The articulated dump truck (ADT) market has seen several technological advancements in recent years. Since the inception of its ‘Gravel Charlie’ in 1966, said to be the first ever ADT to be made, Volvo Construction Equipment (Volvo CE) has established over decades a solid reputation for evolving machines that place innovation at the centre of their development. The primary aim in doing this is to provide hauling solutions which help to overcome project time and cost constraints.
According to GPE product manager at Volvo CE, Anteneh Gebremeskel, the company’s articulated dump truck, invented back in 1966 and known as the famous 10-t payload DR631, or ‘Gravel Charlie’, has paved the way for generation-after-generation of hauler innovation. “Our focus on new technologies has enabled us to retain a leading position in the global market,” he says.
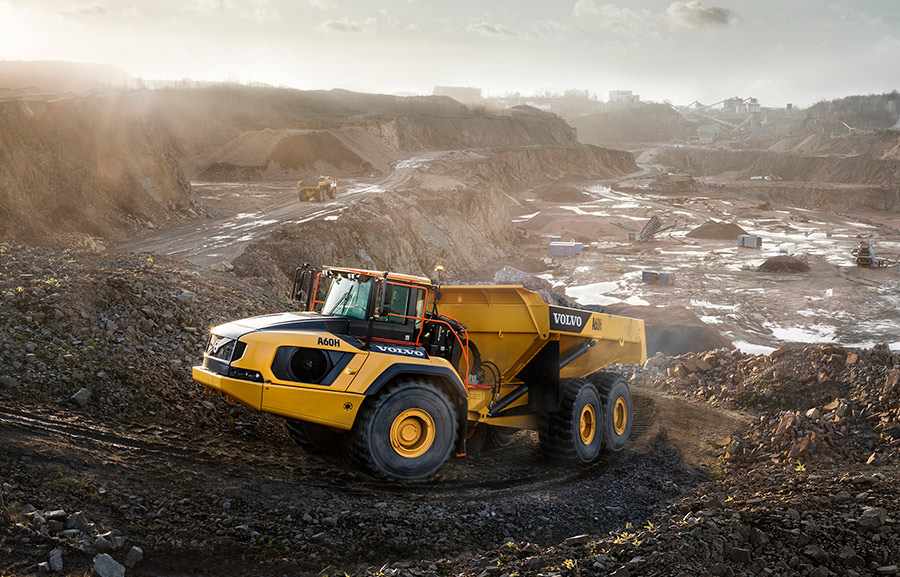
Latest advances
Some of the recent technologies that the company has brought to market include Connected Map, Cruise Control & Downhill Speed Control, Hill Assist, Terrain Memory, Dump Support System and the Tyre Pressure Monitoring System. These features cast the spotlight on hauling safety, thus helping reduce global safety incidents related to trackless mobile machinery (TMM).
Part of Volvo Co-Pilot with Haul Assist, Connected Map informs the operator of the location of other machines and personnel on site, reducing congestion and improving safety. It also issues speed limit notifications when necessary to remind operators to keep to the recommended speed for safer operation.
Cruise Control & Downhill Speed Control are important features for safety and operator comfort. The operator can set and adjust the Cruise Control to maintain a constant travel speed for smoother and more efficient hauling. “When travelling downhill, the Downhill Speed Control enables operators to maintain their control and speed for greater safety, comfort and productivity in all conditions,” explains Gebremeskel.
Hill Assist is a Volvo CE feature which contributes to greater safety by holding the hauler in place when working on uphill slopes of 10% or greater without the need to engage the parking brake. It automatically activates when arriving at a complete stop on a hill and is disengaged when the operator accelerates.
“Part of the intelligent Volvo drivetrain, Terrain Memory identifies and remembers slippery road segments that cause the automatic traction control (ATC) to engage and disengage frequently and keeps the ATC engaged to optimise traction control and off-road mobility,” he explains. He points out that Volvo CE’s CareTrack telematics system is required for this feature to function.
Dump Support System also contributes to greater safety by allowing the operator to see the percentage side inclination of the truck and sets allowable parameters for safe dumping operations. The tipping lever has automatic hold in the lowering position, which provides precise control for faster cycle times.
