Given that transportation, on average, accounts for about 30% of total mining costs at most opencast operations, mines and quarries are putting efficiency of their hauling gear at the top of their list of priorities.
While construction type tippers have traditionally been deemed ideal for light duty applications such as ore rehandling and moving processed material between processing plants and stockpiles, there is a growing acceptance that these trucks are equally robust enough to take on arduous applications such as hauling run of mine (ROM) material from the rock face to the processing plants.
A case in point is Scania’s new G460 XT heavy mining tipper, which headlined Scania South Africa’s exhibit at Electra Mining Africa, the premier mining show which took place from 2-6 September at the Johannesburg Expo Centre. Vinesh Kalu, Segment Manager – Scania Mining at Scania South Africa, tells Quarrying Africa that the heavy mining tipper is built to handle in-pit haulage operations in mines and quarries.
“I am confident that the new Scania heavy mining tipper will add value to our customers’ operations,” says Kalu. “Today’s mine owner has to grapple with the everchanging face of the market. The new requirements are very clear: operations have to simultaneously cut their emissions and meet efficiency targets or face extinction. With Scania’s unmatched fuel economy and improved payload, the heavy mining tipper offers lower operational costs, making a big difference in our customers’ margins and bottom lines.”
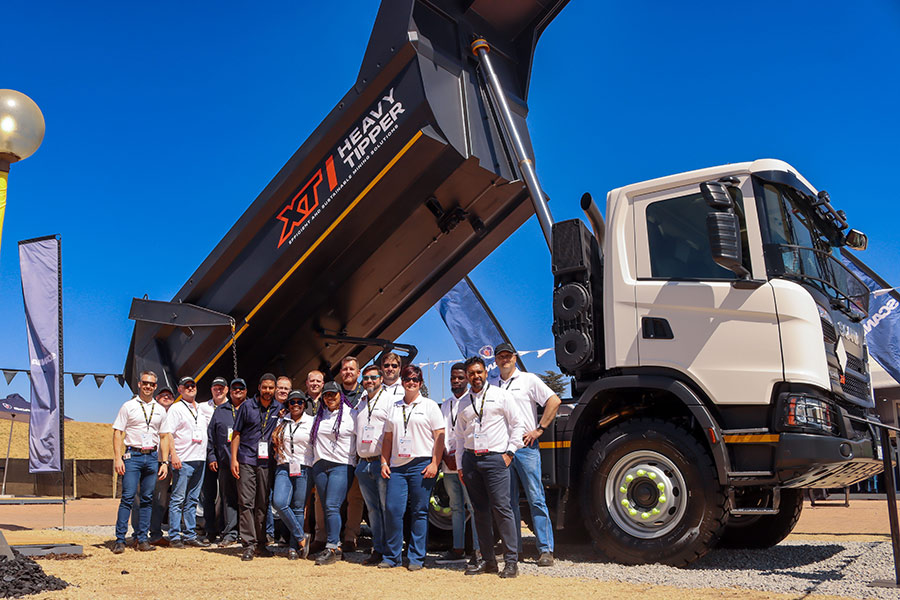
Payload matters
One of the major talking points on the new heavy mining tipper is the increased 60-t gross vehicle mass (GVM) with a rated payload of 40 t, which plugs the payload gap between conventional tipper trucks and their yellow metal counterparts. With its excellent equipment-to-payload ratio and greatly improved technical availability, the new offering can be specially tailored to meet any type of mining-specific demands.
The mining tipper’s 40-t payload, says Kalu, is the most prominent improvement on the new offering compared with its predecessors. The increased truck payload enables mining and quarrying operations to consolidate loads and thus reduce the amount of vehicle movement required to distribute a given quantity of material on site. This yields economic, safety and environmental benefits. In addition, fewer trucks on site translate into less operating costs related to maintenance.
To sustain the increased payload, the new XT mining tipper benefits from a more robust suspension. The new mining tipper is equipped with heavy-duty rear axles with cast-iron housings to stand the test of challenging, rough mining conditions. Both rear axles are equipped with shock absorbers to improve traction and comfort.
“Heavy duty suspension, shock absorbers and anti-roll bars offer increased stability. The Scania Retarder improves braking performance and reduces wear on the wheel brakes, especially on downward slopes,” says Kalu.
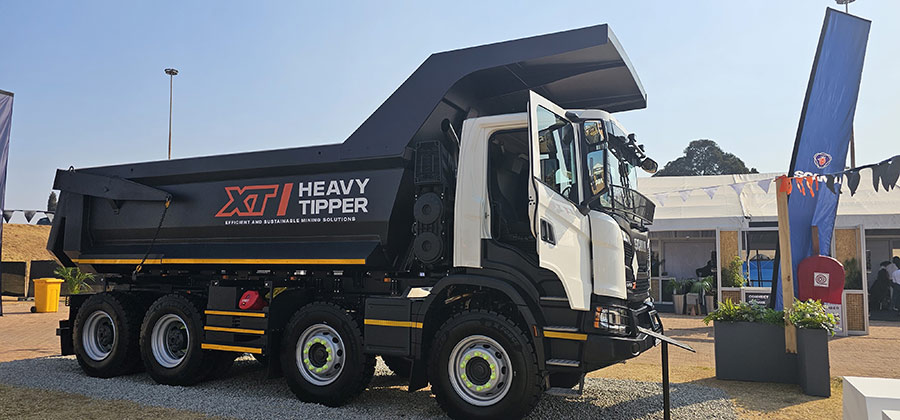
Efficient operation
Another value proposition of the new G460 XT heavy mining tipper is its fuel efficiency, a critical parameter, not only to help mining and quarrying customers reduce their cost per tonne, but also to meet their emission reduction efforts in line with their Environmental, Social and Governance (ESG) targets.
