To stay competitive in today’s business and economic environments requires new strategies and practices. Consequently, quarrying companies in Africa have been challenged to change, adapt and innovate in order to remain competitive and economically viable.
Speaking to Quarrying Africa, Scheepers says digital transformation has taken root in mining in recent years and has become central to the discussion on how the industry can further improve safety, productivity and other critical operational measures. To remain competitive in an ever-changing world, the quarrying industry, he says, should follow suit.
Traditionally, there have been many barriers to quarries adopting new technologies, primarily the economies of scale, but in an increasingly digital age, Scheepers believes that digital transformation has become a distinct possibility as digital tools, data collection and advanced analytics have evolved.
“It is true that mining companies’ budgets for technological adoption completely overshadow those for quarry operators. Understandably, aggregates are low-value material compared to commodities such as coal and iron ore, and therefore mines traditionally have more capital available to spend than quarries,” he says.
However, Scheepers is of the view that digital transformation is about leveraging all the digital tools at the industry’s disposal. From a cost perspective, there are many readily available digital tools which quarries can take up so as to accelerate their digital revolution as well as to fundamentally transform how they operate and make decisions. Digital experiences in mining, he adds, also provide a solid foundation for learning.

Available tools
According to Scheepers, it is best to start small by adding to existing technology. Sensors are the starting point for digitalisation as they are where data is created. It’s true that almost every earthmoving machine in today’s world has utilised certain sensors.
“For a long time in fact, machines have had sensors, such as pressure transducers, temperature sensors, encoders and linear sensors, to mention just a few. However, there have been some significant improvements to the extent that machines can now produce vast amounts of useful data. This not only leads to improvements in operator experience, but also gives operations a great many options in terms of planning and preventative maintenance capabilities,” he explains.
A key enabler, however, is connectivity. Without connectivity, there is no data. Without data there is no digitalisation, visualisation and transparency. To get their digital processes going, quarries should therefore invest in connectivity as the first step.
“Given that digitalisation and automation offerings are generally reliant on the Internet, the first step for quarries is to ensure that they have reliable connectivity. This can be in the form of a well-established mobile network such as 2G, 3G, 4G, 5G and/or LTE, an established Global Network Satellite Systems (GNSS) connection or Wi-Fi systems,” says Scheepers.
To harness the power of digitalisation, mines have invested heavily in their connectivity as a starting point. Quarries, being open-pit environments, have a big advantage over underground operations when it comes to connectivity as they are usually located in built-up areas and can therefore leverage existing mobile networks and Wi-Fi infrastructure. In addition, the open skies allow for GNSS connectivity.
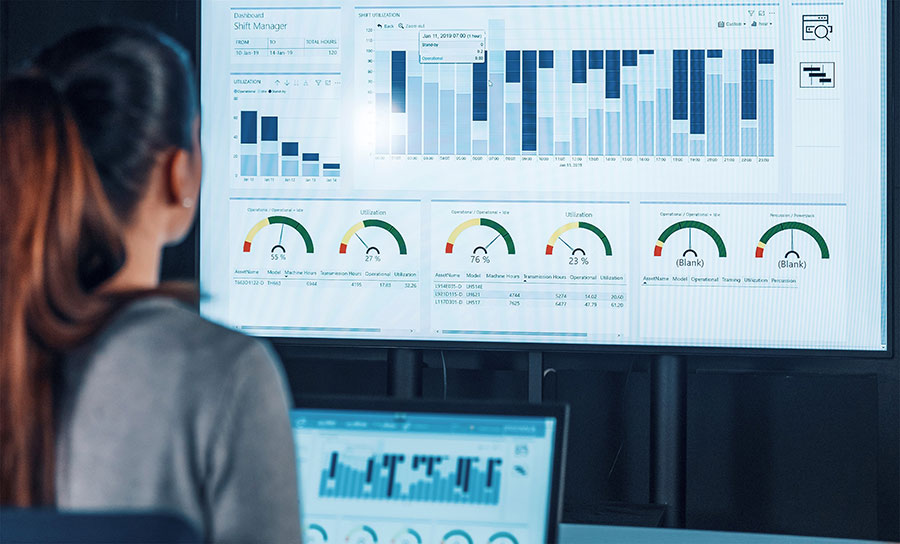
The Sandvik digital basket
Implementing digitalisation is not done in a snap, states Scheepers. The beauty of available Sandvik technologies is that quarries can choose the level of digitalisation they want by installing optional extras that speak to their exact needs or budgets.
Everything works on a digital platform. Physical sensors all over the machine take real-time data and transfer it to a central processing unit (CPU) digitally. To this end, Sandvik Mining and Rock Solutions offers its proven Sandvik Integrated Control Architecture (SICA) platform that gathers raw digital data from machine sensors and other digital tools and transforms it into useful information which humans can understand. The SICA control system is standard on all Sandvik intelligent drill rigs.
My Sandvik is another digital tool that quarries can take advantage of, in their quest to unlock productivity gains and make fact-based decisions. Various options of the online portal provide Sandvik equipment owners with visualisation of fleet utilisation, productivity, and safety on a 24/7 basis.
“Once activated, the Knowledge Box on board the Sandvik machine collects and transfers equipment data to the My Sandvik IoT hub. This is where gathered data is processed into easy-to-use knowledge about the machine’s health and performance. The gained knowledge helps fleet managers to make substantial observations and prioritise actions during daily operations,” explains Scheepers.
