Dubbed the ‘last frontier’ for economic growth, Africa is increasingly becoming an attractive destination for international companies seeking to expand their horizons. One such organisation is Bunting, a leading global magnets and magnetic equipment manufacturer for materials handling, magnetic separation and metal detection.
Bunting’s wide range of equipment features magnetic separation products, metal detection devices, custom magnets and magnetic assemblies, in-stock neodymium magnets, and more.
Bunting has been a family-owned, family-operated company since it was founded in Chicago, Illinois in 1959. In 1979, the company relocated its headquarters to Newton, Kansas, and has since branched out to establish multiple new locations in the United States and globally. To date, Bunting has locations in Bunting-Elk Grove Village and Bunting-DuBois in the United States, as well as Bunting-Berkhamsted and Bunting-Redditch in the United Kingdom; Victoria, Australia; and Ningbo, China.
Sales manager Bradley Greenwood tells Quarrying Africa that the company seeks to appoint distributors in South Africa. “Our ideal partners would be existing suppliers of capital equipment – particularly crushers, screens and conveyors – to the mining and quarrying sectors in South Africa,” says Greenwood.
Why Africa?
Africa, says Greenwood, is a strategic growth market for Bunting. The company sees huge potential and growth opportunities for its extensive line of magnetic solutions on the continent, especially in the extractive sector.
“We realise huge potential for growth and only see the market getting bigger on the back of a global shift towards a greener, electric world,” says Greenwood. The energy transition so critical to meeting the Paris Agreement is heavily dependent on green minerals. Countries such as the Democratic Republic of Congo (DRC) and South Africa are truly significant global players with substantial known reserves of green minerals in Africa.
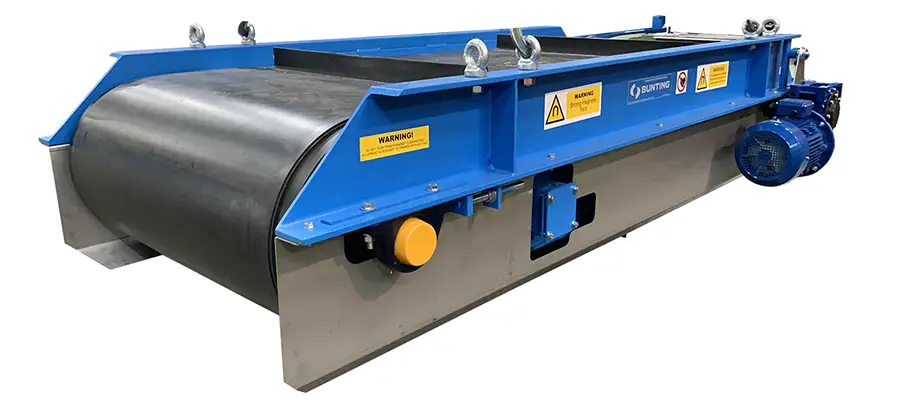
Flagship projects
Although the company has had a limited footprint in Africa, Bunting has already executed some flagship projects on the continent. Some of the major products supplied to date include disc separators, electromagnets and induced roll separators.
In Nigeria, the company has successfully installed two magnetic disc separators for processing coltan. The Nigerian mineral processor first contacted Bunting after viewing previously supplied magnetic disc separators operating successfully in other local coltan processing plants. Following a review of the project specification and subsequent recommendations by Bunting’s mineral application engineers, the Nigerian processor ordered two model MDS 3-375 magnetic disc separators.
In another project, Bunting supplied five high-intensity magnetic separators for SODEX Mines in Nigeria. The mineral processing company specialises in the production of columbite concentrates that are used in the manufacture of superconductive alloys.
Prior to contacting Bunting, SODEX Mines was using old and outdated magnetic separators. Subsequently, the company was experiencing difficulties in upgrading its final product to meet the demands of its customers. With an increasing worldwide demand for its columbite, the company instigated a global search for the best mineral processing technology to improve quality and productivity.
SODEX Mines eventually ordered five high-intensity magnetic separators from Bunting, including three 3-stage high intensity magnetic disc separators and two 2-stage high intensity induced roll magnetic separators. All the magnetic separators were fitted with vibrating feeders to provide an even, steady flow of material into the separation zones.
