Given the nomadic nature of their operations, crushing and screening contractors place high value on mobility and transportability of their plants. Bearing that in mind, Weir Minerals Africa’s WMWP concept takes both these parameters to a whole new level.
In an exclusive interview with Quarrying Africa, Masekwameng explains that wheeled plants have always formed part of the Trio crushing and screening offering and make use of Weir Minerals’ Trio crushers, screens and material handling solutions. However, the solution has been completely redesigned to suit new market dynamics.
“Our wheeled plants have been used across the world in sand and aggregates by clients who require the flexibility of a mobile plant without the complexity needed for additional maintenance obligations of components such as diesel engines and associated tracks on the mobile unit itself. We have found this concept to be a good solution for crushing and screening contractors who want to be able to move their equipment from site to site at short notice,” she explains.
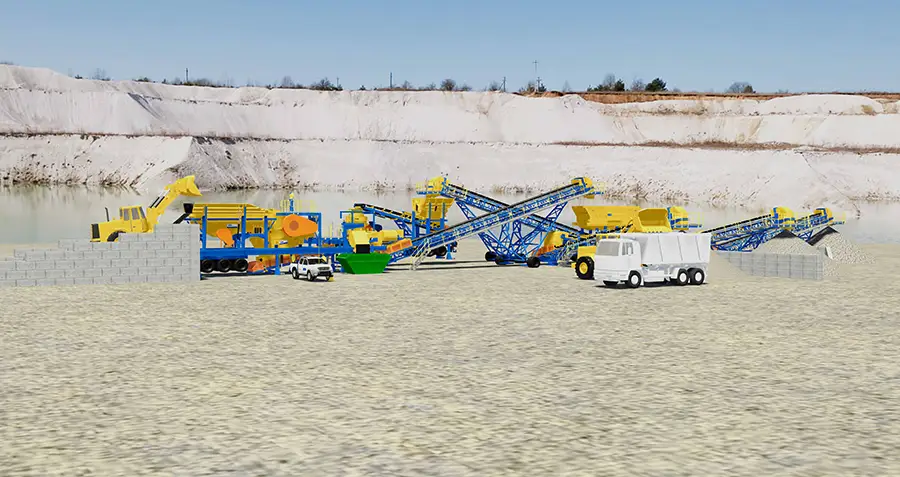
Intended markets
Commenting on targeted applications, Masekwameng says the wheeled plants concept is primarily intended for the construction market, as well as the mining sector, particularly where clients require short-term solutions to help boost production rates during commodity upswings, without constructing a new static plant over a longer lead time. Weir Minerals Africa will use the upcoming Electra Mining exhibition in September this year to showcase one of the first units.
“Many of our clients in the construction market are looking for solutions that allow them to easily relocate their plants to infrastructure development hotspots. Once they get to site, they want to mobilise quickly and start operating immediately,” says Masekwameng.
This, she adds, means that clients do not always have the time to go through a design and delivery period associated with a more permanent, fixed plant which can take months to complete. A solution that can be easily transported and erected on site immediately wins the day in such a scenario. This is particularly true for markets outside of South Africa where commercial quarries are generally few and far between, with borrow pit type of operations more prevalent.
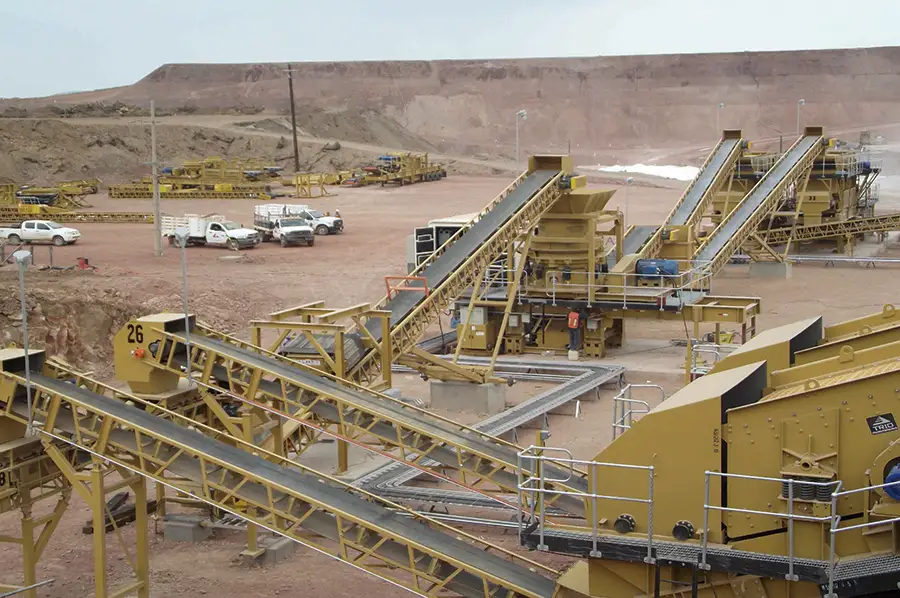
System in detail
Weir Minerals’ wheeled plants are available in various configurations, starting from primary crushing solutions comprising a hopper, a vibrating grizzly feeder and a jaw crusher, to secondary crushing and stations which consist of a vibrating screen and a cone crusher. To combine these solutions, one can use simple mobile conveyors to configure a plant that is capable of producing aggregates for various end-use requirements.
