Excavators are some of the most critical heavy equipment used in quarries. Given that they come in different shapes and sizes, with a wide range of options available, picking the right machine for the project requirements at hand can be a daunting task. It is therefore important for quarry managers to understand the factors that should inform their decision-making process.
Safety, efficiency, bucket size, size, and weight, reach and digging depth, total cost of ownership (TCO), resale value, warranty, and financing options are some of the key factors to consider when making that buying decision.
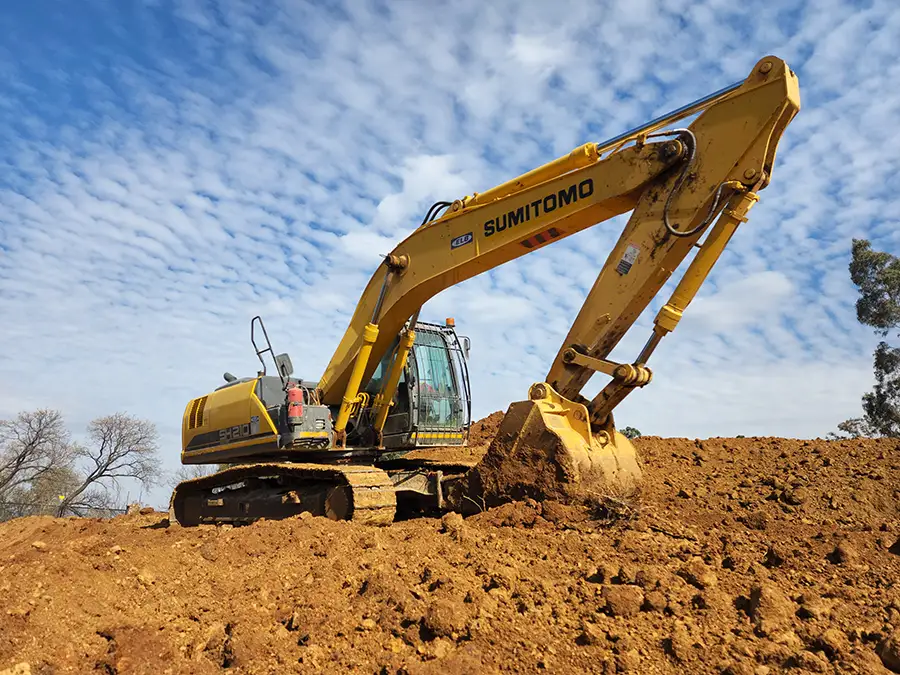
Match factor
Keon Kardolus, divisional manager for Earthmoving and Construction at ELB Equipment, the official distributor of Sumitomo excavators in South Africa, says it is incredibly important for quarry owners to ensure they are buying a machine that is best matched to the application at hand.
Matching the right excavator to the specific quarrying tasks can significantly enhance efficiency and productivity. Quarry owners, says Kardolus, need equipment that can handle the demands of their operations effectively, whether it is digging, loading, hauling or crushing. The wrong machine may struggle or underperform, leading to costly delays and decreased output.
“Investing in the right equipment from the outset can lead to substantial cost savings in the long run. A machine that is optimised for the application will likely have lower operating costs, reduced maintenance requirements, and a longer lifespan. This translates into better return on investment (ROI) for quarry owners,” says Kardolus.
Stephen McNeill, head of Marketing and Sales Support at Bell Equipment, the approved distributor of Kobelco and JCB excavators, says one of the key factors that affects the overall efficiency of the excavator is ensuring the correct bucket is fitted to the excavator. A bucket that is not correctly matched to the material density and the lifting capacity of the machine will slow cycle times and decrease machine stability.
The excavator size needs to match the requirement of the application whether its loading trucks or a hopper. For example, if an excavator is deployed to load a dump truck, the bucket needs to have the capacity to load the dump truck in five to seven passes in order to optimise the efficiency of the equipment.
Gary Martin, senior market professional for heavy construction and quarry industries, Caterpillar, says to operate at the lowest cost per tonne, it is essential that quarry managers do their homework to select the correctly sized machine.