“The G460 XT mining tipper engine delivers high torque output as well as outstanding fuel efficiency,” says Kalu. With improved engine performance and leading emissions control through the Scania Twin-SCR system, the Scania Super 13-litre engine sets a new industry standard for brake thermal efficiency. This contributes to unrivalled powertrain fuel savings of 8%.
Dual overhead camshafts have been introduced to enhance gas exchange and deliver unrivalled performance. The high-intake air system has been developed specifically for dusty and exposed environments – this solution provides the engine with the cleanest air possible.
The Scania Opticruise gearbox ensures smooth automated gear changing, thus reducing driver fatigue. Scania Opticruise, one of the first automated gear changing systems on the market, has been refined in many steps over the years, and is now one of the smoothest and smartest systems on the market.
For operations that require the driver to be in charge for specific manoeuvring, Scania has introduced Clutch on Demand, a new performance step for Scania Opticruise. Clutch on Demand has an additional clutch pedal for convenient use in special conditions, otherwise the system works as an ordinary automatic clutch system. The new lay-shaft brake provides faster and smoother gear changes to maintain both engine torque and speed.
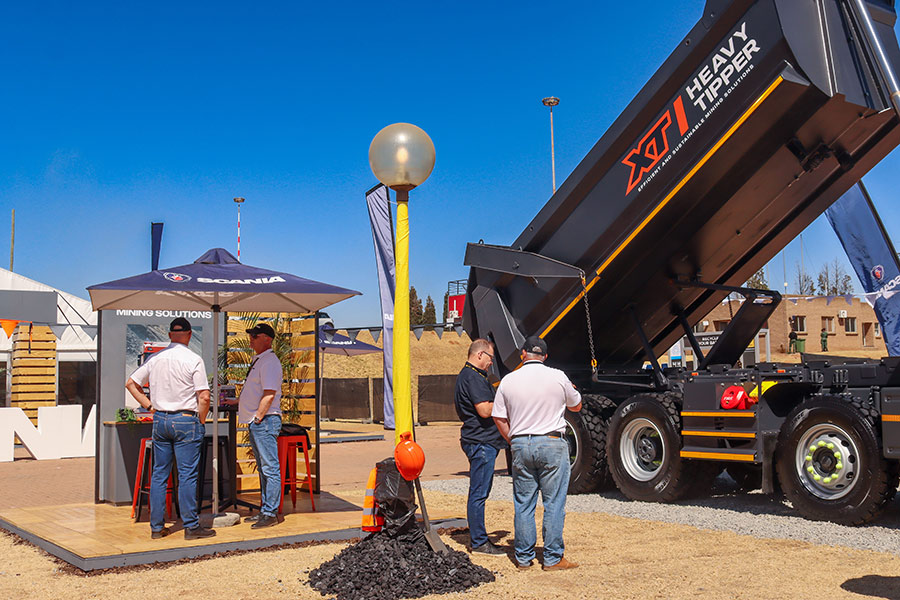
Body improvements
To meet specific market requirements, Scania South Africa has partnered with Efficient Engineering to develop the tipper body. The enhanced substructures of the bin are able to absorb the impact of the material thrown into the body. The material used to build the bin is suited for heavy duty mining. The projected life of the body has been greatly improved through addressing all the stress points of the bin.
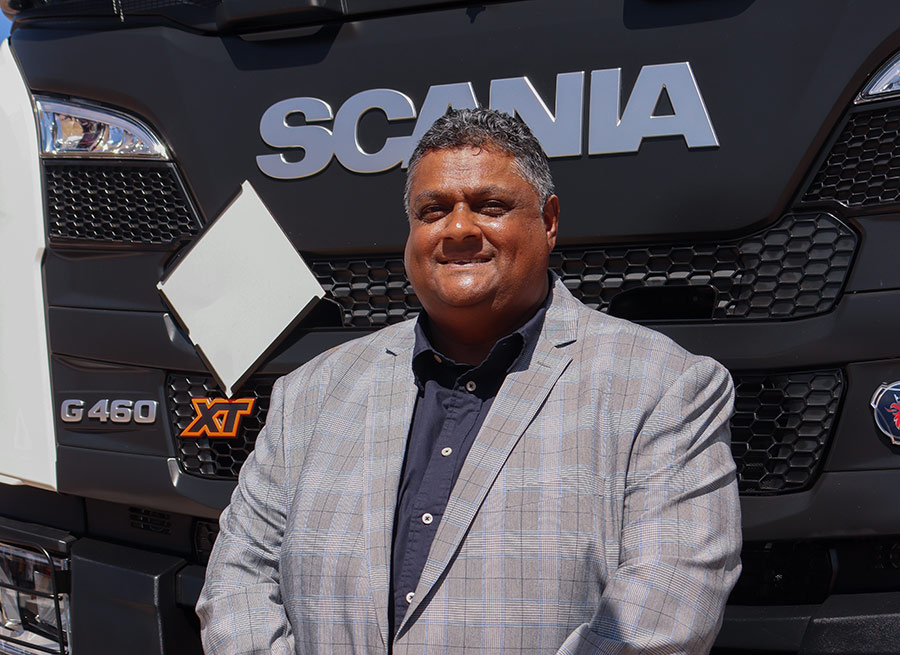
“We have partnered with Efficient Engineering due to its understanding and experience in the mining industry. Efficient Engineering has been building dump bodies for over 30 years. The company has successfully met Scania Mining’s requirement in this build – which is to develop a light yet rugged body that maximises payload efficiency,” concludes Kalu.