Mines and quarries are under extreme pressure to increase output while lowering input in order to remain profitable. One area where this is apparent is in drilling and blasting. Drilling, in particular, is the first unit operation that has a significant bearing on other downstream functions in the mining value chain.
Modern drilling operations are defined by efficiency and reliability, two factors that are fundamental in reducing operational costs and maximising productivity. Consequently, the utilisation of innovative drilling technologies holds the promise for efficient and productive operations.
According to Linton, drilling and blasting techniques have become increasingly technical over the past 35 years, calling for the constant evolution of drilling technology to meet customers’ ever-growing and changing requirements in the quarrying and mining sector at large.
“Furukawa Rock Drills (FRD) is on a continuous quest to upgrade its equipment to meet the performance, safety and efficient operation procedures required in the marketplace, with a large emphasis on ergonomics and ease of operation,” explains Linton. The range is distributed by ELB Equipment in southern Africa.
The close cooperation between the Japanese original equipment manufacturer (OEM) and its southern African representative has culminated in the development of products that speak directly to the local clientele’s requirements. A case in point is the all-new FRD HCRL100-E3 crawler drill launched in August 2023 to drive down the cost of drilling in southern Africa. The raft of changes on this model was informed by customer input and feedback from FRD’s longtime distribution partner, ELB Equipment.
“The latest adaptations are the culmination of decades of successful operations in the field, in Africa, which has allowed FRD to continue fine-tuning its offering for even better performance, speed and cost-per-metre drilled,” says Linton.
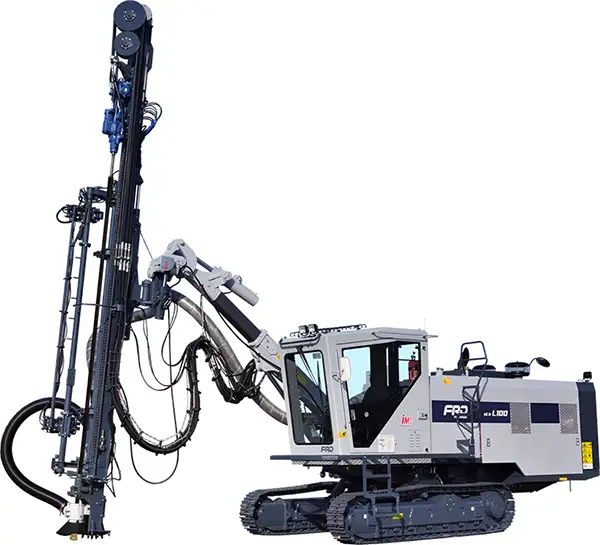
Economic drilling
The FRD HCRL100-E3 is a radical upgrade of the previous FRD HCR 1500 ED-II model, which had become popular among mining, quarrying and construction contractors across southern Africa. The launch of the FRD HCRL100-E3 late last year ushered in a new era in economic drilling in southern Africa.
Linton makes special mention of the Intelligent Drilling System (iDS), FRD’s semi-automatic drilling control which automatically provides for optimal drilling conditions according to changes in rock quality. This results in smoother drilling, reduced hole deviation (a major factor in production efficiency) and extension of the service life of drilling accessories. With the iDS engaged, the drill will only use as much power as is needed to save fuel and minimise unnecessary wear and tear on the system.
The iDS is complemented by the power-saving mode on the new 280-kW Caterpillar C9.3 engine with an auto idle feature which provides economical fuel consumption. With the Super Economy Mode PLUS fuel-saving technology, the engine speed during drilling (impact and blow operation) can be selected from four levels: 1 600, 1 800, 2 000 and 22 00 rpm.
By selecting the appropriate engine speed according to the rock quality, this patented fuel-saving technology contributes to improved fuel efficiency while maintaining impact performance. This reduces fuel consumption by up to 8,5% and enables more power to be channelled towards increased speed and more metres drilled per shift with drill bits up to 127mm diameter.
The dual damper mechanism and wedge-shaped piston shape, with extreme energy transfer efficiency, enable quick response to a wide range of different rock types. High crushing efficiency is achieved by optimal control according to the load. No complicated operation is required, and stable and comfortable drilling is possible with no wasted power.
The dual damper mechanism (shock absorber with special structure) presses the bit against the bedrock in order to reliably transfer the energy of the impact wave of the impact piston to the bit. This causes crushing of the bedrock, and enabling drilling with the proper thrust force.
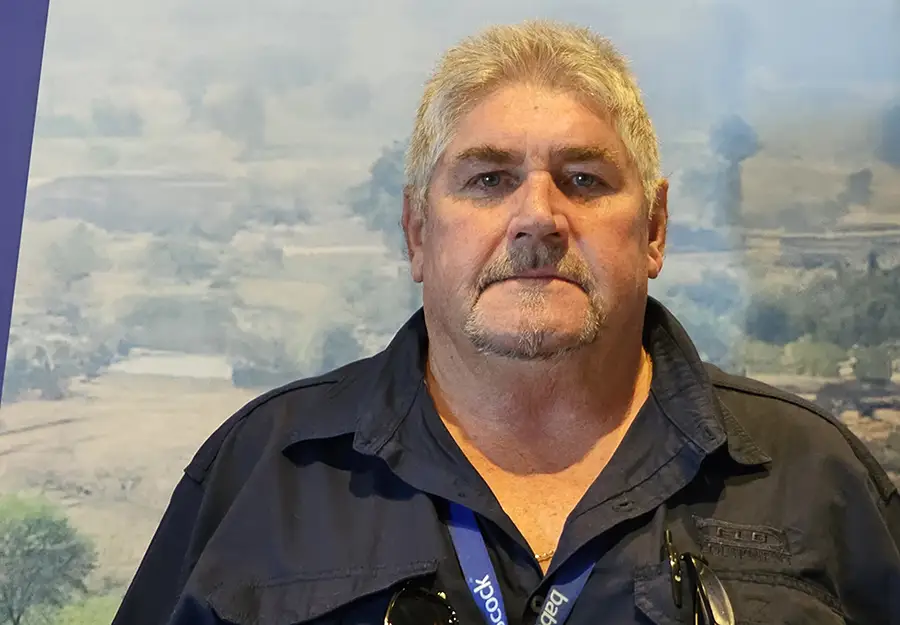
Quick uptake
Since its launch in August 2023, the HCRL100-E3 has been well received by customers in southern Africa. ELB Equipment, confirms Linton, has already put four units into the market, with the fifth unit currently being prepared for commissioning at a fluorspar mine in Limpopo. “We anticipate deploying at least two more units into the market by August 2024,” he says.
Of the four units already in the field, three are working in chrome applications in the North West Province of South Africa, while the remaining unit is running at a large bridge construction application. “The performance of the HCRL100-E3 in the chrome application has been astounding. Here, the ore dips at around 12 degrees, sometimes at a depth of 20 m. The HCRL100-E3 is cutting at 23 m/hour with a 127 mm drill bit,” explains Linton.
Apart from the FRD HCRL100-E3, ELB Equipment offers FRD’s full range of drill rigs catering for the mining and construction industries from start-up and production to geotechnical applications. These range from pneumatic crawler drills to hydraulic top hammer and medium range down-the-hole (DTH) crawler drills. “In fact, FRD has a unit for every rock drilling application,” concludes Linton.