There is a new player in the southern African crushing and screening market following SANY Southern Africa’s launch of its first ever range of mobile crushers and screens. At the time of writing, the company had brought the first unit in South Africa, a SANY SCIM1213RC6 impact crusher, owned and operated by Marodew Plant and Services, a young company that specialises in the rental of mobile crushing and screening equipment, as well as the building of static crushing plants.
As is the norm with any new brand, especially in a competitive market such as crushing and screening, the first machine was received with scepticism among some customers. Based on the experience of previously being a crusher operator, technician and eventually supervisor, Rodney Smith, one of the founding directors of Marodew Plant and Services, was from the onset convinced with the build quality and design of the SANY impact crusher.
Why SANY?
Although the SANY machine was completely new to this market segment, Smith and his co-director Wihan van Wyk were both convinced by the globally proven components that make up the crusher. For example, the SCIM1213RC6 impact crusher is powered by a 371-kW Isuzu engine, a Japanese motor that has proven itself across many functions in mining and construction equipment. The crushing chamber is made in Ireland, which is dubbed the “home of crushing and screening”. All the electrical components are from Schneider, a trusted global specialist in energy management.
When it comes to the build quality of the machine, says Smith, the SANY impact crusher is built on an excavator chassis, ensuring reliability. It also comes with an overload protection for the crusher. When a crusher is overloaded, components such as the crushing chamber, motor and bearings can experience excessive stress, leading to potential damage or failure. Overload protection therefore prevents this by automatically shutting off power when the load becomes too high, thus extending equipment lifespan, enhancing operational efficiency by minimising downtime due to breakdowns, and improving safety by mitigating risks associated with overstressed components.
Most of the SANY SCIM1213RC6 impact crusher’s components are electrically driven, doing away with hydraulically driven pumps. “The absence of hydraulic pumps increases the machine’s reliability and reduces downtime associated with hydraulic failures. In our experience, about 80% of breakdowns in hydraulic machines is related to the hydraulics,” says Smith.
“From the onset, we were convinced by the production capacity of this machine which, as a rental company that also executes contract crushing work, allows us to take on bigger jobs. The machine can take a feed size of up to 600 mm, producing between 150 and 450 tonnes per hour (tph), depending on the characteristics of the material,” adds Smith.
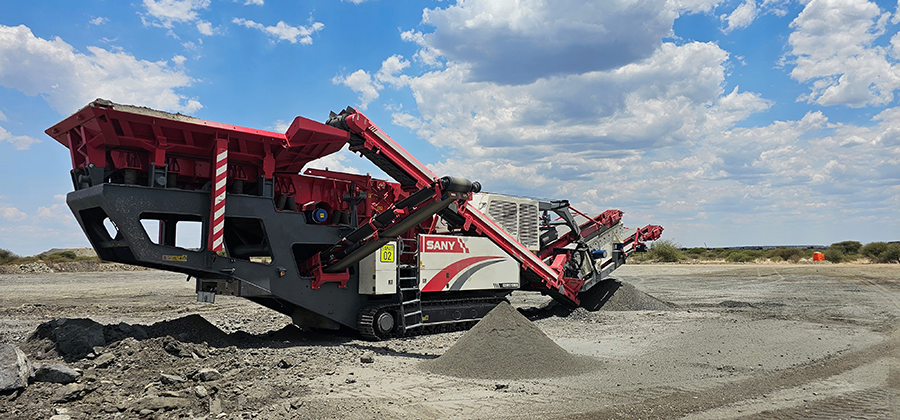
The proof of the pudding is in the eating
At the time of writing, Marodew Plant and Services had already run the machine for about nine months, initially in a coal application, before moving it into a chrome processing environment. In both jobs, “the machine passed with flying colours”, displaying high levels of productivity, efficiency and ease of maintenance.
“In coal, we crushed between 5 000 and 6 000 t in a 12-hour cycle. The machine punched well above its rated production capacity of up to 450 tph by producing 500 tph. Given that this is a diesel-electric unit, the machine is consuming about 50% less diesel per hour in this application than a competitor machine,” says Van Wyk.
With productivity in mind, the machine incorporates a pre-screen, a crusher and a post-screen, allowing for the production of different product sizes using a single machine. This three-in-one nature of the machine allowed Marodew Plant and Services to produce up to three different sizes of material in coal, eliminating the traditional need for two to three machines in such an application, thus reducing both capital and operational costs.
The pre-screen guarantees accurate fines removal, ensuring both increased productivity and reduced wear in the crushing chamber. The less fine material that reaches the crushing process, the higher the productivity and final grain quality. During coal processing, Marodew Plant and Services saw particularly an increase in final product quality through the discharge of coarser particles via the side discharge conveyor.
The post-screen processes two screened products and recirculates any oversize back into the crusher. The ability for it to be reconfigured quickly to produce one single-sized finished product, or two-sized finished products, depending on the operational demands, maximises the machine’s versatility.
When Quarrying Africa visited the chrome mine in December 2024, the machine had already crushed about 150 000 t of material, clocking some 450 hours in the process. Given the abrasive nature of chrome, the crusher is offering a 50% fuel saving compared to a same-sized competitor machine previously deployed in the same application.
Given that this machine is diesel-electric, it can also be plugged onto mains electricity. Where infrastructure is available, this provides for a significant reduction in both operational costs and carbon (CO₂) emissions.
