One of the most common causes of unscheduled downtime on conveyor systems is conveyor belt mistracking. Belt misalignment causes spillage, belt edge damage, damage to the structure, increased power consumption and increased labour costs. Misaligned belts will ultimately result in lost production, increased operating costs and safety hazards.
Although there are many factors that cause belt misalignment, belt mistracking issues are often attributed to conveyor belts alone, which in most cases is unjustified as conveyor systems are more than just belts. It is therefore essential to be fully aware of the basic characteristics of the different belt tracking components and for these to be employed correctly. Key to the belt running ‘true’ are both structural and non-structural factors.
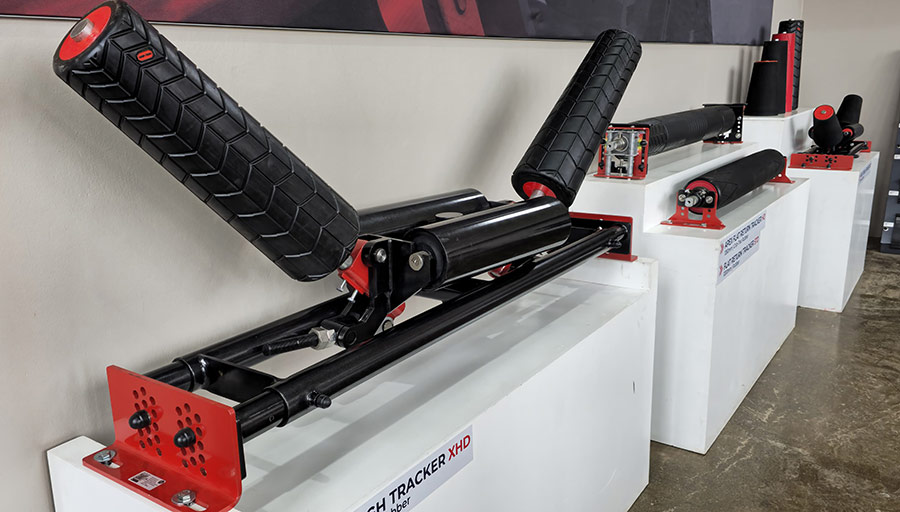
Belt practices
On the structural front, says Van der Westhuizen, it is important to make sure that all the structural conveyor components such as pulleys, idlers, take-ups and the supporting structure are properly aligned at all times. In fact, these should be the principal areas of concern whenever trying to identify belt tracking problems. All pulleys, snub rollers, troughing and return idlers must be square with the frame parallel to each other, and also be level.
“Constant condition monitoring of conveyor components is one of the best practices in ensuring correct belt tracking at all times,” says Van der Westhuizen. “Always check the condition of your pulley laggings and idlers. Make sure the idler frames are square and straight. What we have observed in many instances is that some of the idler frames are bent during installation, causing incessant belt misalignment problems during operation. It is therefore crucial to ensure that the idler frames are square and straight from the onset.”
In addition, to be properly steered, the belt needs to be in full contact with the idlers and pulleys at all times. A lack of contact or having material in between these components will definitely result in belt mistracking.
One of the critical non-structural factors to eliminating belt mistracking in conveyor systems is housekeeping. Cleanliness is essential to good belt tracking. “For me, the number one best practice in belt tracking is housekeeping; if something is clean, it works better,” says Van der Westhuizen.
Excessive material buildup, he adds, can cause misalignment, especially on idlers and pulleys. It can also cause the conveyor belt to jam or stop altogether, resulting in production delays and lost productivity. In the worst case scenario, the excess material can damage the belt itself, leading to costly repairs or even to the need for replacement. This is particularly the case in quarries, where there is a lot of fine dust and water in the processes, which exacerbate accumulation of material on idlers and pulleys.
Fitt agrees, saying that regular inspection and maintenance of the conveyor plays a crucial role in preventing the possibility of mistracking occurring. It is essential to regularly inspect idlers and their rollers to ensure the idlers are aligned properly and the rollers are running evenly.
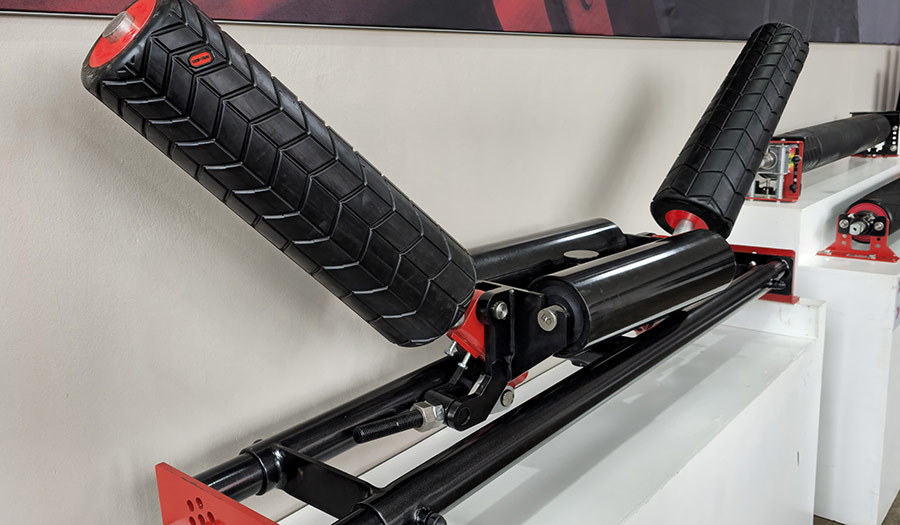
Eliminating misalignment
From the onset, the birth of Tru-Trac Rollers nearly 30 years ago was informed by the need for continuous innovation to help industries deal with belt misalignment issues, says Fitt, thus allowing customers to achieve maximum conveyor system performance, resulting in optimal production output at the lowest possible cost.
