Whatever type of material is being processed, a production plant’s conveyor belt network forms part of the critical artery that moves material through the system from run-of-quarry to saleable end product. According to Van der Berg, it is no overstatement to say that regular conveyor maintenance is absolutely crucial to productivity and profitability. A proactive approach to conveyor maintenance, she adds, also plays a vital role in safety, the longevity of the plant and its components, cost control and energy efficiency.
“Keeping belts running efficiently demands that they are well maintained to ensure they remain free from carry-back, spillage and build-up, which would otherwise cause excess wear and unscheduled downtime. Regular inspection and maintenance are proven to ensure that everything is running as it should, and that components such as belt cleaners are performing at their optimum,” she says.
Van der Berg points out that the benefits of regular conveyor maintenance extend far beyond plant productivity, especially as far as the health and safety of workers is concerned. Conveyors are one of the places where the most accidents occur, and, having conveyor components such as belt scrapers well maintained, does lower health and safety risks.
In Van der Berg’s experience, however, the benefits of well maintained belts and belt scrapers are rarely understood or prioritised by busy plant maintenance teams, unless they have a specially trained resident expert in conveyors.
“That is where a scheme such as Martin Engineering’s Walk the Belt™ programme comes in,” she says. “During inspections, our highly trained technicians will see things that are often overlooked by in-house teams. Our team gets to the root causes and provides a detailed report with solutions and recommendations on the entire conveyor system.”
Apart from improving productivity, Martin’s unique Foundations™ learning programme is a great way to develop workers so they can understand the benefits of regular maintenance and identify the most common problems.
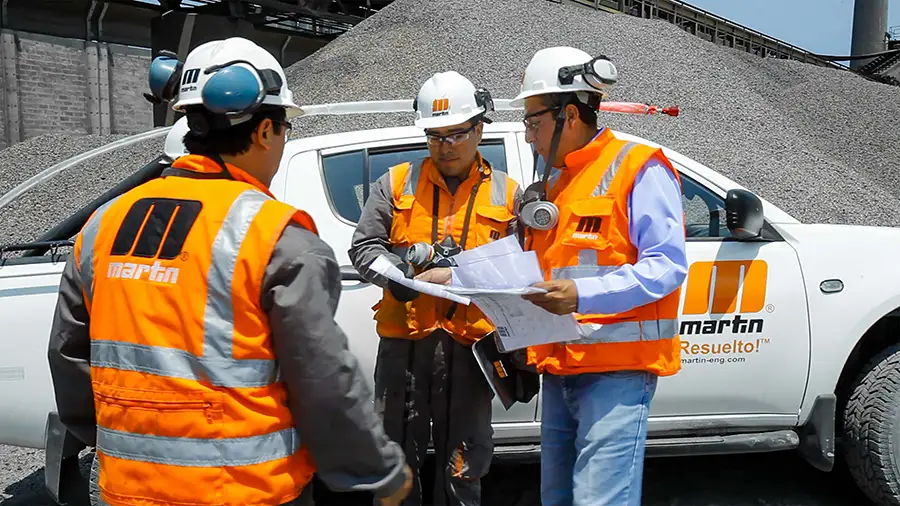
Common problems
Commenting on some of the common conveyor maintenance issues to look out for, Van der Berg says some of the issues encountered on a regular basis include material carryback and spillage, structure damage due to belt mistracking or causing mistracking, belts and pulleys engulfed in spillage, seized rollers, missing belt scrapers and other components, belt sag or damage to the conveyor in the loading zones due to inefficient support, airborne dust, flow obstructions in chutes and hoppers, as well as component wear, damage or failure.
“These are sometimes caused by poorly designed systems and mismatched components, but usually result from a lack of regular inspection and maintenance that can help to keep on top of these kinds of issues,” she says. “In terms of the frequency and interval of maintenance, that really depends on the capacity, design and condition of the plant, the components being maintained, and the types of materials being processed, amongst other things.”
The downside, she adds, is that many companies still rely on reactive maintenance on their conveyors – they simply fix when it breaks. This approach means that components are left to run until they fail, and the resulting downtime is unscheduled, disruptive and almost always expensive. Among the contributors to the costs of this approach are unplanned stoppages, ancillary damage (when a broken component damages something else), personnel overtime and emergency service fees.
“Worse still, technicians tend to take more risks and make more mistakes when under pressure to restore operations in the shortest possible times. Despite the clear downsides of reactive maintenance, we estimate that over half of all conveyor maintenance programmes still follow this approach,” states Van der Berg.
