need for training that is specifically tailored to individual sites and operations. The one-size-fits-all approach is becoming less attractive – and less effective – with each passing year.
Understanding how and why accidents happen is also critical in preventing them from occurring. Some might argue that workers’ unsafe acts are the primary cause of accidents. Yet many safety professionals have realised for some time that the root causes of accidents are not that straightforward.
Often, the employee’s action is not the only – or even the most significant – root cause. The real underlying causes are usually more involved and require a more complete accident analysis, followed by thoughtful corrective action. Addressing the symptoms with workable long-term root cause solutions will reduce unsafe practices, improving availability and safety, while enhancing profitability.
A 2003 study by a major corporation found a correlation between fatalities and unsafe practices, indicating that for every fatality there are an estimated 300 000 unsafe behaviours.
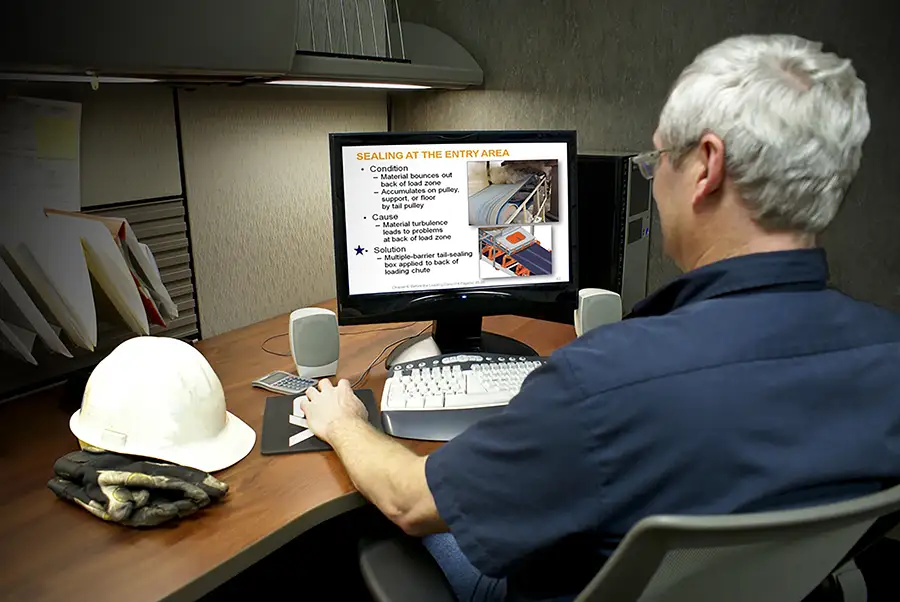
In search of a deeper understanding
Most operations personnel are only expected to know the basics of how conveyors operate, but they may not be fully aware of their limits, safety protocols and best maintenance practices. However, optimising a conveyor system requires an advanced understanding of how fugitive material relates to safety and the newest technologies to control dust and spillage, as well as accommodating changing production demands and how to use existing designs to meet those demands. Some mines lack a deeper understanding of equipment limitations, which encourages workers to treat symptoms such as fugitive material by adjusting skirt seals, for example, when the real culprit may be insufficient belt support or wear liners.
Equipment vendors and third-party trainers can be a highly effective source of training, but there are hundreds of companies providing such services, and expertise and approaches vary widely. Most are not bulk handling specialists, and even among those that focus on conveyors, their offerings are rarely mine-specific. That means the nuances of an individual facility and its equipment are addressed by a generic programme presented to all bulk handlers. Training is often piecemeal, with little follow-up to evaluate progress toward mine-specific goals and spotty access to industry experts.
Some firms take training seriously yet fail to repeat and update training often enough. Any approach that allows maintenance personnel to drift back toward trial-and-error learning is certain to increase costs and reduce effectiveness. The results can include a lack of deep understanding of the mine’s conveying systems and how the various components should work together, as well as increased regulatory oversight, disengaged workers, reduced productivity, poor safety records and increased labour turnover.
