On the back of increased demand, a Mali-based limestone producer recently took the decision to expand its production capacity. Having run an existing Sandvik fixed plant for years, the company was already aware of the Sandvik quality and aftermarket support excellence, hence the decision to opt for another plant from the same original equipment manufacturer (OEM).
Given the urgent nature with which the company wanted to expand its capacity, the FastPlant concept from Sandvik Rock Processing Solutions was the ultimate solution to inject the much-needed extra capacity within a short period of time. Hubert Kwesi Essel, sales engineer – Sandvik Rock Processing Solutions, tells Quarrying Africa that the FastPlant fit the bill for the client, mainly because of the fast lead time, allowing the operation to expand production sooner.
“The client opted for a two-stage FastPlant, which is a range of pre-defined crushing and screening modules made for the most common quarrying and mining applications. The FastPlant concept therefore ensured a fast delivery time and installation,” says Essel.
Delivery of a FastPlant, states Essel, generally takes about 10-12 weeks, as opposed to double or even thrice the timeline of a bespoke plant. This particular plant, however, took about 20 weeks due to shipping and logistical delays from Europe to Mali. Commissioned in April 2023, the plant is producing beyond customer expectations, managing between 200 and 250 tph.
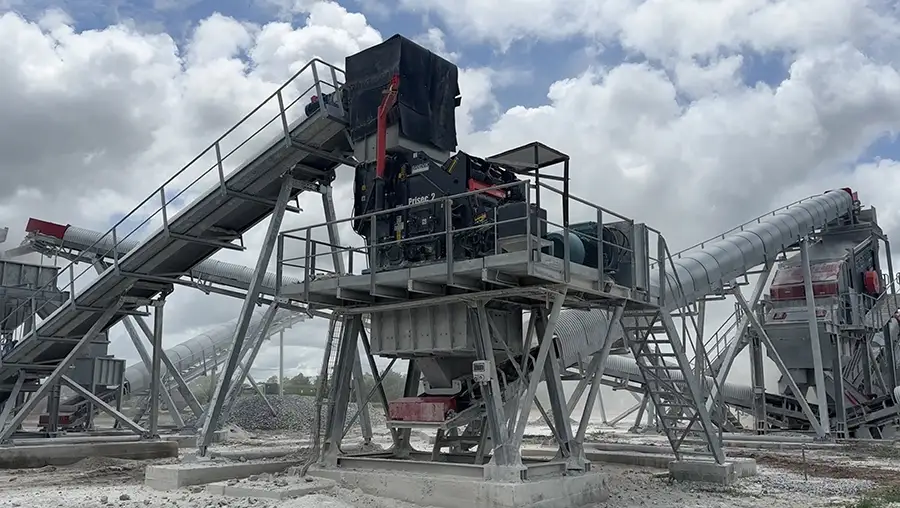
Plant in detail
The plant comprises a full suite of Sandvik equipment, including a grizzly feeder, a jaw crusher, a horizontal shaft impactor (HIS) and a four-deck screen.
With a 100 mm setting, the Sandvik ST1263H vibrating grizzly feeder takes run-of-mine material of up to 700 mm. The ST1263H ensures efficient scalping and fines removal, thus significantly improving the total throughput of the primary station by its ability to keep the crusher fully fed even during varying feed conditions.
From the grizzly feeder, material goes into the Sandvik CJ411 primary single-toggle jaw crusher with a close side setting (CSS) of 100 mm. The CJ411 was chosen for its high capacity. The crusher’s deep symmetrical crushing chamber and optimised nip angle maximises size reduction and production capacity.
“The Sandvik CJ411 benefits from high capacity as well as high reduction rates. It is also designed to be stable, durable and benefits from low jaw-plate wear, which minimises the need for maintenance and downtime,” explains Essel.
From the jaw, material goes into a surge bin, which in turn feeds the Sandvik CI722 HSI secondary crusher with a 25 mm CSS. The CI722 is said to be the perfect secondary crusher for non-abrasive material such as limestone. The working principle of the Sandvik CI722 HSI encourages material to break along its natural cleavage planes, and it produces stress-free, cubical-shaped products.
From the HSI, material is directed into a four-deck Sandvik SA2164 screen, with a 25 mm top deck and a 19 mm bottom deck. The other two decks are 13 mm and 5 mm respectively.