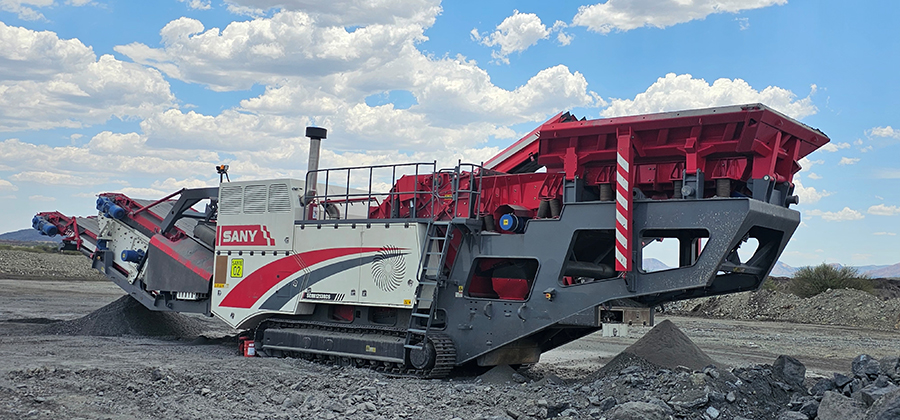
New capabilities
The addition of the SANY impact crusher to Marodew Plant and Services’ fleet has given the company new capabilities. Adding the SANY SCIM1213RC6, says Smith, now allows the company to tender for large-volume jobs from bigger mining companies.
“We can now service any high-production contracts from 40 000 to 150 000 tonnes per month (tpm) with a single machine, be it in coal, chrome or any other hard rock application. With our previous fleet, we could only undertake contracts up to 40 000 tpm in size. In essence, we have increased our crushing capacity by 200-300% by adding this machine to our stable,” says Smith.
The efficiency of the machine also allows the company to meet stringent fuel cap limits in contracting. According to Van Wyk, the acceptable standard in the industry is about R1,5 worth of fuel per tonne, and with the SANY machine, Marodew Plant and Services is well below that limit, achieving between 30 cents and 50 cents per tonne in terms of fuel consumption. In addition, being able to produce up to three material sizes using one machine means that the company further saves clients fuel and also helps them meet their sustainability goals.
Fewer maintenance requirements on the machine also translate into high uptime for Marodew Plant and Services, allowing the company to meet its contractual obligations, especially in high-production jobs. The machine is designed with ease of maintenance in mind. For example, it takes about 15 minutes to change the deck. It also comes with an on-board mini-crane for easy changing of blow bars.
“Reduced maintenance equals more production and reduced operational costs. To provide context, we have produced 150 000 t of chrome and 500 000 t of coal with one set of blow bars which, in our experience, is unheard of. The ease of maintenance and the reduced maintenance costs of this machine are ‘dream attributes’ for every contractor,” says Smith.
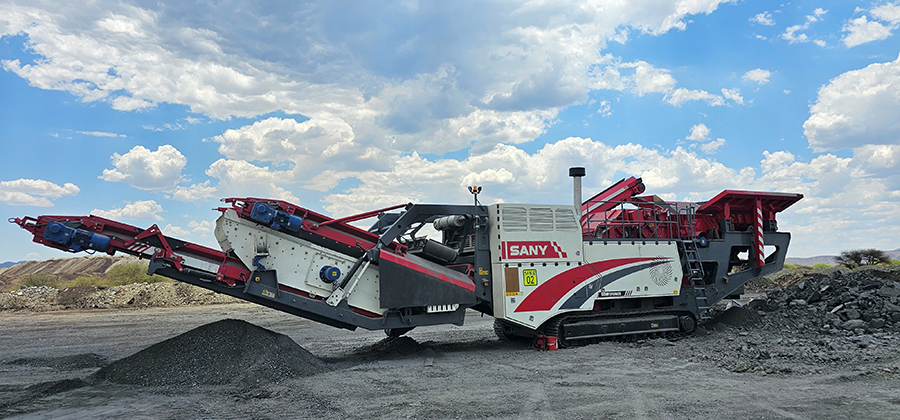
Support
Both Smith and Van Wyk have been impressed by the support from SANY Southern Africa. From the onset, says Smith, Thabo Lerumo, operations manager at SANY Southern Africa, was supportive of the young company. Despite the lack of a substantive track record, SANY was willing to “take a chance” on the Marodew Plant and Services and provided the machine on a rent-to-buy basis.
To ensure uninterrupted operations, SANY brought in a technician from China to support Marodew Plant and Services. During Quarrying Africa’s visit in December 2024, the technician, a knowledgeable individual who was part of the team that designed SANY crushers and screens, had been on site for six months which, according to Van Wyk, shows SANY’s commitment to the success of its customers.
Before opting for the SANY crusher, Marodew Plant and Services had already been impressed by SANY Southern Africa’s parts stockholding. The company recently commissioned a new parts distribution centre located in Olifantsfontein, Midrand. The new, bigger warehouse has enabled SANY to increase its spare parts inventory from approximately R170-million to R270-million.
As part of its strategy to further grow its aftermarket capacity, SANY has in recent time opened new branches in Middelburg, Rustenburg and Richards Bay, allowing it to provide faster service turnaround times to customers in these important mining regions.
“These investments are informed by our drive for customer satisfaction and to advance the reputation of the brand in southern Africa, which is important for us. The huge capital investments also exhibit our long-term commitment to the local market and our customers,” says Lerumo. “We are happy that the first SANY crusher has performed beyond expectations. Based on this performance, we have received three orders, which will be delivered in 2025.”
Van Wyk has also been impressed by the quick turnaround in terms of parts. SANY maintains an impressive 99% parts availability in its parts warehouse. If, for any reason, something is not in stock, the company resorts to air freight to ensure minimal impact on customer operations.
“In a recent incident, we had a problem with the generator of our machine and SANY flew in a new generator from China, which took only a week to arrive. For us, this shows true commitment by the original equipment manufacturer. In future, we are looking at standardising our mobile crushing fleet with SANY machines,” concludes Van Wyk.