“Let’s start with face loading – there is a need to establish the tonnage that represents the output of the crusher at 100% efficiency, assuming in this case there is only one crusher. Then, select the trucks to match the crusher maximum production output. As first indicators to match production, look at the excavator weight and bucket size,” says Martin.
It is all about the calculation, stresses Martin. Take for example, a crusher with a feed rate of 500 tonnes per hour (tph) serviced by two Cat 770G trucks with a payload of 38 t each. The 770G trucks carry the material from the face to the crusher before returning for another payload. To complete one cycle of load-haul-dump-return takes a truck some eight minutes or 285 tph (2 x Cat 770G trucks = 570 tph).
“Now that the required production rate is known, the excavator can be sized for performance and optimum efficiency. The industry benchmark is to load the truck in six to seven buckets. Taking the maximum 38-t truck capacity, then dividing it by six or seven buckets, means that the excavator should hold five to six tonnes per bucket. Divide the tonnes by the material density and you have the bucket volume,” he says.
For example, 5,5 t divided by material density of 1,6 is equal to a bucket with a volume size of 3,45 m³, which indicates that the Cat 352 excavator is the right match. Another easy rule of thumb to calculate the correct size Cat excavator to match the production is by using the last two digits of the model number – in the case of the Cat 352, 52 x 10 represents the approximate tonnage that can be safely loaded per hour. This works for the Cat excavators, from the Cat 320 to the 395.
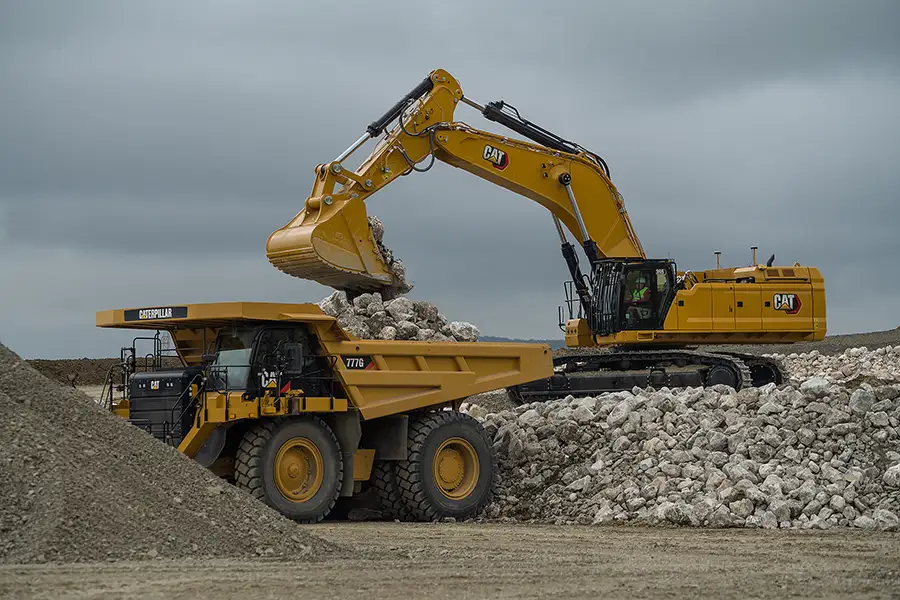
Correct choice
Kardolus adds that the choice of the right excavator for the right application plays a crucial role in ensuring a safe working environment – a concern which is paramount in any industrial setting. Using an excavator that is appropriately sized and equipped for the task can help minimise accidents and injuries, safeguarding both the workers and the investment.
“Providing operators with the right equipment not only enhances their comfort but also their productivity. A machine that is well-matched to the job reduces operator fatigue and allows for more precise and efficient work, ultimately leading to higher output,” says Kardolus.
Given that quarrying needs can change over time, having the flexibility to adapt to evolving requirements is essential. Purchasing a machine that can be easily configured or equipped with attachments to handle various tasks ensures long-term utility and versatility.