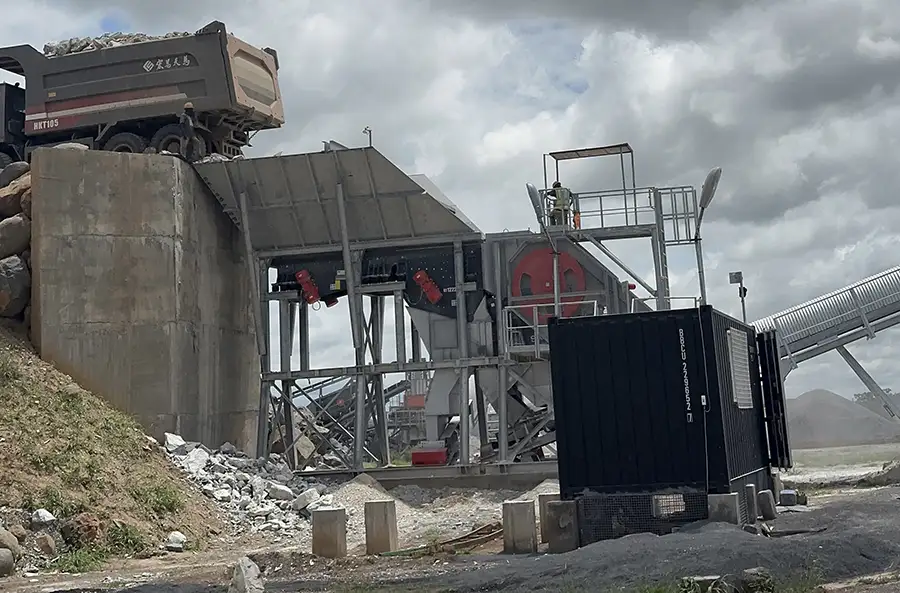
Why FastPlant?
As the name suggests, one of the key features of the FastPlant that appealed to this particular customer was the fast delivery times. The FastPlant benefits from pre-designed layouts and flowsheets, which significantly reduce delivery lead times, especially for fast-tracked projects, says Praveen Kumar VG, Sales Support – Global Plant Solutions at Sandvik Rock Processing Solutions.
In addition, the flexible nature of the plant allows for customers to chop and change in line with their changing production requirements. “If production requirements change in future, customers can just add a couple of modules to increase production or take out a few modules to reduce capacity in line with market requirements,” explains Kumar VG.
Another major feature of the FastPlant is its minimum footprint, which bodes well for space-constrained sites. In addition, the required civil works are very minimal, translating into major cost benefits for the client. The minimal civil works, coupled with the modularity of the plant, means that it can be moved from one site to the other with ease.
According to Essel, safety was a major consideration in the client’s buying decision. The client was strict about access and the FastPlant addressed the concerns through spacious walkways, as well as ample space in the chute areas for ease of maintenance. In addition, there is an option to fully automate the plant, thus taking people out of harm’s way.
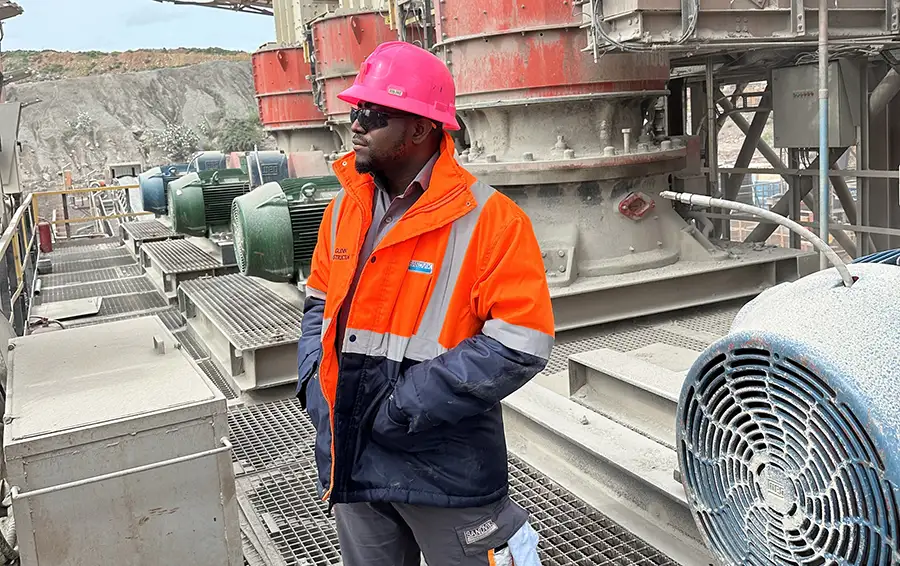
Support matters
Given the high-production nature of the operation, downtime for this limestone producer is out of the question. Key to its buying decision was the support capabilities of the OEM. Customers in West Africa benefit from Sandvik’s expanded support footprint across the region.
According to Essel, the company has a strong support structure in Mali and the West African region at large. “Over the years, we have invested in massive infrastructure to support customers in this important mining region. In Mali, for example, we have our own entity and a large parts warehouse that supports Mali and other neighbouring countries such as Guinea, Niger and Senegal. This is complemented by a vendor management team that provides sound backup support on various customer sites,” says Essel.
Apart from Mali, Sandvik has invested in its regional headquarters in Ghana, which boasts a large parts warehouse and a vendor management team stationed at various customer sites. This is complemented by entities and parts warehouses in Nigeria and Burkina Faso, which cater for these countries and neighbouring markets.
Growth prospects
Due to its proven benefits, the FastPlant concept is gaining popularity in the global market. To provide context, the Indian market alone accounts for about 30 to 40 Sandvik plants per year, and 80% of these are a FastPlant, confirms Kumar VG.
Looking ahead, Kumar VG believes there is massive scope for growth for the FastPlant concept in Africa, especially given the sheer scale of mining and quarrying projects on the continent. “We see massive growth prospects for our FastPlant concept across the African continent, both in mainstream mining and aggregates markets,” concludes Kumar VG.