For any mining or quarrying project, machine reliability, high production and high efficiency for both cost and environmental reasons, are non-negotiables. While delivering on all these parameters, the new Volvo EC550E crawler excavator, now available with a Tier 3 engine for Africa and the Middle East, also breaks the industry norm of production having a direct link to operating weight, writes Munesu Shoko.
Following the expansion of the distribution of the Volvo EC550E crawler excavator internationally, quarry operators and surface miners in Tier 3 markets can brace themselves for up to 35% more productivity and 22% more fuel efficiency, combined with enhanced operator comfort and uptime.
Now available for Africa and the Middle East from January 31, 2022, the first units of the Volvo EC550E crawler are expected to ship internationally in April this year. Olle Watz, product manager – Excavators, Volvo Construction Equipment Region International, is optimistic about a positive response from African customers.
The EC550E, he says, is well suited to the mining and quarrying projects in Africa, delivering on customers’ priorities for high reliability, high production and high efficiency for both cost and environmental reasons.
Punching above its weight
Traditionally, the excavator’s production has a direct link to its operating weight. With the EC550E, Watz tells Quarrying Africa, Volvo CE managed to break the norm by introducing the Independent Metering Valve Technology (IMVT) hydraulic setup, in conjunction with a totally new engine trim on the D13 engine block and electrohydraulic command for the joysticks. As a result, the machine punches well above its weight, offering production more in line with a bigger class machine, despite the decals stating 550.
“We were able to accommodate a larger bucket (2,4 – 4,2 m³ capacity) by increasing the size and weight of the undercarriage, which gives greater stability. The more stability you have, the bigger buckets you can put on – it is the law of physics. By load distribution surface/footprint of the undercarriage, the EC550EL has almost an identical size to some competitor 70-t machines,” says Watz.
“The EC550E is well in line with heavier operating weight machines,” adds Watz. “In mass excavation (ME) configuration, it can even challenge bigger class competitors. For a typical ME machine, at 6 m reach, 1,5 m elevation – in other words where stability really counts – you have a lift value of 17 910 kg across tracks. This is, by kilos, comparable to certain 70 t competitor offerings,” he says.
The 2071 Nm (320 kW) engine, with rated power @1 600 rpm, is also well in line with certain competitor 70 t machines. This, coupled with the large displacement pumps (832 litres per minute), results in faster cycle times. For most competitor offerings in the bigger class, says Watz, one needs to rev the engine at 1 800 rpm to reach the maximum power. Low revs are generally good, so the EC550E has the upper hand here.
“Experienced people tend to be relatively more interested in torque than power when it comes to large excavators. Torque is more about force, and power is more about speed – and typically excavator force can be more a priority than speed, subject to application. However, you cannot see torque in isolation. The EC550 is fitted with large displacement pumps, matched to the capabilities of the engine. So, you can also get high flow/fast cycle times at the same time as when operating at a high torque,” explains Watz.
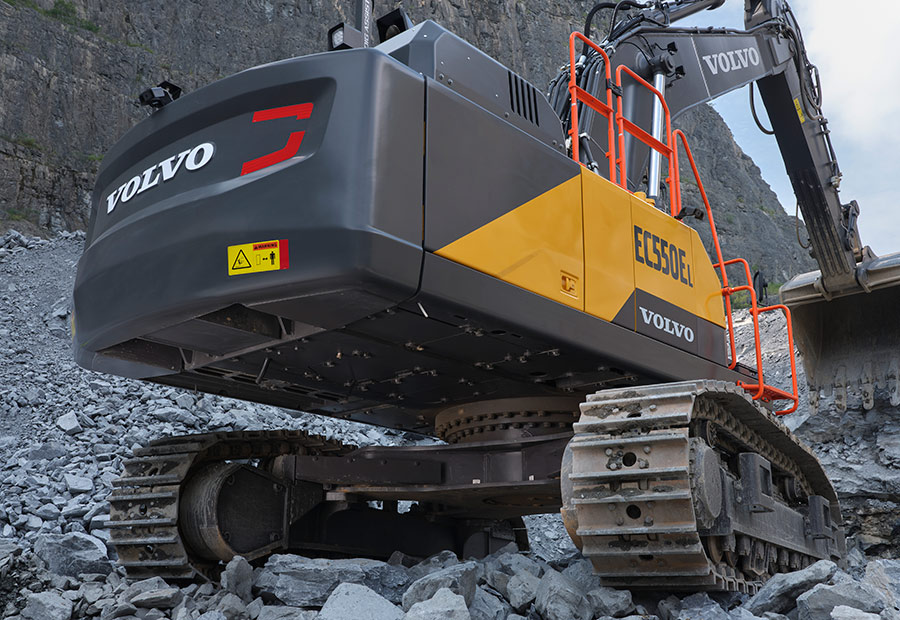
35% more productivity
Ideal for mining/quarrying, mass excavation and large infrastructure projects, the EC550 can fill a 35 – 40 t hauler or highway truck with just four to six buckets. The result is optimum pass-matching and high production at a low cost per tonne.
The EC550E can fill a Volvo A35G or A40G articulated hauler with four to six buckets, which is considered a well-balanced match in the industry. It also means that Volvo now offers two perfect match excavators for A35G or A40G haulers in Africa – the EC750D and the EC550E.
While Volvo’s existing EC480D model is aimed at customers looking for an efficient and reliable 50 t class excavator, the EC550E offers 35% greater production than the EC480D in typical dig and dump applications, meaning it is closer to the EC750D and so challenges the 60 – 65 t excavator class.
