Given its impact on all quarry activities, blasting should be given the full attention it deserves in the process development of any quarry. Drilling and blasting influences nearly every aspect of the downstream operations, from load and haul though to crushing and screening. Poor drill and blast, therefore, leads to poor mine results and expensive operations.
This was the overreaching takeaway from Quarrying Africa’s recent visit to Gauteng-based Eikenhof Quarry, where a blast optimisation programme has changed the fortunes of an operation that has traditionally battled to get optimal blast results due to the challenging geological conditions on site.
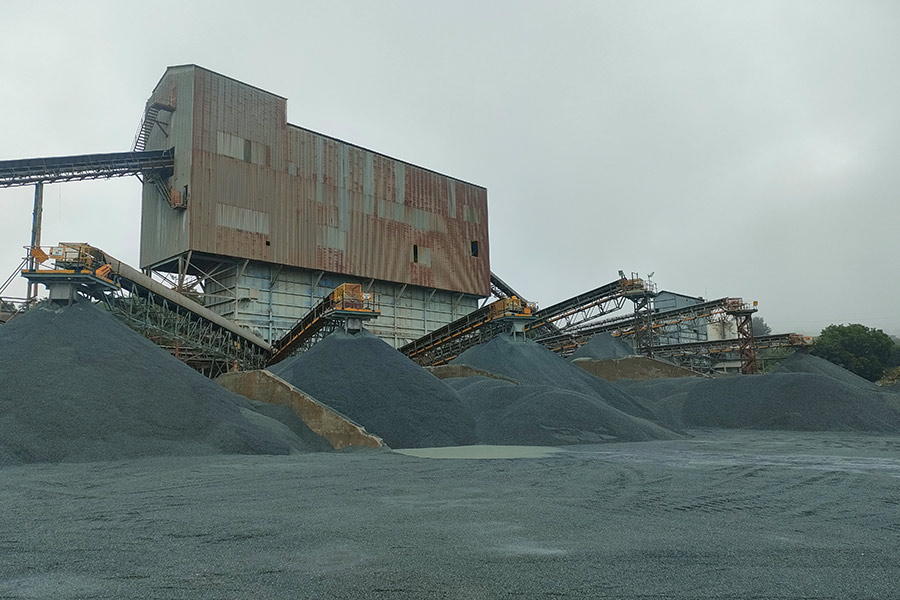
Problem statement
The andersite found at AfriSam’s Eikenhof Quarry is known to be one of the hardest and most abrasive rocks in the world. It is extremely hard, with a uniaxial compressive strength (UCS) of more than 500 MPa and Young’s Modulus of about 100, making it very difficult to blast and process. Its density is between 2,85 and 2,92. It therefore requires more explosive energy than granite, for example, to create fresh cracks in the intact rock between joint planes.
Works manager Yedwa Christopher Mgxekwa tells Quarrying Africa that although the andersite at Eikenhof is unusually strong, with a high UCS and high elastic modulus, it also contains joint planes that get damaged easily by creating voids on the back and side walls of the blast faces, creating large boulders and limited fines in each blast.
During blasts, the rock breaks preferentially along joints and planes and, therefore, joints would have a greater influence on fragmentation because of the huge difference between the joint strength and the rock strength. Consequently, the energy needed during blasting along joint planes is much lower than the energy required to create fresh cracks in the rock mass.
The rock structure at Eikenhof is quite variable across the pit, with some areas being moderately jointed and others being blockier to massive. In some places, shallow dipping joint planes exist. This complexity in structure led to inconsistent blast results. For example, on the higher benches of the western end of the pit, poor fragmentation has always been experienced in relatively blocky ground, whereas there have been fewer boulders on the lower benches on the south edge of the pit.
The impact of the rock structure is exacerbated by extensive back damage caused by blasting. The damage causes joint planes to open, thus generating a loose matrix of boulders on the free face of each blast, with very little fines.
“The rock structure at Eikenhof has always been challenging when it comes to blasting. The proportion of big boulders was always between 18% and 22% in each blast, which called for either secondary blasting or mechanical breaking using a hammer,” explains Mgxekwa.
Secondary blasting, he adds, is the most expensive type of blasting. To provide context, it is believed that mechanical breaking of oversize material is four times the cost of the original blast. Secondary blasting also creates excessive noise, and given the quarry’s proximity to communities, with Southfork just about 1 600 m and Eagles Nest just under 1 100 m away, this created unwanted community issues.
“The issue of boulders not only created a cost issue, but also presented safety challenges and downtime issues at our primary crusher. Having oversized rock in our run of quarry material resulted in incessant blockages at the primary plant. This resulted in safety issues related to the unblocking of the crusher. In addition, the process of unblocking the primary crusher would always cost us between two to three hours of production, depending on the type of blockage,” says Mgxekwa.
