With productivity high on the agenda, Zizwe Opencast Mining does not leave anything to chance when it comes to the selection of its equipment for its mining projects. It is for this reason that the company has opted to deploy a fleet of three Metso mobile machines supplied by Pilot Crushtec International at one of its chrome processing contracts in Steelpoort. The train comprises a Lokotrack LT120 jaw crusher, a Nordtrack S2.11 scalping screen and a Lokotrack LT200HPS cone crusher.
As part of the production process, -450 mm run of mine (ROM) material is fed into the Lokotrack LT120 jaw crusher, which crushes it down to a -80 mm, which is in turn fed into the Nordtrack S2.11 scalping screen for further processing. At the scalping screen, the production team takes out sellable -15 mm product.
Any oversize material from the scalping screen is fed into the Lokotrack LT200HPS cone crusher, which crushes it down to the desired -15 mm product. Anything above the -15 mm spec is passed onto the LT200HPS’s on-board return conveyor, which recirculates it back to the crushing chamber for a second or even third crush.
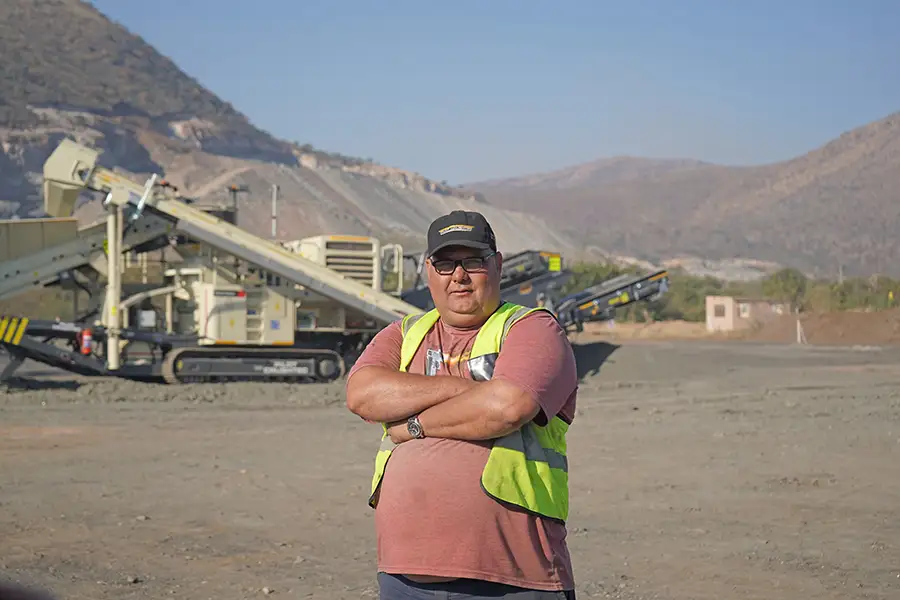
With the high production nature of the Metso machines, coupled with their reliability and ultimately high availability, Zizwe is meeting its production target of 200 tonnes per hour (tph), confirms Rayno Combrick, crushing and screening foreman at Zizwe. “We are very happy with the performance of the Metso machines we have deployed on this particular project,” says Combrick.
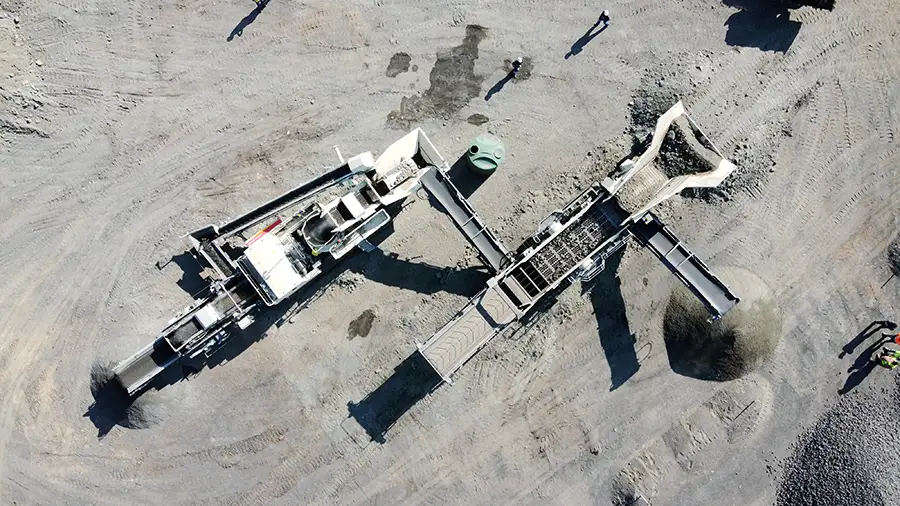
Two in one
While all the three machines have proven their mettle, Joe de Beer, crushing and screening plant manager at Zizwe, is particularly impressed by the newly acquired LT200HPS cone crusher. By featuring a detachable screen and return conveyor on one tracked chassis, he says, the LT200HPS is basically two machines in one, which eliminates double handling on site.
