RT Loaders is a division within the larger Reinhardt Transport Group (RTG), responsible for loading both RTG and other transporters’ trucks at various loading points at mines. Although the group has always had this function within its ranks, it was previously never a dedicated division. Following the expansion of the loading fleet in recent years, a decision was taken some two years ago to establish a dedicated division to look after the yellow metal fleet deployed at the group’s loadout operations across various mines.
With a fleet in excess of 1 000 trucks across its various renowned transport brands – Reinhardt Transport, Chrome Carriers, Transmac, Amalgamated Bulk and S Hauliers – RTG is one of the largest privately-owned side tipper transporters on the African continent. The group specialises in bulk transportation of commodities, including chrome, coal, manganese, fertilisers, metallurgical coke, ferro chrome, iron ore, mill scale, grains and gypsum, across South Africa and neighbouring countries.
Headed by divisional manager Gordon Losper, RT Loaders operates a large fleet of 23 Lovol FL968H loaders, four skid steers, four water bowsers, one dozer, one excavator and about nine light-duty vehicles (LDVs). Losper tells Quarrying Africa that the wheel loaders are responsible for loading trucks at various loading points. Given the criticality of these loadout operations, which are responsible for handling about 674 000 tonnes per month or 8-million tonnes per year, on average, the company has over the years trusted the accuracy and precision of Loadrite on-board weighing systems to eliminate guesswork in its loading operations.
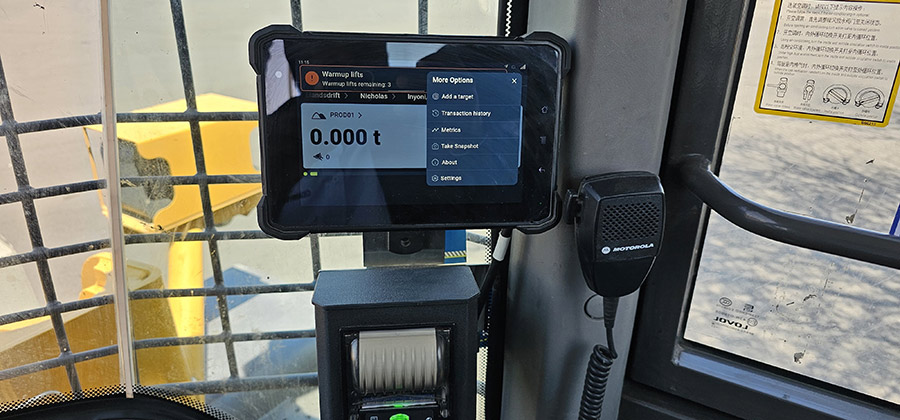
Why weighing systems?
According to Losper, the Loadrite systems have transformed the way in which RT Loaders conducts its loadout processes. Traditionally, operations relied on weighbridges alone, which are well known to be prone to product errors and inaccurate weight challenges.
In addition, a key operational headache in conventional operations was the loading of incorrect tonnages in trucks, which resulted in unwanted downtime. In an event that trucks were under- or over-loaded, this would only be discovered at the weighbridge. Consequently, the truck would need to turn back to the loading point to load the correct tonnage. This resulted in unnecessary downtime and high costs associated with re-handling of material.
Loadrite onboard weighing systems are designed to eliminate these problems, which is why RT Loaders has fitted all of its 23 wheel loaders with the technology. Loadrite on-board weighing systems are used to calculate the weight of material in a loader’s bucket, relay this information to the operator and record the weight for later use. The data acquired from tracking the amount of material moved per hour is then used internally as part of an overall business analysis to measure productivity and set benchmarks.
“One of the reasons we opted for Loadrite from the onset is the accuracy and precision of the technology, which is very important to our operations. Although Loadtech generally specifies a single calibration once every three months, we calibrate our systems once every month to keep them in tip-top condition and maintain high levels of accuracy,” explains Losper.
Having access to data from load weighing systems, adds Losper, is key to ensuring efficient and productive loadout operations. The insights derived from the Loadrite systems can be turned into actionable changes to improve efficiency and productivity.
“The technology is more than just a load weighing system; in our operations we also use the Loadrite system to manage operator performance, which informs our bonus structure. Available data from the system shows the tonnages each operator has loaded. Those who go the extra mile are rewarded, based on a prescribed bonus structure we have in place,” says Losper.