As part of Volvo Co-Pilot with Haul Assist, the Tyre Pressure Monitoring System gives operators an instant and safe indication that tyres are functioning within the correct parameters, thus enhancing safety, machine availability and lower total cost of ownership (TCO).
“Via the 10-inch touchscreen Volvo Co-Pilot display in the cab, operators can see real-time information on tyre pressure and temperature, both as nominal values and percentages. They also receive visual alerts if there are inconsistencies in pressure or temperature, indicating they should keep certain tyres under observation and, if the inconsistencies have worsened, signalling it is time to take action,” says Gebremeskel.
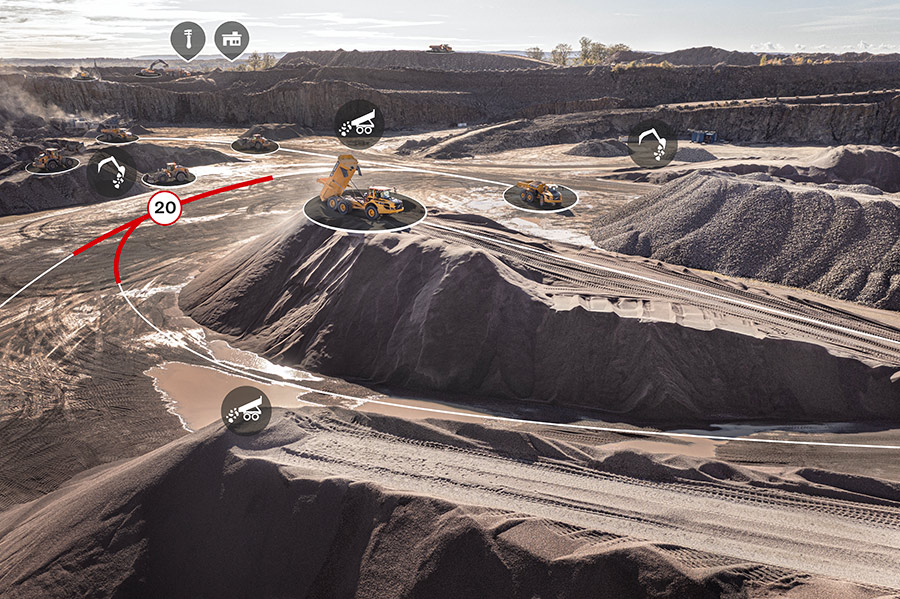
Efficiency
The importance of efficiency in hauling cannot be reiterated enough. Volvo CE has over the years brought to market some technological advancements that speak directly to better running efficiency of its ADTs.
Volvo articulated haulers’ excellent traction on slopes and in slippery conditions means that operators can maintain fast cycle times, getting the job done efficiently. Cruise Control and Downhill Speed Control also play a role in this respect.
Volvo’s Reverse by Braking (RBB) and OptiShift are key to maintaining high fuel efficiency when stopping and starting and changing directions. RBB slows the machine when the operator wants to change direction, by reducing engine rpm and automatically applying the service brakes.
“Among the newer features, Haul Assist On-Board Weighing is important for efficiency as it ensures the hauler is optimally loaded at each cycle to move more material in fewer cycles,” he says. “Connected Map also ensures operators are taking the most efficient route thus avoiding delays caused by traffic, improving cycle times and fuel consumption.”