Over the years, Tru-Trac has continuously evolved its offering to provide the industry with the very best of solutions to solve common conveyor problems such as belt misalignment. A case in point is the patented Tru-Trac Apex Taper Trough Tracker range.
“Designed for high performance, the Apex Taper Trough Tracker is a culmination of nearly 30 years of experience and two years of research and development, followed by a stringent testing regime in tough operating environments across commodities. We are glad to finally offer the market with what we believe is the next leap forward in belt tracking technology,” says Fitt.
One of the major talking points on the Apex Taper Trough Tracker is its proven performance. The combination of tapers and the unique centre pivot offers fast, autonomous and continuous tracking in all conditions.
“The Apex Taper Trough Tracker is a radical upgrade of our previous systems. The upgraded system now includes enhancements for durability and better protection against dust, especially in fine dust environments,” says Van der Westhuizen.
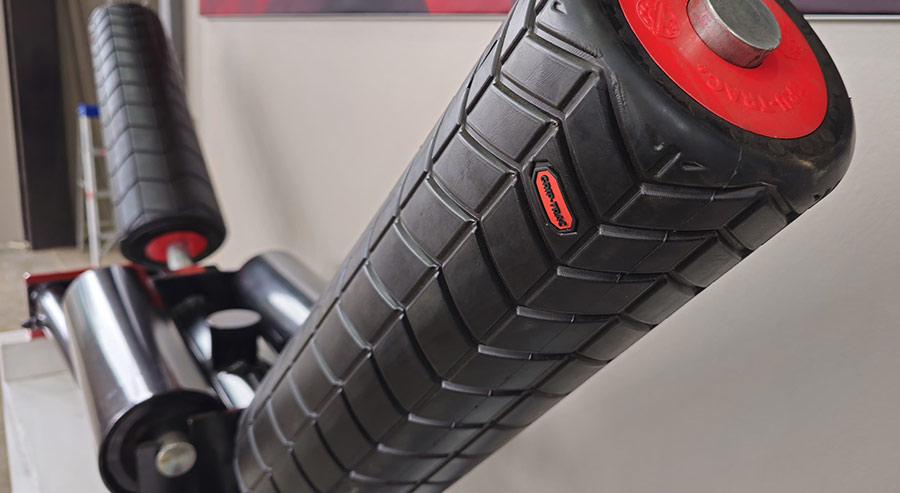
With its compact design, the Apex Taper Trough Tracker can be installed effortlessly in tight spaces, such as under hoods or on tripper cars. The new cantilevered wing roll and cradle replace the previous design’s protruding adjustment bolts, eliminating space constraints and potential safety hazards. Adjustments are now quick and straightforward, allowing for easy angle setting of the wing rollers.
“The Apex Taper Trough Tracker’s inline taper wing rollers are designed for compatibility with trough angles up to 60 degrees and can flatten as low as 10 degrees for easy installation and transportation. This is a significant upgrade to the maximum 50 degrees trough angle on the previous system,” says Fitt.
The flat-packed nature of the system allows for easy handling and installation. “The compact and flat-packed nature of the system also means that there is less wasted space in shipping containers/crates, which saves on shipping costs. This is important, especially given the rising shipping costs across several major trading routes globally,” says Van der Westhuizen.
In addition, the improved custom-compounded GRIP-TRAC™ rubber lagging and patented tread pattern on the wing rolls offer enhanced traction and tracking performance as well as extended working life of the replaceable wing rolls, further reducing total cost of ownership.
Increased responsiveness is yet another key benefit of the new Apex Taper Trough Tracker. The optimised centre of gravity and weight distribution offers improved stability, control and balance. This enhances sensitivity to belt misalignment and tracking performance by increasing efficiency and responsiveness.
“Belt misalignment is one of the biggest issues for quarries and mines. It can result in higher operating costs, capacity losses, unscheduled shutdowns, material spillage and unsafe operator conditions. We used Electra Mining Africa to showcase how the new Apex Taper Trough Tracker ushers in a new era in belt tracking technology and several clients who visited our stand were thrilled by the capabilities of this groundbreaking offering. Operations that are already running the system have also expressed great satisfaction with the exceptional performance of the Apex Taper Trough Tracker,” concludes Fitt.