Reputation and customer satisfaction are also outcomes of good purchasing practices. Successful quarry operations, says Kardolus, often rely on their reputation and customer satisfaction. Using the right equipment ensures that jobs are completed efficiently and on time, which can lead to satisfied customers and positive word-of-mouth referrals.
“In summary, for quarry owners in South Africa or anywhere else, selecting the right equipment that matches the specific quarrying application is of great importance. It directly impacts efficiency, safety, costs, and overall operational success. As the official distributor for Sumitomo excavators in South Africa, we play a vital role in helping quarry owners make informed choices to achieve these benefits and drive the success of their businesses,” says Kardolus.
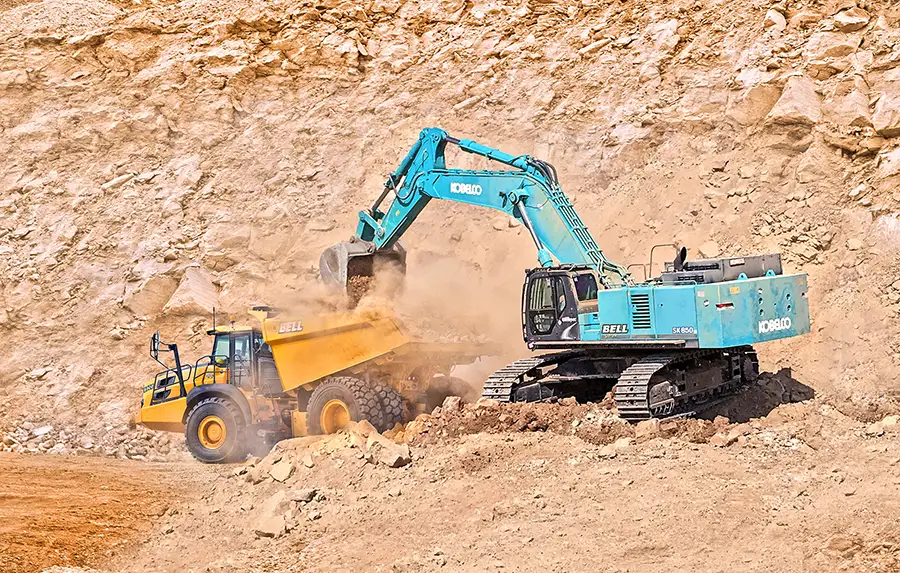
Factors to consider
Commenting on some key factors to consider when choosing an excavator for a quarry operation, Caterpillar’s Martin says the configuration of an excavator plays a major part in its production output. There are two different offerings from Caterpillar and other suppliers configured for different environments. The reach excavator version comes with a longer boom, a longer stick and a smaller bucket which is designed to give more reach in applications. It also normally comes with a slightly different undercarriage with wider triple grouser track pads to improve flotation in moderate applications.
“When selecting an excavator, it is not just about the machine weight and size but also about the machine configuration. For pure production loading, the same machine will have a shorter boom, a slightly shorter stick, with a much bigger bucket,” explains Martin. “For harsh and demanding quarry and mine environments, a heavy-duty undercarriage with double grouser track pads is recommended. It is not all about the size and horsepower. For example, a 50-t excavator with a 2 m³ bucket will provide the same output as a 30-t excavator but with higher running costs, impacting the cost per tonne and therefore profit margins.”
Cat dealers, he adds, have considerable experience and expertise and can advise quarry managers on the right equipment to achieve their production targets within their unique operating conditions.