“More importantly, we utilise equipment that is within the dimensions and weights that can be accommodated on a multi-axle trailer,” she emphasises. “With that comes the limitation of the amount of mass that can be accommodated per axle, in addition to legal road limits on width and height. The machines that we use for our wheeled plants are in the 50 to 350 tonnes per hour (tph) range. Once you go bigger than that, the equipment gets too heavy, and the solution becomes more like a fixed plant.”
Commenting on some key features of the system, Masekwameng makes special mention of the unique hydraulic and mechanical deployment system which requires minimal truck-mounted cranage during site installation. Its purposefully designed hydraulic leg system raises the plant from wheels, levels it and installs main supporting legs without any cranes being required.
When in operation, the plant is supported by structural support legs with the operational load removed from wheels/axles and hydraulic lifts for working safety and structural stability, as well as having reduced noise and vibration. All connections are done with structural pins and bolted connections, resulting in seamless integration of all components. The unique positioning bogey system makes final site-placing of modular wheeled units and conveyors simple and efficient.
The modular primary jaw crushing units are fed directly with excavator or front-end loaders with optional hopper extension for direct dump truck feed. The jaw wheeled units include an integrated overband magnet system for removal of tramp metal. A surge hopper unit with an integrated belt feeder could be added in circuit to ensure proper choke feeding of cone crushers for optimal crushing quality and performance.
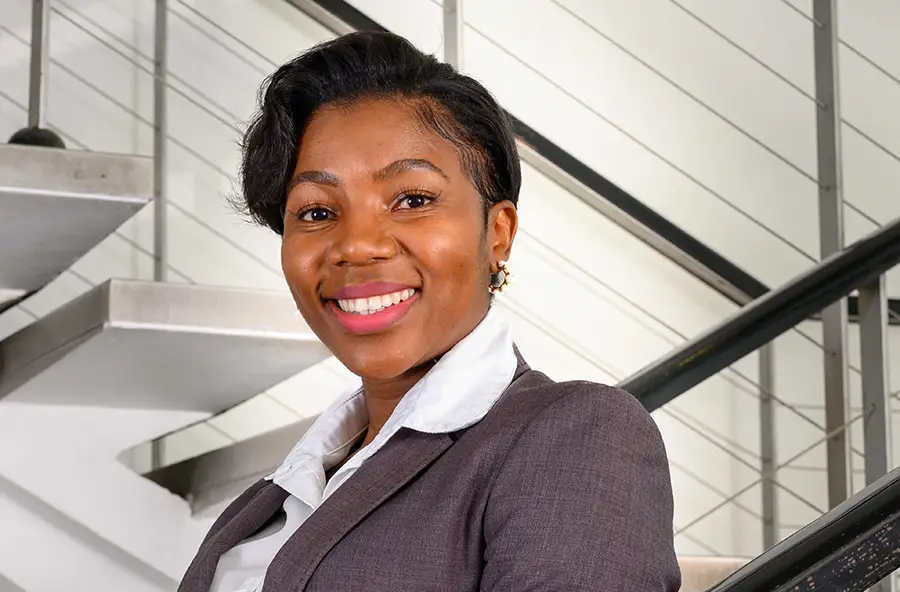
Benefits abound
According to Masekwameng, one of the major benefits of wheeled plants is that they eliminate the complexity of having a diesel engine as part of the unit as well as tracks which require additional maintenance over and above the crushers and screens themselves.
“With wheeled plants, our customers can focus their maintenance attention on equipment that is core to their operation – crushers and screens – as the availability of these machines is what earns them money. Wheeled plants can also be transported on the highway depending on the size and road regulations within the client’s jurisdiction. That means customers only need to hook the plant on to the back of a truck and off they go,” she says.
By their nature, wheeled plants are portable crushing and screening solutions with minimal civil requirements, which translates into both time-savings and reduced operational costs for customers.
These solutions can be transported on road with standard horse kingpin connection (South African road transport requirements) or containerised (subject to main equipment size) for shipping to remote sites where sea freight is more economical.
In addition, these plants are designed with safety in mind and ease of maintenance as the highest priority. Various crushing and screening wheeled plant modules seamlessly integrate together with the Weir Modular Conveyor System (WMCS), all powered from a central wheeled generator/master control wheeled unit, with cable racking and routing allowance already provided for.
“WMWP combines all the features and benefits of the robust Trio and Enduron range of equipment in an easy to deploy and relocate, complete crushing and screening solution,” says Masekwameng.
The future
Masekwameng says, given that the sand and aggregates required for infrastructure development are generally high-volume, low-value products, it is difficult for contractors to factor in transportation costs for these materials and still turn a profit when crushing projects are far away from construction sites.
“As such, it becomes important for them to move around to where there is construction development. In our view, demand for solutions that can be easily transported and quickly mobilised is going to increase as the world turns to infrastructure development as a tool to foster economic recovery and development,” concludes Masekwameng.