With SanRemo Mobile, an easy and low-cost connectivity solution for Sandvik surface drill rigs, fleet management and drilling data, such as digital drillplans, can be transferred to and from the machine, and the cloud using a mobile device. “SanRemo Mobile uses a phone or a tablet device for connectivity, thus providing Sandvik customers with the most convenient way of transferring data.”
Once installed, the application uses Bluetooth connectivity to exchange data to and from the mobile device in the vicinity of the drill rig, without the need of an internet connection. Internet access is established using wireless or cellular data connections on the mobile device, when the user heads back to the office to upload data collected to the cloud.
Driller’s Office is a practical software tool for surface drilling process management, offering better drilling accuracy, hole quality and blasting results. Designed to simplify and improve the efficiency of surface drilling management, proven in quarrying applications, it covers drill plan design, drilling data management and reporting.
The easy-to-learn and easy-to-use software follows “job site logic” and features clear and simple 3D visualisations of the drilling pattern and terrain models. Streamlining management work and removing obstacles between the quarry’s planning skills and the actual drilling work, Driller’s Office translates into considerable savings in time and money, as well as improved job site safety.
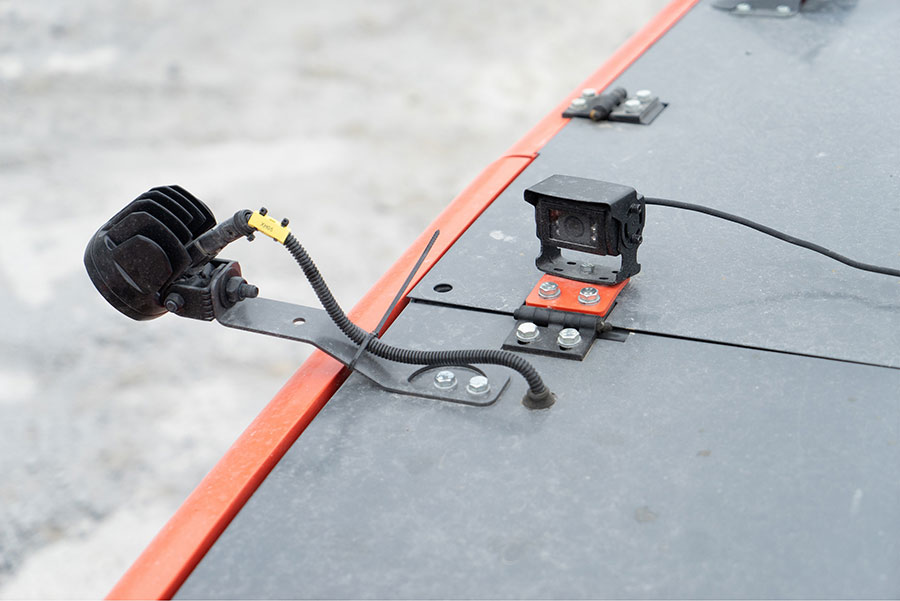
Automation
Digital transformation is not an isolated technological project. Instead, it is the combination of numerous projects that transform every aspect of an operation to be digital-first. One of the necessary steps in the digital transformation journey is automation.
Scheepers reiterates that automation is an opportunity for African quarries to improve their safety, efficiency and productivity. However, he believes that the major barrier to implementation of automated systems, especially in Africa, is that there are still uninformed viewpoints on their practicality and costs.
“This is also exacerbated by the perception that automation and digitalisation result in job losses. Automation is not about replacing people; it means that the entire team now benefits from newly efficient workflows. Automation is an opportunity for quarries to reduce operating costs, improve operations and take people out of harm’s way,” says Scheepers.
The move towards autonomous operations – especially in drilling where many quarries already own automation-ready Sandvik drill rigs – is increasingly difficult to resist. Sandvik Mining and Rock Solutions offers a high level of flexibility, allowing customers to select the level of automation that best suits their operation. Available Sandvik systems can be expanded from line-of-sight setup to control room operation many kilometres away.
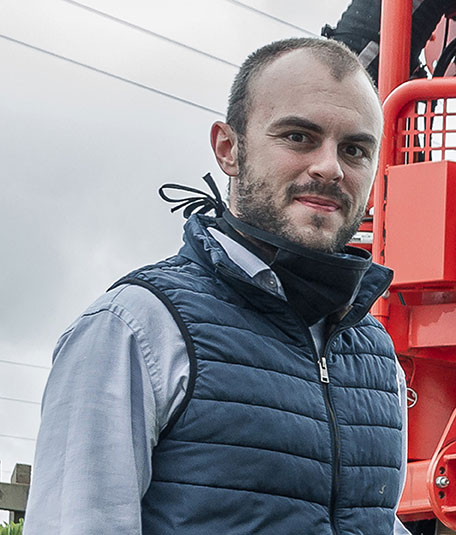
The future
Commenting on the outlook of digital and automation systems in the quarrying industry, Scheepers says the growth in take-up is inevitable. “There is no reason for quarries to be left behind in the digital revolution,” he says. “My view is that within the next 10 years, demand for aggregate will increase at an exponential rate and the industry will need to adapt to new ways of working in order to meet that demand and run profitable operations.”
Scheepers adds that there is a need for quarries to focus on continuous improvement, which will add to safety improvements, productivity gains and ultimately economic growth. “The more we can get out of each machine and increase production, the more we contribute to the growth of the economy in the long run.”
In conclusion, Scheepers stresses the importance of data management. “A company that doesn’t capture, analyse, summarise and learn from data is either dead or dying. There is an urgent need for quarries to adapt to new technology to remain relevant,” concludes Scheepers.
This article first appeared in the March-April edition of Quarrying Africa.