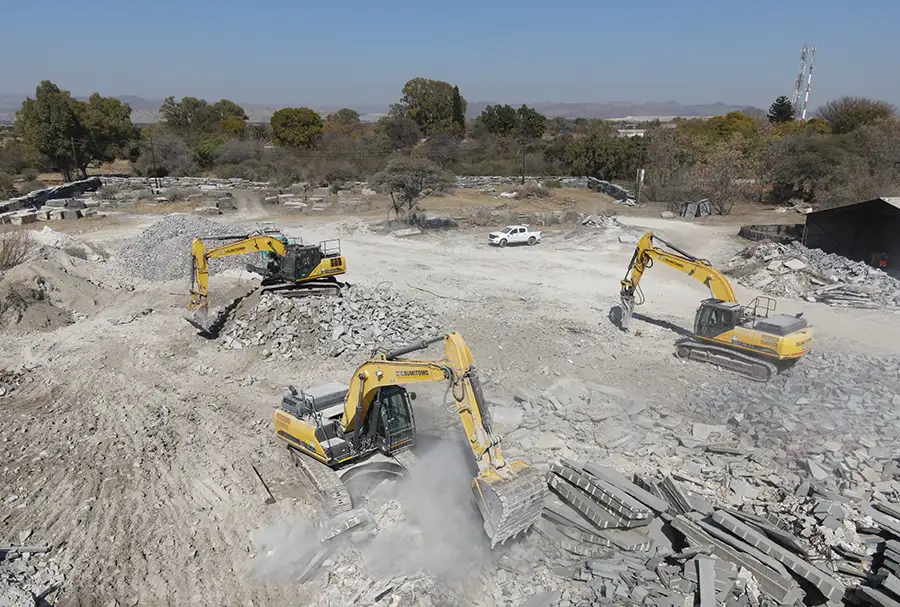
More considerations
For McNeill, one of the key considerations should be choosing an excavator design that has a proven reputation in the market for being able to handle the application/s that it is intended for. It should also provide quarry operators with low overall running costs – from fuel through to maintenance costs – that are within the quarry’s operational budget.
“Fuel economy is application-specific, but it is probably the largest cost in terms of cost per tonne. Kobelco has a huge fuel efficiency focus without losing focus on productivity. There is no compromise when it comes to productivity,” says McNeill.
Support from the local dealer, he adds, is another crucial consideration because every machine, especially those working in harsh applications, will require some technical backup at some point and it is important that a service provider is quick to respond and has the necessary expertise and parts availability to avoid costly downtime. In this respect, says McNeill, Bell Equipment South Africa has a large footprint of customer service centres, each with trained technicians and a well-stocked parts department.
“The excavator should also have the ability to provide you with the telematics data that you require to be able to track machine hours, fault codes, and productivity for the relevant application. The Kobelco range of excavators, sold and supported by Bell Equipment South Africa, can be integrated with the Bell Fleetm@tic® fleet monitoring system to enable fleet owners to monitor their whole fleet with one, user-friendly telematics system,” adds McNeill.
Additional factors to consider are operator comfort and safety. Any machine under 50 t should have a ROPS FOPS-certified cab and machines over 50 t should have a FOPS-certified cab guarding to protect the operator against rock falls. In terms of comfort, operator comfort reduces operator fatigue, which positively influences productivity.
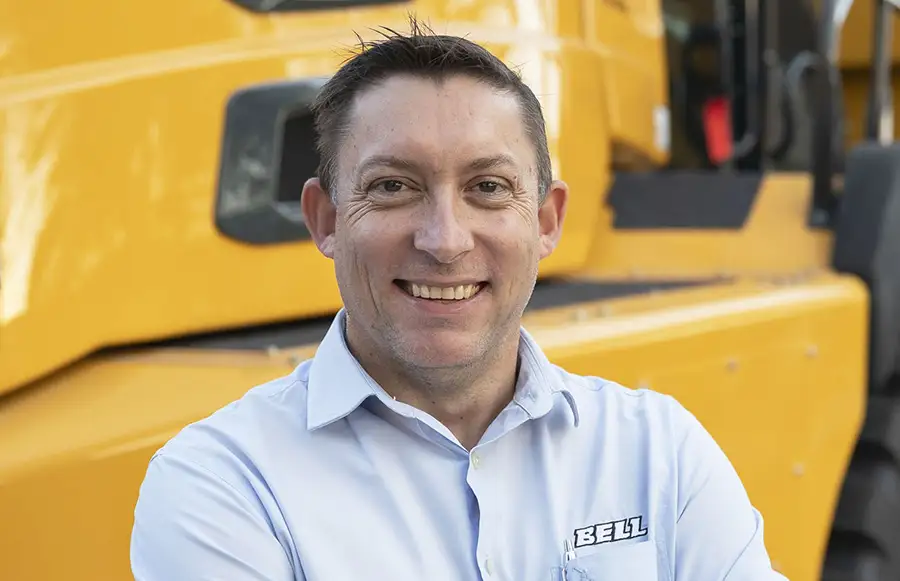
“The key to operator comfort is operator-friendly controls, and the Kobelco range has a comfortable and spacious cab with excellent visibility, a powerful automatic air-conditioner, easy-to-understand displays, and smooth controls. The travel pedal is also larger for greater operator comfort. The wide access cab allows for smooth entry and exit. A quieter working environment is achieved through strategic component positioning and the superior sealing of the cab, while the rigid cab construction and liquid-filled viscous cab-mounts minimise cab vibration for fatigue-free operation,” explains McNeill.
