Reducing the environmental impact of the mining industry has become the main priority for the coming decades. While mines and their contracting counterparts will explore a range of new technologies to drive their Environmental, Social and Governance (ESG) agendas, battery-electric equipment is proving to be the best alternative to traditional diesel-powered mining machines.
With that in mind, a strategic quadripartite alliance between Chinese original equipment manufacturer (OEM) LiuGong, its South African dealer, Burgers Equipment & Spares, mining company Samancor Chrome and mining contractor M Civils, has brought the first LiuGong 856H-E battery-electric wheel loader to Africa. At the launch event attended by Quarrying Africa on May 7, 2024, the parties used the same platform to sign an agreement of sale for the first 856H-E.
The collaborative effort between the four parties materialised on the back of M Civils’ 2023 visit to LiuGong’s manufacturing facility in China as part of the 2023 LiuGong Global Dealer Conference, confirms Petrus van Blerk, Project Manager at M Civils.
“Upon seeing the 856H-E for the first time in China, we immediately started conversations with Burgers Equipment & Spares and LiuGong about the possibility of bringing the machine to South Africa for a trial run on a mine. The idea also appealed to our long-time client, Samancor Chrome, as part of its own ESG targets. As a mining contracting company that thinks innovation, this makes sense in terms of reducing our cost of operation, while delivering the same production for the mine,” explains Van Blerk.
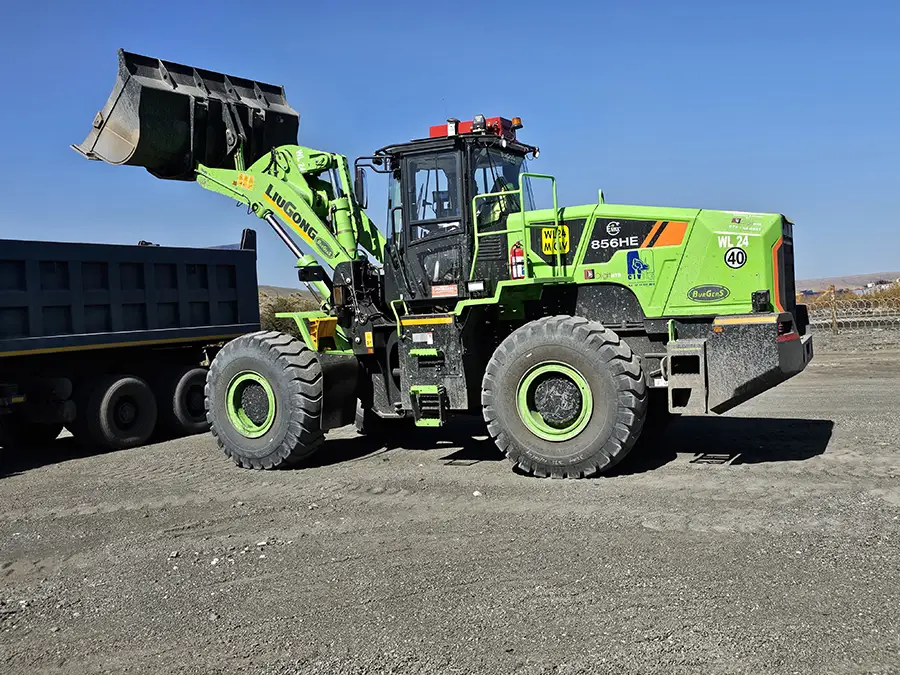
Pioneering the ‘green’ revolution
Tiaan Burger, MD of Burgers Equipment & Spares, says the deal is exciting and allows the company to pioneer the ‘green’ revolution in the local earthmoving equipment sector. “We are excited to bring the first ever production-size battery-electric piece of earthmoving equipment to Africa on a commercial basis. We do not believe that this will be a high-sales volume machine, but it allows us to support the mining sector’s sustainability drive and play our part in the protection of the environment,” says Burger.
Li Yi, GM of LiuGong Machinery South Africa, says the OEM has over the years demonstrated its commitment to sustainability by leading the battery-electric equipment revolution in China, the biggest battery-electric vehicles (BEV) market in the world. Since 2014, the company has made astronomic investments into research and development (R&D) of intelligent equipment solutions. In 2019, LiuGong rolled out its first generation 5-tonne (t) electric wheel loader, before using CONEXPO 2020 to introduce the 856H-E to the global market. To date, the company has already sold in excess of 3 000 battery-electric machines in over 30 countries.