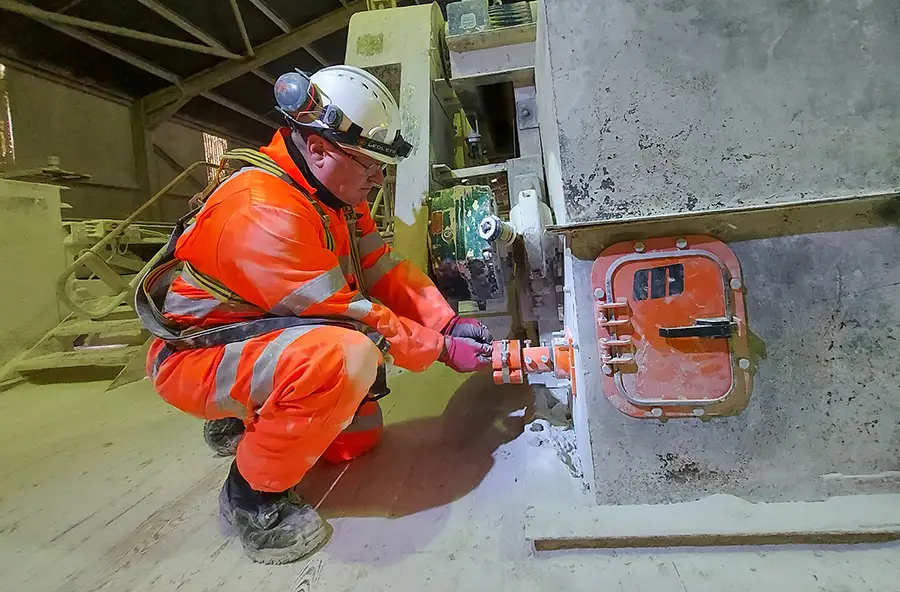
Basics of conveyor maintenance
Fundamentally, says Van der Berg, every production plant needs a comprehensive maintenance plan, not just to address the basics but with goals to minimise unscheduled downtime, improve health and safety, increase efficiency and reduce costs to achieve a better overall return on investment (ROI).
“This naturally leads to regular inspection and servicing schedule as an integral part of a preventive maintenance regime. The idea of preventive maintenance – performing regular maintenance to reduce the chances of failure – is nothing new but it is still not commonplace despite the obvious advantages,” she says.
Bulk handling equipment endures continual punishment while transporting millions of tonnes of raw materials, and preventive maintenance prolongs component life, increases productivity, improves efficiency and reduces maintenance costs.
Some firms, she says, take this responsibility in-house, but others find that specialist service providers deliver a better return on their maintenance investment, bringing in external experts for specific inspection or maintenance tasks so employees can focus on core activities.
“A preventive maintenance approach to conveyor maintenance assumes that each component has a typical functional life span. Using observation and experience, preventive maintenance determines when relevant parts should be retired, replaced or refurbished, before the expected failure point. The result is generally greater safety, higher system efficiency, reduced spillage and better overall system control,” says Van der Berg.
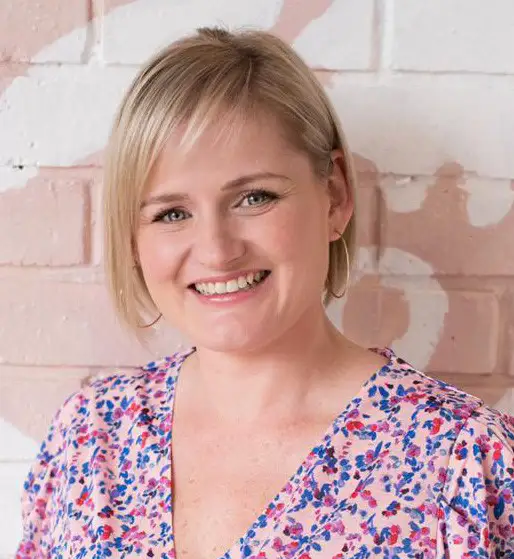
Maintenance solutions
Martin Engineering has long been a pioneer of technologies that help producers assist with conveyor maintenance, reducing the need for manual intervention, minimising the interaction of people and machinery while maximising plant uptime.
The most notable examples include the company’s N2® Remote Monitoring System, which allows for predictive maintenance by ensuring belt scrapers are monitored on a real-time basis and visible to customers on their mobile devices or desktop computers. Before N2, the only way for maintenance teams to identify what service was needed on belt scrapers was to physically go to each head pulley, taking all the necessary steps to address the hazards involved in the inspection.
However, with N2, technicians only need to visit conveyors when their system shows that a belt scraper needs attention. It is the ideal solution, especially for large-scale plants which have numerous difficult-to-access belt conveyors distributed over a large area.
“In addition, our revolutionary CleanScrape® belt scraper provides unmatched cleaning performance and is guaranteed to last longer than any conventional cleaners. Featuring a series of hard-wearing tungsten carbide tips tensioned at an angle across the discharge pulley, CleanScrape provides unparalleled cleaning at the lowest operating cost, with the greatest ROI over the life of the cleaner, while significantly reducing the frequency of maintenance. We have proven success, especially on critical conveyors with the CleanScrape belt scraper,” concludes Van der Berg.