In contrast, dedicated educators with a specific focus on (and a reputation for) expert conveyor training will guide personnel along a path of best practices and continuous learning. The most successful trainers develop a site-specific curriculum that pertains directly to the individual facility, delivering information that not only educates, but also motivates learners to change behaviours.
Good teachers should provide a variety of delivery methods, based on different learning styles, that is, good graphics for visual learners, clear documentation for those who learn best by reading, and demonstration models or actual equipment for hands-on learners, all designed to increase the probability that there will be measurable positive results.
Some trainers are even able to integrate their programmes with customer Learning Management Systems, so companies can ensure thorough and convenient training for all employees – at all levels – across multiple sites. Customers can make effective use of their learning management system (LMS) by centralising conveyor training, delivering consistent high-quality content inexpensively that is available 24/7 and by ensuring that all workers have the same level of education on vital bulk handling systems. This also gives trainers an opportunity to review data that helps identify trends or indicates a need for additional content or refresher courses.
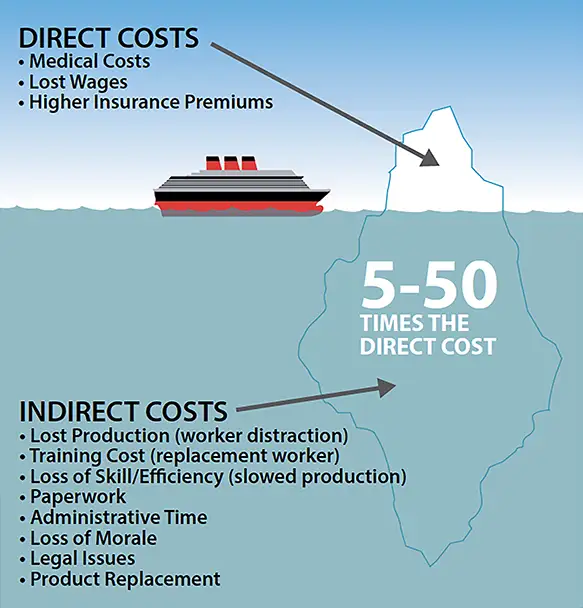
Payback on training
While most maintenance workers are skilled technicians, they are often not expected to understand the conveyor holistically. Conveyors are complex, integrated systems; a change to one component will often have unintended consequences for others, affecting the rest of the system.
Without a complete understanding of how conveyors are designed, and components selected, maintenance becomes an exercise in finding the longest-lasting ‘band aids’ to treat the symptoms rather than solving the root causes. Before long, an accumulation of bad choices in treating symptoms results in a system that cannot operate at maximum efficiency.
Some companies continuously focus on an effective training culture (and thereby improve safety) from the top down. Organisations that embrace this approach show significant performance advantages over the competition. The proof is reflected in safety, productivity and environmental records, along with above industry-average financial returns and share prices.
While the goal of many training efforts is to maximise productivity, a key element in achieving this objective is improving safety, minimising injuries and the associated repercussions. Literature and research offer many pieces of the puzzle on how safety pays, showing a correlation between reduced expenses and a clean, efficient conveyor. Numerous case studies revealing the positive relationships between safety and productivity are backed up by organisations that gather global statistics on accidents and incidents.
Insufficient safety training can be incredibly costly to a mine, with direct and indirect costs of every accident. When mines ensure workers have sufficient training on particular risks, the risks and costs are minimised. Indirect costs are harder to understand, and often the return on investment is unclear to personnel. Expert training helps bridge that gap, and instead of simply teaching workers how to maintain a conveyor system, educators must also help students understand the consequences of not performing adequate maintenance.
Conclusion
The most effective approach to training examines a mine’s specific conveyor challenges and helps companies run cleaner, safer and more productive operations by treating the root causes of its problems.
When workers and management understand why certain actions are important, as well as the cascading effects that result from poorly trained staff, they are more likely to adjust behaviours and ultimately reap the benefits.