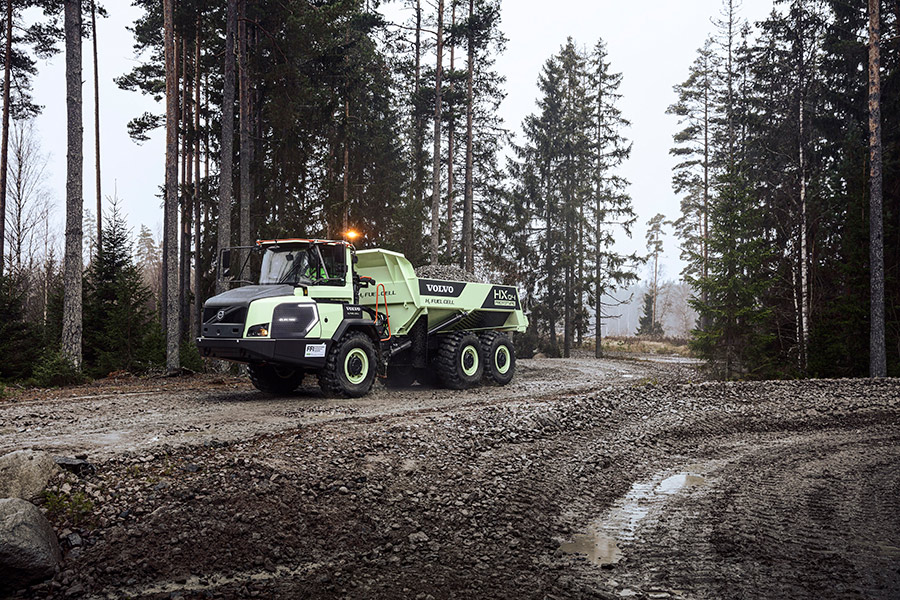
Productivity
Many of the features that improve efficiency, safety and operator convenience also contribute to greater productivity, because if operators are reducing the time taken to get the job done, they can do more within their shifts.
“However, the introduction of the largest production articulated hauler with automatic 6×4 and 6×6 configuration, the 55-tonne (t) capacity Volvo A60H, has made a particular difference to productivity in the quarrying and mining space,” says Gebremeskel. “It enabled a 40% payload increase on the popular A40G, helping operators to move more tonnes per hour, while offering a more flexible alternative to rigid haulers in this class size.”
In fact, Gebremeskel has seen a trend where customers are replacing rigid haulers with the A60H as its off-road capabilities on steep gradients and in slippery conditions enable safe and productive operation throughout the rainy seasons.
“Productivity is obviously more than just payload capacity and hauling speed. There are numerous factors that influence productivity, including uptime, fleet composition and site layout, amongst others,” he says.
“To maximise uptime, we offer a 24/7 remote machine-monitoring and a weekly fleet utilisation reporting service called ActiveCare. With ActiveCare, CareTrack telematics data is managed on behalf of the customer. Volvo and the local dealer provide remote diagnosis and become aware of problems before they occur,” says Gebremeskel.
These activities, he adds, takes the burden of monitoring and initial diagnosis off the customer, who is notified only when specific action is necessary. From the customer’s perspective, issues are resolved proactively and seamlessly with their local dealer before they have the chance to develop into serious and expensive problems – and uptime is maintained.
Another key Volvo service that improves productivity is Site Simulation. This consultancy service models and calculates the optimum flow of production over an entire site. By inputting the density of the material, distances and topography of the site, a Volvo consultant can recommend the ideal number and capacity of machines, as well as the optimum speed and routes operators should drive, based on the tonnes per hour and the cost per tonne.
“This helps to eliminate unnecessary waste and waiting and get the job done in an efficient and productive manner. Site studies such as this are regularly carried out in the mining industry, but Volvo CE is unique in its ability to offer comprehensive simulations for small- and medium-sized sites too,” he says.
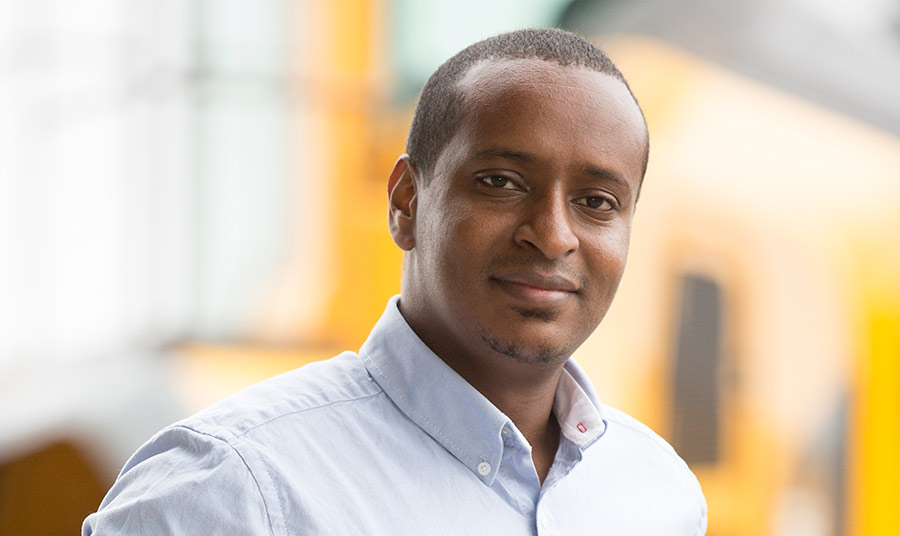
Autonomy
Autonomy is no longer a concept in ADTs. Several OEMs have already made significant headway in this area.