Attachments have also become key to enhancing an excavator’s versatility. According to McNeill, most hydraulic-operated attachments can now be fitted to Kobelco excavators without any need for modifications to the machines as they are factory-fitted with two-way piping which has foot-operated controls.
Hydraulic flow can also be adjusted from inside the cab at the flick of a button. This alleviates the need for flow gauges and making mechanical adjustments on the pump itself. This is now a standard on all Kobelco machines up to and including the 50-t SK520. Kobelco machines also allow for the switching between single and bi-directional hydraulic flow within the cab.
Electronics significantly affect the versatility of the machine in terms of switching between different functions and from a diagnostics point of view. The Kobelco range uses an Intelligent Total Control System (ITCS) – an electronic system that responds quickly to sudden changes in hydraulic load to ensure that the engine runs as efficiently as possible with the minimum of wasted output.
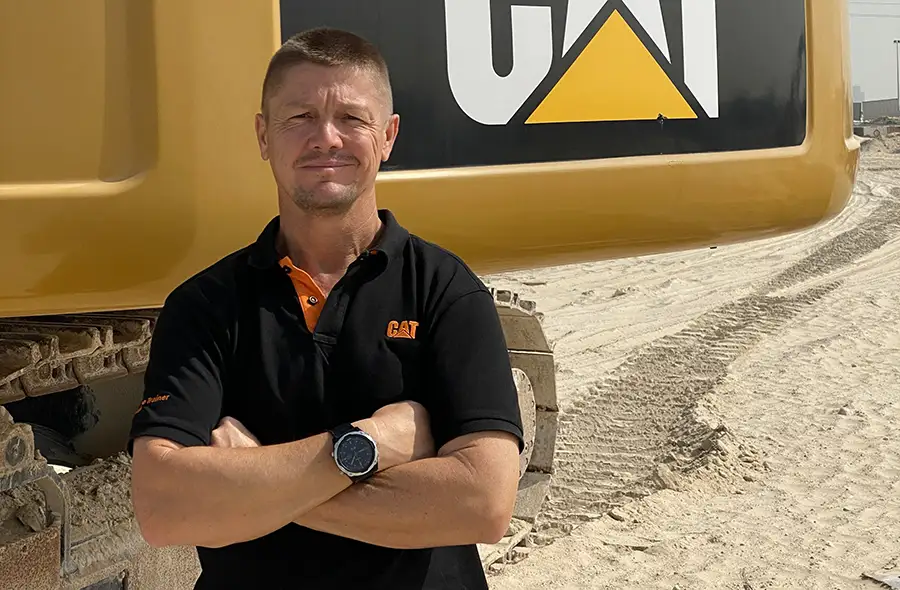
Essential factors
For Kardolus, when buying an excavator for quarrying purposes, several key factors should be carefully considered to ensure one makes the right choice. Here are some of the essential factors to keep in mind, with a focus on Sumitomo excavators:
Excavator size and capacity: Consider the size of the excavator needed based on the scale of your quarry operations and the types of materials you will be handling. Smaller excavators are suitable for lighter tasks, while larger ones are needed for heavy-duty operations.
Bucket size and attachments: Ensure that the excavator can accommodate the appropriate bucket size and attachments for the specific tasks in your quarry. Different buckets and attachments are designed for various tasks like digging, grading or lifting.