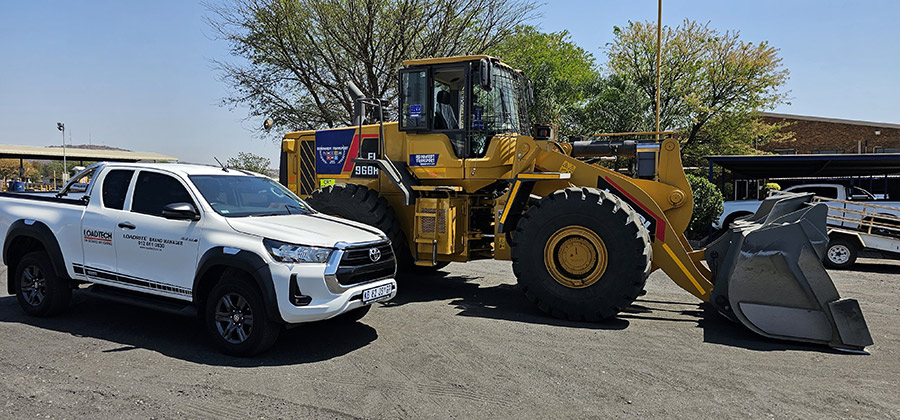
Enter L5000
For its wheel loaders, RT Loaders maintains a systematic replacement cycle where machines are traded in for new ones once they reach 8 000 hours. Loadrite systems fitted on these machines are simultaneously traded in for new units to be installed on the new wheel loaders. Loadtech, the sole supplier of the Loadrite system in sub-Saharan Africa, has an excellent buy-back programme for its Loadrite on-board weighing systems.
While the majority of the existing loaders within RT Loaders’ fleet are installed with the Loadrite L3180, the company is one of the first recipients of the new L5000 in South Africa, with two of its wheel loaders – one in Rustenburg and the other in Steelpoort – running with the system. Quarrying Africa recently visited RTG’s operation in Rustenburg, where one of the loaders installed with the L5000 is deployed to load trucks. Losper and his team are particularly happy with the L5000’s advanced features.
“We are impressed by the L5000’s real-time data monitoring and analysis capabilities,” explains Losper. “The system’s wireless connectivity enables seamless data transfer and real-time monitoring. The touchscreen interface offers intuitive and user-friendly navigation, enhancing ease of use for our operators.”
Loutjie van der Merwe, Loadrite divisional manager at Loadtech, says with its WiFi readiness and touchscreen interface, the L5000 is revolutionising the industry by providing more convenience, accuracy and efficiency in weighing operations.
“Overall, the L5000 SmartWeigh system is poised to streamline weighing processes, improve productivity and provide valuable insights for better decision-making in various industries. Its innovative features have the potential to change the way weighing systems are used and perceived, making Loadrite a frontrunner in the market,” says Van der Merwe.
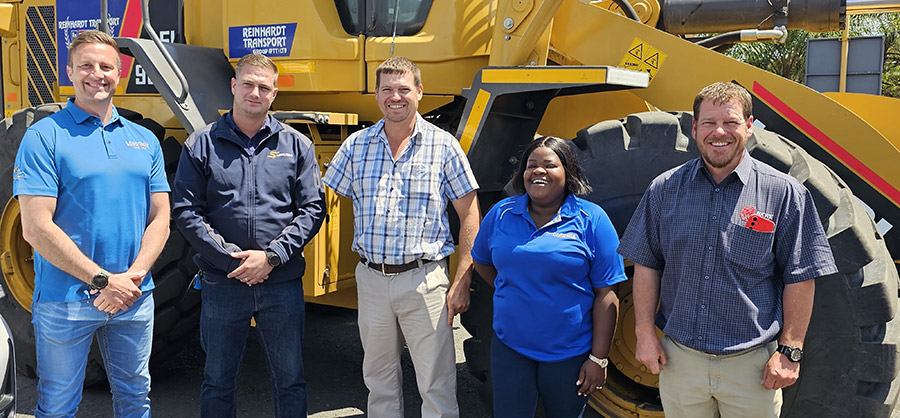
Support matters
Apart from the accuracy and precision of the Loadrite technology, RT Loaders is also pleased with the backup support from Loadtech. “Over the years, dealing with Loadtech has been a breeze, which is why we also use their Loadrite systems in our Performance-Based Standards (PBS) trucks,” says Losper. “Loadtech understands the support we need for our 24/7 operations and it is always there to provide the service we need.”
In addition, Loadtech has a dedicated data specialist who works closely with RT Loaders and other customers to help interpret and make sense of the data generated by the Loadrite systems. This makes a significant difference in customer operations. Data is one thing and making sense of it is quite another. Having a dedicated data specialist is therefore a big benefit for customers who need to translate data into workable solutions for their businesses.
“In recent times, we have also grown our technical team, which is key to our support capabilities. Consequently, we can now guarantee our customers quick turnaround times for any technical issues. We also offer continuous operator training and stay connected with all our customers,” concludes Van der Merwe.