Having made its local debut some two years ago, the Liebherr TA 230 has proven itself in some of the toughest operating environments in southern Africa. With several units already operating in the field, clocking about 35 000 – 45 000 market hours in the process, Tendayi Kudumba, GM: Earthmoving, at Liebherr-Africa, expects the sales of the Liebherr TA 230 to pick up steam on the back of increased enquiries in the region.
“The ADT market in southern Africa is very competitive, but we are very happy with the sales performance and enquiries of the TA 230 to date. Several customers have shown immense interest in the machine, and we expect to put more units into the market soon,” says Kudumba.
Biggest customer
With five units in its fleet, Orca Group, a prominent mining contractor operating in Zimbabwe, runs the biggest fleet of Liebherr TA 230 machines in southern Africa to date. In fact, the company was the recipient of the first ever TA 230 in the region, which was handed over during the official launch at the Liebherr-Africa headquarters in Springs, Gauteng, South Africa, in June 2022. The company initially took delivery of three units, before expanding the fleet with two more machines.
The five machines have been deployed in a taxing application at Bindura-based Freda Rebecca Gold Mine, hauling ore from the underground tunnels to the overland crushers. Lavell Ruthman, Head of Sales, Earthmoving Technology at Liebherr-Africa, tells Quarrying Africa that the machines have already clocked between 6 000 and 7 000 hours in this challenging application, travelling 15 km out of the pit fully loaded in extremely hot conditions.
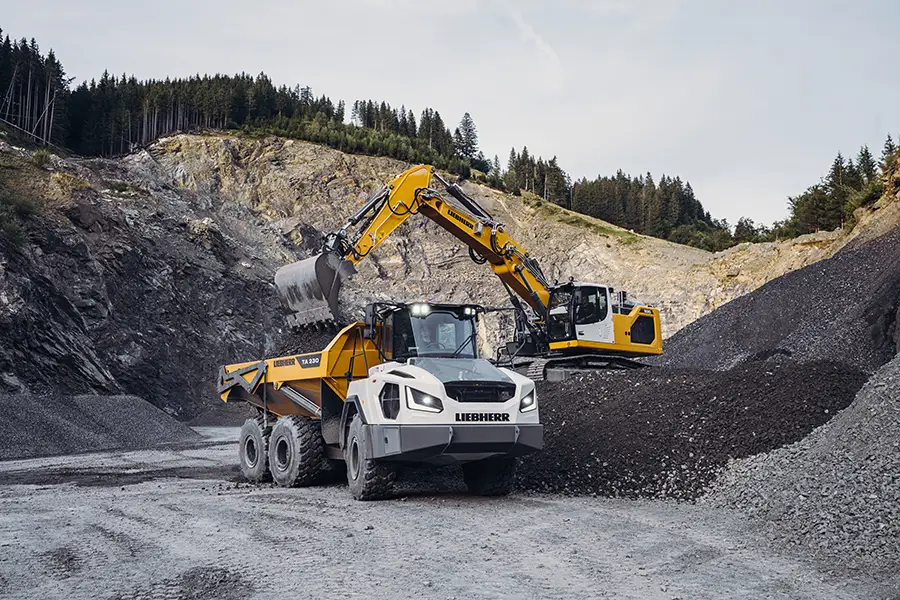
More units
Two of the first batch of five units to be delivered in southern Africa are hard at work in the Palaborwa area in South Africa. Running at this particular site for over a year now, the two Liebherr TA 230 units have already passed the 6 000-hour mark.
“Despite the heavy and abrasive nature of magnetite, the two machines have proven their mettle in this tough application, meeting the requirements of the customer in terms of uptime, efficiency and productivity,” says Ruthman. “The machine’s 28 000 kg payload with a dump body capacity of 18,1 m³ also fits the bill for the customer’s production requirements. The 6-cylinder Liebherr engine with a 12-litre displacement, producing 265 kW of power, has been praised on site for delivering enough power when needed.”
Another TA 230 operating in South Africa has been deployed in a chrome application in Limpopo. Delivered in late 2023, the machine has so far performed beyond expectations in what is known to be an abrasive application. The feedback from the customer, confirms Ruthman, has been very positive, with prospects of delivering more units in the near future.