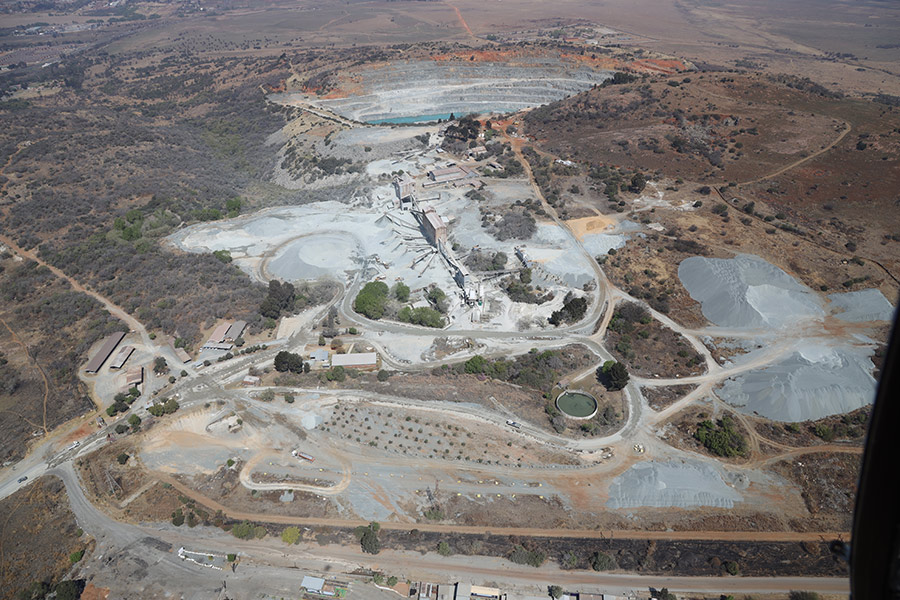
Blast optimisation
To get the better of these issues, the AfriSam Eikenhof team embarked on a blast optimisation programme in May 2021, which was led by well-known blasting consultant, Tony Rorke. During a site visit, Rorke got a better understanding of the rock properties and made several recommendations based on his findings.
“The objective of the blast optimisation programme was to reduce the proportion of boulders in each blast and to find ways to increase the percentage of fines in the fragmented rock,” explains Mgxekwa. “In order to achieve this, we implemented a range of changes to our blast parameters.”
The main aim was to limit the extent of damage on the back walls, which created a lot of boulders. To achieve this, confinement on the back line of holes was reduced to lower the pressure exerted on the back wall of each blast. Several measures were taken for blasts on the western end of the pit.
Firstly, the blasting team had to double delay time between the two back rows. “We also had to reduce the burden from 2,8 m to 2,5 m between the two back lines of holes when drilling 102 mm holes. This provided faster burden response and thus limited confinement and the associated damage,” explains Mgxekwa. “We also had to cut the ends of each blast to an open angle to limit sheering and associated damage at the front corners of the next blast.”
To increase the proportion of fines in each blast, one of the recommendations by the blasting consultant was to increase hole diameter from 102 mm to 115 mm. This would increase the velocity of detonation (VOD) and subsequently the shock component during detonation. In turn, this would help to increase the annulus of crushing around each hole and optimise fracture creation in the hard andersite rock.
At the time of writing, however, this recommendation had still to be implemented. The blasting team was awaiting a drill rig that could drill 115 mm holes. “With the current 102 mm holes, we have seen massive improvements to our blast results. We are anxious to see what sort of further improvements we will experience once we start drilling 115 mm holes,” says Mgxekwa.
The amount of energy lost through the collars by blow-outs also needed to be contained within each blast. As a result, a 1,5 m stemming length was deemed too short to contain the energy. The blasting consultant therefore recommended an increase in stemming height to 2 m for 102 mm holes.
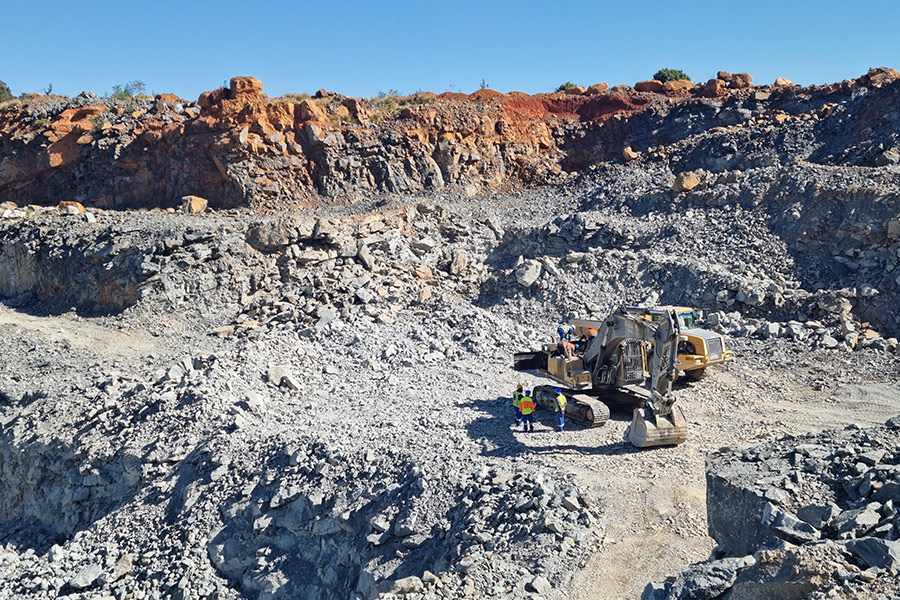
Massive results
As a result of these interventions, the issue of boulders in blasts is now a thing of the past. The proportion of boulders in each blast has been reduced from the previous 18-22% to less than 1%. “Consequently, we haven’t had a hammer on site for a long time, which significantly reduces the cost of blasting and our fuel burn on site,” says Mgxekwa.