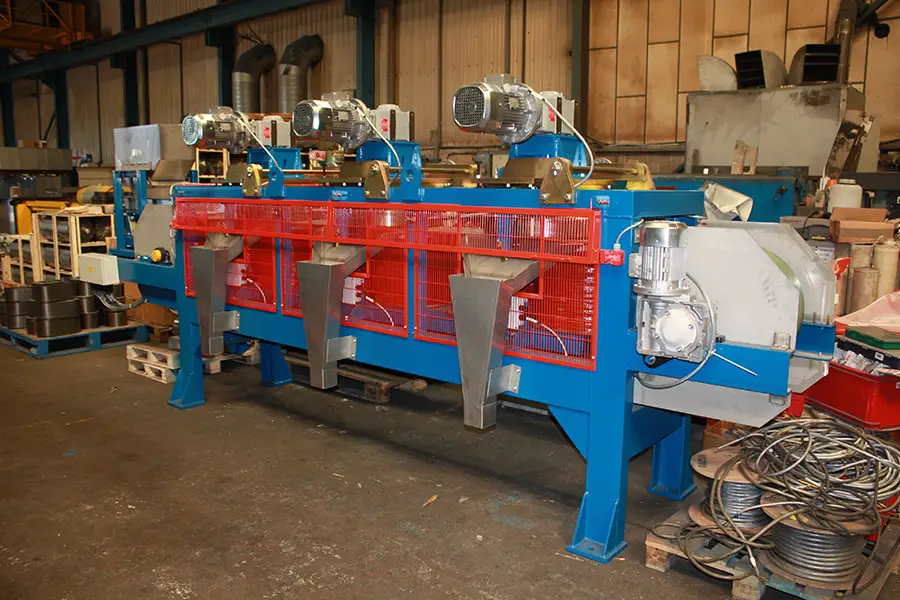
Exciting products
Commenting on products that he believes will drive the market in Africa, Greenwood is excited about the ElectroMax and TN77 metal detectors, which prevent production downtime and save on costly process plant repairs.
The ElectroMax is a new product that is selling in huge quantities throughout Europe, the UK and the United States. It is ideal for distributors to hold and sell from stock. The Bunting ElectroMax overband magnetic separator is said to be 185% stronger and 25% lighter than equivalent permanent overband magnets.
Ideal for applications in the recycling, aggregates, minerals, and mining industries, Bunting’s new ElectroMax provides customers with a smaller, lighter, and more compact system without any compromise in separation performance. The low-profile, air-cooled electromagnetic conveyor meets the ever-increasing demand for high-powered, light, and compact electromagnets.
“The ElectroMax is ideally suited for any application where there are weight and size limitations. It provides additional magnetic power for more difficult tramp metal separation applications, achieving a boosted separation force while remaining compact and light,” explains Greenwood.
The electromagnetic coil produces a high gradient magnetic field that is up to 250% more powerful than comparable equipment. This enables the removal and separation of smaller and more challenging shapes of iron contaminants often missed by other magnetic separation systems. The additional magnetic strength also aids the lifting and removal of heavier tramp ferrous metals; these traits are particularly desirable for customers in industries such as the mobile crusher market.
Five standard models are designed for suspension at a height of 35-55 cm over conveyors with widths of 1 m, 1,2 m, 1,4 m, 1,5 m and 1,8m across the transfer material belts.
Bunting’s TN77 conveyor belt metal detectors allow customers in the mining, aggregates, and mineral industries to effectively detect ferrous and manganese metal contamination from their product flow in order to purify their product and protect other process equipment downstream in their facilities.
Customers usually have three main concerns associated with installing a new piece of metal detector equipment into their facility. These concerns include the price of cost versus return associated with the purchase and installation of new equipment, the equipment’s ease of installation, and how much support they will receive from the company from whom they are purchasing.
“Bunting’s TN77 metal detector addresses all these concerns with ease. The TN77 pays for itself with the first piece of tramp metal it detects – the cost of expensive repairs associated with the damages tramp metal can cause far exceeds the cost of investing in TN77 metal detectors,” explains Greenwood.
Installing the TN77 is simple and fast, taking less than one day with no need to remove the belt of the existing conveyor. The design of this metal detector means that it easily fits onto customers’ existing conveyors, allowing material to pass beneath it with ample clearance.
“In addition to these two products, Bunting also offers permanent overband or suspension magnets, metal detectors, electromagnets, eddy current separators and a whole range of mineral separation equipment,” concludes Greenwood.
For more information on dealer partnership opportunities, contact Bradley Greenwood: bgreenwood@buntingmagnetics.com