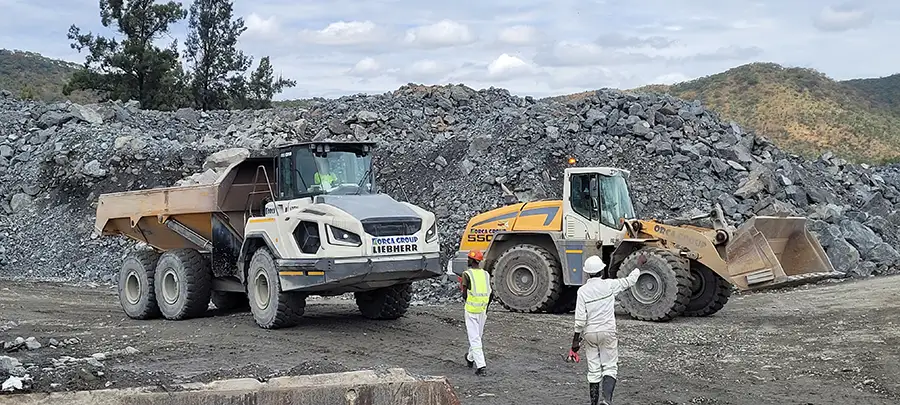
Why TA 230?
Several customers who have purchased the TA 230 to date have expressed satisfaction with Liebherr’s new machine concept, which has been developed especially for challenging off-road applications. Modern designs in the front-end area create maximum ground clearance for greater off-road performance.
The newly designed articulated swivel joint creates sound off-road capability; it allows independent movement of the front and rear ends, thus ensuring maximum manoeuvrability. The positive-locking swivel joint with tapered roller bearing is perfect for the shear stresses associated with tough underfoot conditions, while it also withstands maximum loads and provides optimal force distribution.
The front and rear axles of the machine are secured using sturdy A-rods at the articulated swivel joint and at the rear end. On front, the truck uses hydro-pneumatic suspension for maximum comfort, which is key to the smooth driving. The shock absorbers at the articulated swivel joint and the position of the separate and oscillating A-rods of the rear axles at the rear end, provide maximum ground clearance.
Powered by a 265-kW 6-cylinder Liebherr engine with a 12-litre displacement, the TA 230 Litronic is driven by an automatic 8-speed powershift transmission which ensures optimal force distribution. The machine impresses with great driving performance and massive pulling force, even in the most difficult ground conditions and on challenging gradients.
“A combination of balanced weight distribution, permanent 6 x 6 all-wheel drive, solid, flexible mounting and large bank angle as well as the machine’s high ground clearance, enable the TA 230 Litronic to deliver unparalleled performance on uneven terrain,” says Kudumba.
The actively controlled inter-axle differential locks mean that the Liebherr TA 230 has automatic traction control. As soon as one axle experiences wheelspin, it is decelerated, and the traction is intelligently redistributed to the other axles. In addition to maximum forward drive, this reduces the power requirement and therefore translates into lower fuel consumption.
Efficiency is further enhanced by the smart gear selection, which enables the machine to adjust automatically to its current speed and load to ensure optimum torque and fuel consumption at all times. The machine therefore automatically reduces its fuel consumption per tonne of transported material.
With productivity in mind, the optimised trough ensures that more material can be moved in a short time. The front of the trough – designed for the effective transport of a 28-t payload – is straight and the sills are low so that loading with a wheel loader, for example, is easily possible across the entire length of the truck.
A standard Liebherr weighing system shows the current payload during loading on the display in the operator’s cab, helping eliminate guesswork in loadout processes. An optional loading light on both sides at the back of the operator’s cab shows the loading level outdoors.
In order to accelerate the release of the material during unloading, the inner edges of the new trough are tapered. The two tipping cylinders at the side give the TA 230 Litronic high tipping pressure. The load can be tipped against the slope easily and quickly.
“During transportation, the long chute at the end of the trough ensures minimal material loss. The trough volume can be increased with the optional tailgate. Thanks to the large opening width, tipping of large and bulky transported material is easily possible. Even with the tailgate the overall width of the TA 230 Litronic is still below three metres, which allows the machine to be easily and quickly transported on a lowbed truck,” concludes Ruthman.