Engine power and fuel efficiency: Evaluate the engine power to ensure it provides sufficient horsepower for your quarrying needs. Also, check for fuel efficiency to reduce operating costs over time.
Hydraulic system: Assess the excavator’s hydraulic system for its speed, precision and durability. A well-designed hydraulic system can significantly impact the machine’s performance and efficiency.
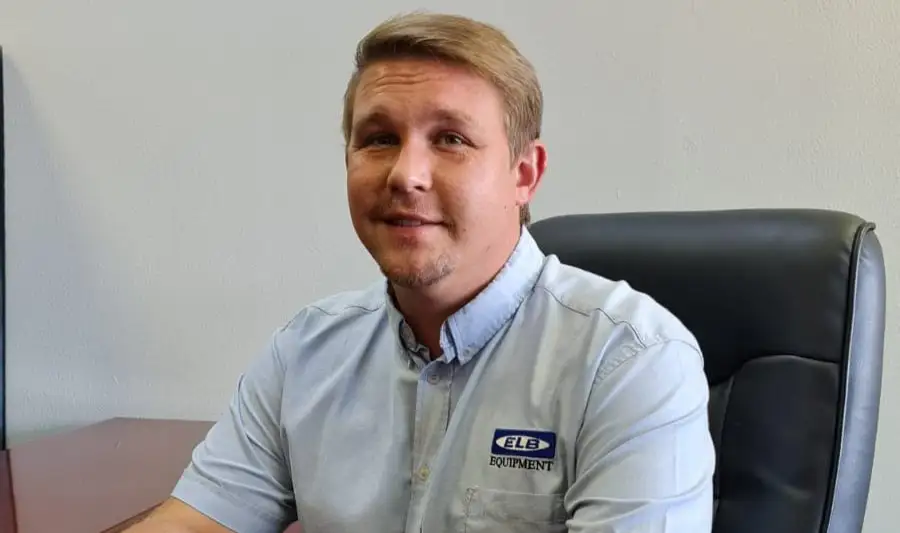
Reach and digging depth: Consider the maximum reach and digging depth of the excavator to ensure it can access the areas you need to work in your quarry.
Operating weight and stability: Ensure that the excavator’s weight and stability are suitable for your quarry’s terrain and conditions. Stability is crucial for safe and efficient operation.
Cab comfort and operator features: A comfortable and well-equipped operator’s cabin can improve productivity and reduce operator fatigue. Look for features such as ergonomic controls, air conditioning, and visibility.
Maintenance and serviceability: Check the ease of maintenance and access to key components. Easy maintenance can minimise downtime and reduce operating costs.
Brand reputation and dealer support: Consider the reputation of the manufacturer and the availability of dealer support and spare parts in your region. A reliable support network can be crucial for ongoing maintenance and repairs.
Warranty and financing options: Review the warranty offered by the manufacturer and explore financing options to fit your budget. A good warranty can provide peace of mind and potentially save on repair costs.
Environmental compliance: Ensure the excavator meets environmental regulations and emissions standards applicable in your area. Compliance can be essential for legal and environmental reasons.
Safety features: Look for safety features such as backup cameras, proximity sensors and rollover protection systems (ROPS) to enhance the safety of your quarrying operations.
Resale value: Consider the potential resale value of the excavator, as this can impact your long-term investment.
TCO: Calculate the total cost of ownership, which includes initial purchase price, maintenance costs, fuel consumption and resale value. This will help you make a more informed decision.
Operator training: Ensure that your operators are trained and certified to operate the specific excavator model safely and efficiently.
Demonstration and evaluation: Whenever feasible, schedule a demonstration of the excavator to gauge its real-world performance in quarry conditions. According to Kardolus, this is just one of the additional advantages one can expect when partnering with ELB Equipment to fulfil their equipment requirements.
“By carefully evaluating these factors and their relevance to their quarrying operations, quarry owners can make informed decisions when purchasing a Sumitomo excavator or any other brand that suits their needs,” concludes Kardolus.