“Autonomy is an enormously complex challenge. Our approach has been to start small, in a tightly confined environment with a limited number of variables and build on our success over time,” says Gebremeskel.
Quarries, he adds, are the perfect place to start as they are highly regulated and contained environments with clearly defined load-and-dump locations over generally short, simple repetitive circuits that can be separated out from other processes on site. A case in point is Volvo CE’s Electric Site project, where the company tested its autonomous battery-electric load carrier concept at a quarry in Sweden in 2018.
“The next step could be underground mining and tunnel applications since autonomous machines work just as well in the dark as in the light and it would be good to remove people as far as possible from such hazardous locations. From there, we could focus on large earthmoving projects that are still contained but have more variables to cope with, as our technology becomes more embedded over time,” he says.
However, Gebremeskel stresses that any move to autonomous machines would not simply be a case of replacing a machine with an operator to one without. Autonomous machines require a new way of looking at the entire operation and prompt the development of a total solution to manage the full automated transport process.
In 2020, Volvo Group launched a new entity, Volvo Autonomous Solutions (VAS), to develop and commercialise autonomous transport solutions for the entire group. This team can focus on challenges outside of Volvo CE’s usual areas of expertise and which may be common to other Volvo business areas – namely the supporting infrastructure, control towers, repair and maintenance, virtual drivers and even running the operations if required.
VAS now offers the Tara system, which includes the fully automated Volvo TA15 battery-electric dumper, a virtual driver and support with all the necessary site infrastructure, as a complete automation solution for quarries. Improved process optimisation, lower energy consumption and greater safety are just three of the many benefits.
The future
Looking to the future, Gebremeskel says apart from battery-electric solutions, Volvo CE is also exploring the potential of electrification through hydrogen fuel cell technology. Last year, the company reached an important milestone with the testing of a world-first emission-free hydrogen fuel cell articulated hauler prototype, the Volvo HX04.
Fuel cells work by combining hydrogen with oxygen and the resulting chemical reaction produces electricity to power the machine. The only emission is water vapour.
“While an early prototype, the HX04 will give valuable insights into the opportunities of hydrogen in the energy transformation scheme alongside battery-electric solutions,” he says.
Infrastructure for hydrogen is still in development, which means refuelling the Volvo HX04 is an important aspect to solve within the project. Shell has installed a state-of-the-art hydrogen refuelling station at the Volvo CE test track in Braås, Sweden, which can refuel the HX04 with 12 kg of hydrogen in around 7,5 minutes, enabling it to operate for approximately four hours.
“In the immediate future, however, customers in Africa should look forward to seeing Volvo Co-Pilot with Haul Assist on their new machines, including On-Board Weighing and other valuable features. Volvo Co-Pilot builds on all benefits of the Volvo transmission and drivetrain to deliver new levels of safety, efficiency and productivity,” says Gebremeskel.
On-Board Weighing, in particular, helps eliminate dangerous overloading, and to improving safety and decreasing unnecessary fuel consumption and wear to the hauler. The system provides real-time payload information to the screen in the cab and uses external lights as a visual guide for the operator of the loading unit as to when the nominal load has been reached. It also enables remote monitoring of productivity.
“We will continue to develop Volvo Co-Pilot with Haul Assist as a platform for further services in the future, so watch this space,” concludes Gebremeskel.