Building a new processing plant can be an expensive endeavour. Therefore, quarrying operations are turning to modular plant systems for their array of advantages, essentially the low capital costs that are reflected in a higher return on investment and improved cost to recovery ratios.
Additionally, modular systems offer quick lead times because they comprise quick and easily available modules that can be on site and operational within a short space of time. Original equipment manufacturers can build these self-contained, high recovery plants for minimal start-up capital, using high-quality components and in-house expertise.
“We have observed that customers are increasingly looking for faster and more cost-effective solutions compared to conventional, bespoke structures. Modular plants by their nature require a smaller site footprint with minimal civil works, which gives the customer the option to have the equipment relocated to a new location at a later stage. Time, available real estate and moveability are some of the key factors behind their uptake, especially for expansion projects or extending the life of mine,” says Isaacs.
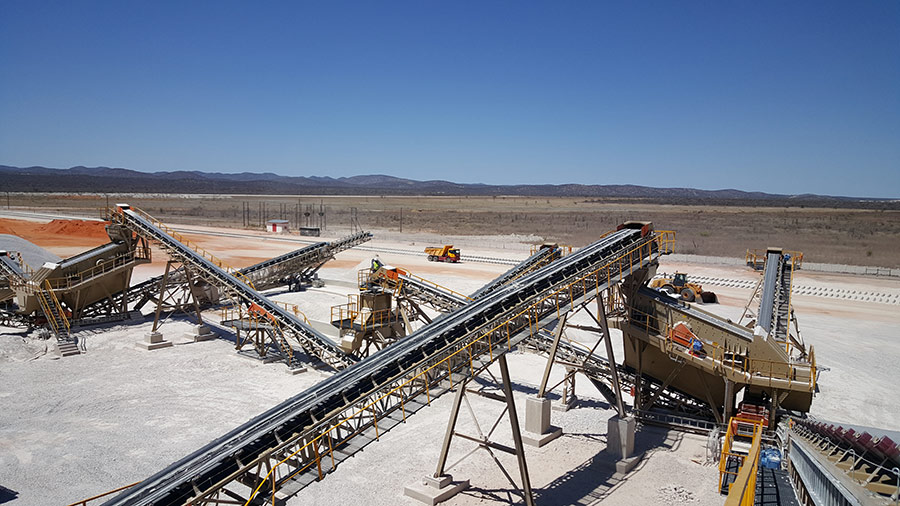
Key benefits
The short timeframe for manufacture and erection on site is a big benefit for customers. In addition, modular plants allow for ease of plant extensions. Subject to the lifespan of the operation, the modular concept also allows for decommissioning and reinstating on alternative sites.
“Astec modular solutions are meticulously designed for easy erection and transportation, which allows them to be broken down to fit into standard shipping containers if needed. It is a compact but sturdy, heavy-duty design built to last and provides easy access for maintenance,” he says.
Astec’s excavator feed hopper modular jaw plant requires no retaining wall. However, the company’s truck dumping hopper will require one. The company also offers skid-type structures complete with walkways, handrails, access ladders, guards and all fasteners.
“Our modular structures are erected at many southern African quarrying and mining sites. One of our flagship projects is the recent supply of a 400 tonnes per hour (tph) primary modular jaw system to a top quarry in Cape Town,” he says.
The structure was easy to assemble and was erected in a matter of days with a mobile crane and only a single technician and an assistant. The client is now able to shut down and dismantle the old plant and access saleable rock beneath the old plant. At the time of ordering, the quarry opted for a larger jaw crusher to increase its primary plant capacity.
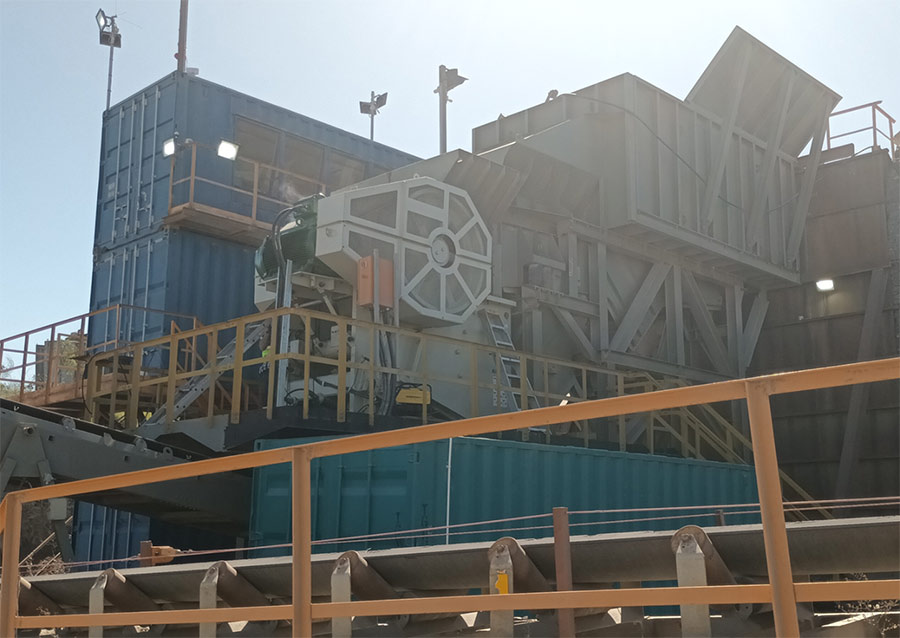
Key considerations
While quarries are generally pressed for time and cost, Isaacs cautions that there is need for due diligence and careful consideration of the manufacturer, safety, quality and durability and not always the cheapest solution when it is buying time.
However, Isaacs believes that the modular growth will always be driven by cost, efficiency and safety. This, he believes, is going to be a growing opportunity in both the mining and aggregates spaces. Astec is an industry leader and has over the 100 years of its existence demonstrated its capability of manufacturing world-class products and of being compliant to standards in the mining and quarrying sector.
“At Astec Industries South Africa (previously Osborn), we are a triple ISO certified manufacturer. Our modular solutions are in operation worldwide and we can supply complete plants with various feed or surge hopper sizes up to 50 t live capacity, as well as inter-connecting and product conveyors for primary, secondary and tertiary applications. The standard sizes we offer range from 150 tph to 800 tph, however, we customise as per customer requirements,” concludes Isaacs.