Eliminating boulders in each blast has also translated into no blockages at the primary crusher, thus eliminating previous safety issues related to the unblocking of the jaw crusher, as well as increasing plant uptime and subsequently productivity. In fact, he says, production at the secondary plant section has almost doubled due to better fragmentation.
Due to the abrasive nature of the andersite rock, which makes it a nightmare for every piece of equipment that handles it, the quarry has always struggled with a high wear rate of liners in its primary crusher. Velapi Vilakazi, maintenance superintendent at Eikenhof, notes that following the implementation of the blast optimisation programme, liner usage life has increased significantly.
“Previously, we would change our liners every three months. With a good proportion of fines in our blasts, we have now doubled our liner life to six months. We have also seen a massive 50% reduction in our wear costs. The increased liner change intervals have also translated into less maintenance time, thus allowing the team to focus on other pressing matters on site,” explains Vilakazi.
Good fragmentation has also allowed the team to squeeze more life out of the jaw crusher. In fact, the current primary jaw crusher flywheels were due for replacement in 2022. “Because of good fragmentation, the jaw is no longer working as hard as before, allowing us to defer the replacement to 2024. We have therefore managed to squeeze more life out of this big-ticket equipment item,” says Mgxekwa.
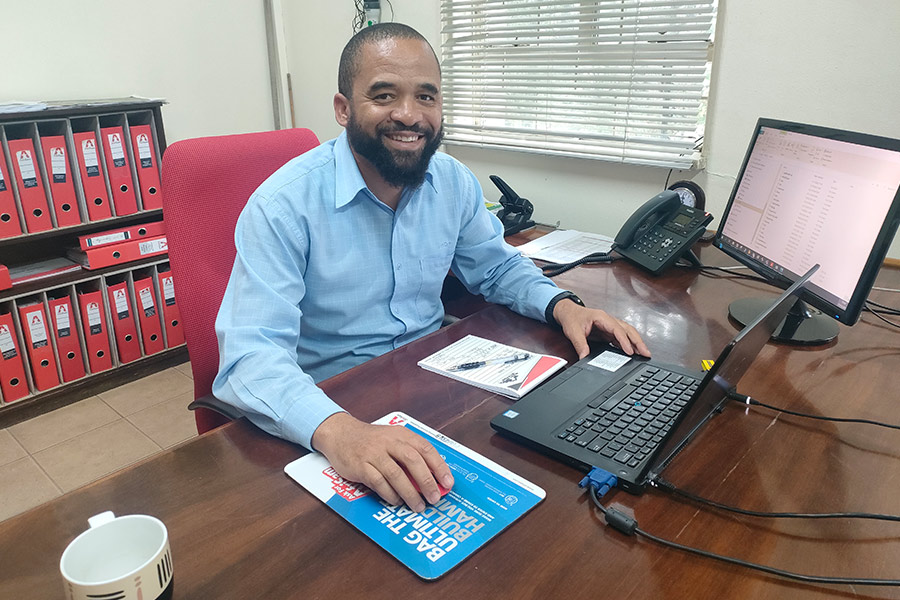
Due to the lack of optimal blasts, the Eikenhof team has traditionally struggled to produce 22 mm road stone, 7,1 mm concrete stone, and sand. As a result of several improvement efforts in the plant, the constraints around the production of 22 mm and 7,1 mm stone have been sorted out over the past two years. However, the production of sand, which currently constitutes almost 45% of the quarry’s sales, has always constituted a significant constraint.
Following the implementation of the new blast parameters, the proportion of fines in each blast has almost doubled, helping to reduce the bottlenecks related to sand production on site. “Apart from blast improvements, we have also started using poly ripple wire from Multotec on our screens. This has helped us improve the production of 22 mm and 7,1 mm products. The new screen media has helped us double the production of these products,” concludes Mgxekwa.