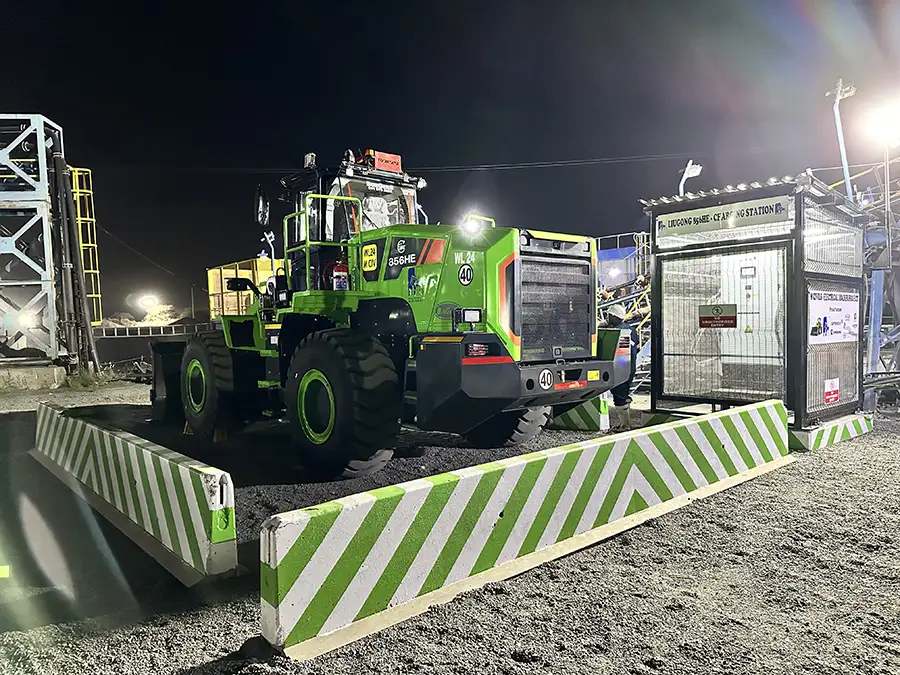
Hard at work
As part of the trial phase, M Civils has deployed the machine at Samancor Chrome in the North West Province of South Africa. When Quarrying Africa visited the site in mid-June, the machine had been hard at work for just over two weeks and had already clocked over 100 hours with no teething issues whatsoever.
“We have deployed the machine to load trucks and perform stockpile management duties on site, where it is loading different types of processed chrome products and waste rock,” explains Van Blerk. “In the next few weeks, we also plan to deploy it to load trains, which will give us a good indication of the machine’s performance in a non-stop working environment.”
During the first two weeks of operation, the machine had performed beyond expectations. Feedback from operators had been particularly positive – they had found the machine to be as powerful as its diesel counterpart. More importantly, operators are happy with the quiet nature of the machine. The electric motor is smoother and quieter than internal combustion engines, which means that it produces less noise and vibration. This provides for a safer working environment for operators, as it reduces their risk of developing musculoskeletal disorders.
While it is too early to make an informed comparison in terms of the cost of operation between the new electric machine and its diesel equivalent, Van Blerk says early indications are that the machine is cheaper to run just in terms of the diesel/electric comparison.
“Ideally, we would like to run the machine for at least three months to get a clear picture of the actual savings. The big thing, however, will be the cost of maintenance. We believe the cost of maintenance for battery-electric equipment will be a lot lower than for the diesel-powered machines. Electric machines have fewer moving parts than those powered by combustion engines, which means less maintenance. In addition, battery-electric parts are usually more reliable than diesel-powered parts, and this can significantly reduce the cost of operation,” says Van Blerk.
Apart from the reduction in operational costs, Burger believes that the main advantage of battery-powered equipment in the mining industry is its environmental friendliness as it does not produce any greenhouse gas emissions. By switching to battery-electric equipment, mines and their contracting counterparts can significantly reduce their environmental impact and improve the health of their workers.