“As quarry and opencast mine operators seek to increase their tonne per hour and lower their cost per tonne, while reducing their environmental impact, pass-matching is especially important. Matching the size and capacity of the loading machine to the hauler shortens cycle times and minimises idling for greater productivity, lower fuel consumption and lower emissions. Essentially, it avoids unnecessary waste of time, fuel and money,” says Watz.
Away from the machine, the EC550E is available with a range of optimum-sized heavy-duty rock buckets designed for use in abrasive conditions, with the Volvo Tooth System making light work of teeth replacements thanks to its place, push and click functionality.
Customers can further take control of their productivity with On-Board Weighing, helping to ensure the optimum amount of material is loaded. The optional system provides real-time information to eliminate under and overloading of haul trucks and records total tonnage for complete production management.
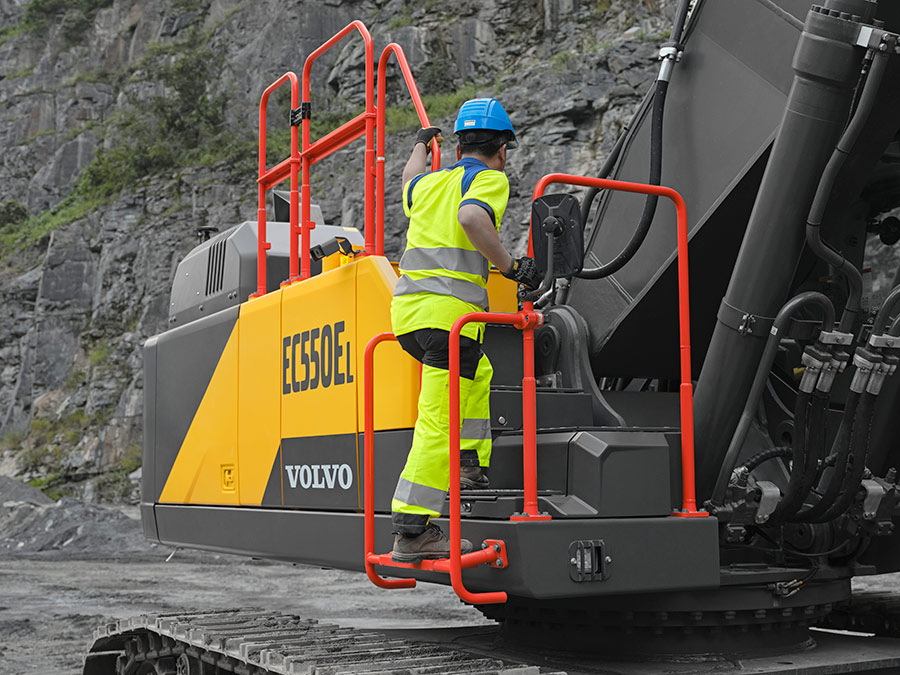
Efficiency to the fore
Customers can take fuel efficiency to a new level thanks to the next generation electro-hydraulic system with IMVT and engine/pump optimisation, which lowers engine rpm while optimising power. The main control valve uses IMVT, the latest pioneering innovation from Volvo, said to be the most high-performing hydraulic system in the industry. It provides significantly more precise control compared to a conventional system and contributes towards up to a 22% improvement in fuel efficiency.
“The IMVT is probably the biggest news as it is an industry first in this excavator size class. It involves a new concept main control valve (MCV). Instead of a conventional spool-type MCV, we have built an MCV with dedicated valves – one each for feed and return for each actuator. This means that the pumps pump exactly according to demand at any given time, subject to the precise and exact requirement of oil for any specific actuator,” says Watz.
This, he adds, eliminates hydraulic losses, delivers increased fuel efficiency and unparalleled level of command of the machine. The system does not only cut fuel consumption for mining contractors, but it also reduces carbon (CO2) emissions significantly. Operators can achieve production that is close to the 70-t mark but without the fuel consumption that comes with a 70-t class machine.
To support the fuel-efficient performance of the machine, Volvo offers a range of services to help customers reduce the fuel expenditure and carbon emissions of their operations even further, including Fuel Efficiency Reports and operator training initiatives. Using Volvo Site Simulation, Volvo dealers can also help customers to optimise site productivity and lower their total cost of ownership, by providing recommendations on the best fleet configuration and site set-up to maximise profitability.
Boosting uptime
With a host of uptime-boosting machine features combined with the support of the Volvo dealer, customers can count on the EC550E to deliver maximum machine availability. With the optional delayed engine shutdown customers can keep their turbocharger working in top condition for longer.
To avoid overheating, the intelligent function turns the machine off when the turbo charger has cooled down to the appropriate temperature. The EC550E can also be fitted with a high-performance fuel filtration system which delivers 99,7% water separation efficiency consistently over the full service life of the filter.
CareTrack, the Volvo telematics system, also helps customers to maximise machine uptime and reduce repair costs. Customers can choose to keep track of their machines themselves, or let Volvo take care of it with ActiveCare. The Volvo Uptime Centre provides 24/7 machine monitoring, supplying weekly reports and notifying customers should preventive maintenance action be required.
When it is maintenance time, grouped filters accessible from the ground level make servicing quick and easy, while the three-point right-hand access ensures the upper structure can be accessed with confidence when needed. Industry renowned features such as bolted anti-slip plates, high visibility guardrails and handrails, as well as large walkways further ensure the highest levels of convenience when servicing the machine.