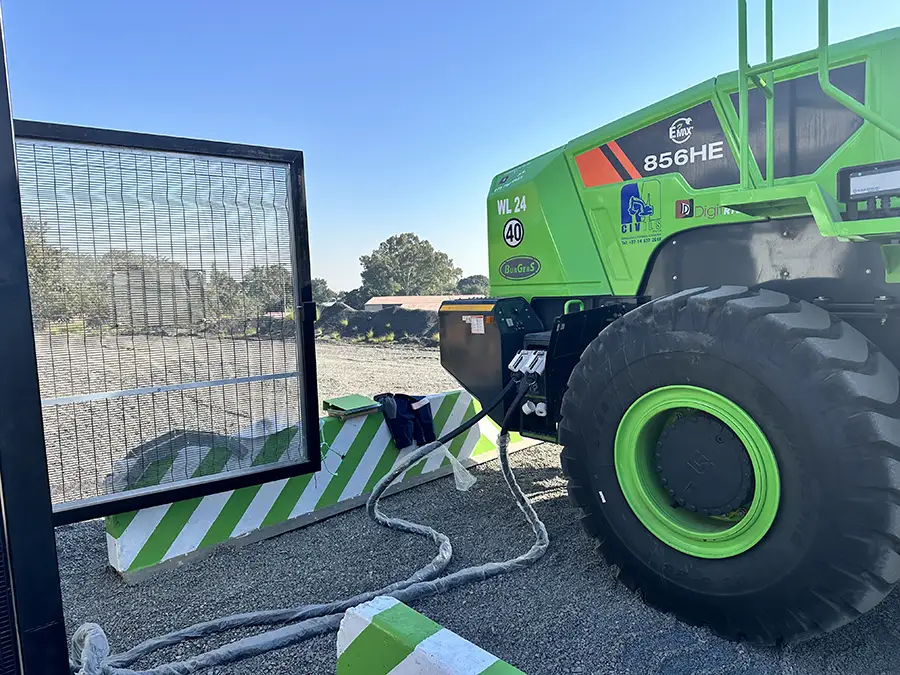
Putting in the shift
Powering the 856H-E Max is a 423-kWh large-capacity lithium-iron phosphate battery from battery manufacturer CATL. The battery, confirms Burger, is made up of ten individual battery packs. The motor has a kilowatt peak power output of between 160 and 180 kW. According to the OEM, the machine can work ten hours in light applications and eight hours in heavy duty applications. With the Intelligent Battery Management System, it can be fast-charged in 90 minutes.
At Samancor Chrome, M Civils works 24/7, using three eight-hour shifts. During weekends, the contractor deploys two 12-hour shifts. During the first two weeks of operation, the machine has completed both the eight- and 12-hour shifts on a full charge without discharging completely. This is despite the heavy nature of the chrome material that it handles.
“The shift changes provide an opportunity to recharge the machine before each shift. We use a double input charging system, which fully charges the machine in about 60 to 90 minutes depending on the discharge state of the battery. This means that the machine is fully charged before the start of every shift,” explains Van Blerk.
Tailored components
For this particular application’s requirements, the 856H-E has been equipped with several custom components. For example, because it is deployed to handle a chrome product, which by its very nature has a higher density than several other ores, bucket size has been reduced from the standard 3,5 m³ to 2,5 m³. Because chrome is also quite abrasive, a high abrasive wear package has been added to increase the longevity of the bucket.
In line with the Department of Mineral Resources and Energy’s safety regulations, the machine has been equipped with a proximity detection system (PDS) through a partnership between Nerospec and Schauenburg Systems. The mine already uses this technology on some of its existing trackless mobile machinery. However, the 856H-E becomes the first piece of equipment on site to be Level 9-compliant. The machine has also been equipped with a fully automatic fire suppression system.
In addition, the machine has been installed with the new flagship Loadrite L5000 SmartWeigh system supplied by Loadtech. With its wi-fi readiness and touchscreen interface, the L5000 provides more convenience, accuracy and efficiency in loading operations. The system’s wireless connectivity enables seamless data transfer and real-time monitoring. The touchscreen interface offers intuitive and user-friendly navigation, enhancing ease of use for operators.
While operation of the machine is quite similar to that of the conventional 856H wheel loader, Van Blerk says M Civils’ operators had to undergo a familiarisation training programme facilitated by LiuGong and Burgers Equipment & Spares.
Key specs
The 856H-E MAX features intelligent controls and an operator-focused design, including load-sensing hydraulics, an EAT700 transmission with an electro-proportional valve for fast, smooth shifting and independent control of the dual-motor drive for added hydraulic lift.
The LiuGong Intelligent Auto Digging System automatically carries out repetitive digging cycles to reduce operator fatigue. Its electric control box also improves transmission efficiency compared to conventional machines, the company says.
“The 856H-E Max offers the highest levels of safety, visibility and comfort, including full ROPS & FOPS protection and a cab design that significantly reduces dust and noise contamination. Its reliability is reinforced by the IP67-rated wiring harness and waterproof integrated battery package,” concludes Burger.