“The fact that the LT200HPS does the job for two machines was central to our purchasing decision. It features a detachable screen and return conveyor which guides screened oversize material back to the cone crusher. It is essentially a cone crusher, a screen and a conveyor on one tracked chassis,” says De Beer.
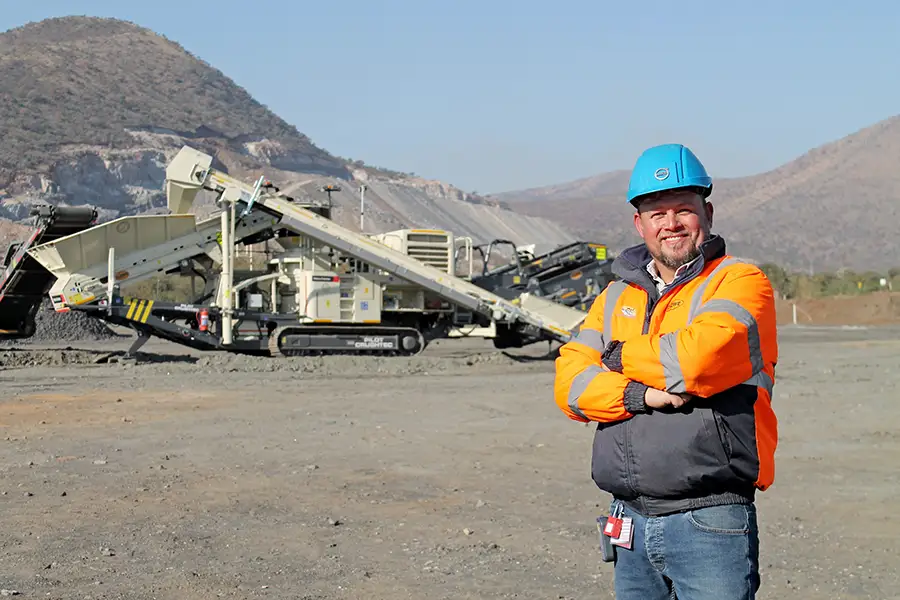
Francois Marais, sales and marketing director at Pilot Crushtec, tells Quarrying Africa that this is the first ever LT200HPS with an overhanging screen to be supplied in the local market by Pilot Crushtec. In fact, the LT200HPS now comes in three different configurations, depending on individual customer needs. Apart from the standard cone crusher configuration, he explains, it is also available with a pre-screen called the HPX, which is placed just before the crushing chamber, or alternatively with an overhanging screen called the HPS, located post the crushing chamber.
“In traditional operations, you would need two machines – a cone crusher and a screen – to do the same job done by this machine on its own. In addition, you would probably have to deploy a minimum of two or three conveyor belts to recirculate oversize material from the screen back to the cone crusher,” says Marais.
Yeshen Achary, sales engineer at Pilot Crushtec, explains that Zizwe was looking for a single machine that could do the job of two machines. “Traditionally, we have always supplied the LT200HP in a standard configuration. Because cone crushers by their nature are not 100% efficient, the added benefit of having a screen post the crushing chamber is that it allows for recirculation of any oversize material back to the cone crusher,” he says.
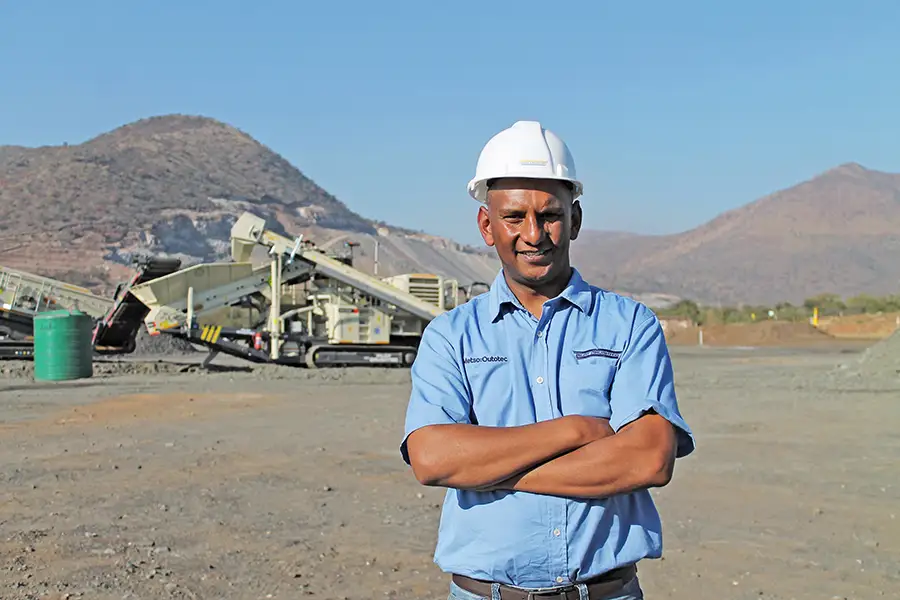
This, explains Achary, eliminates the need for another machine to work in closed circuit with the cone crusher. Having a single machine doing the job of two machines offers significant cost benefits for the customer. Apart from the obvious capital cost benefit, having the cone and screen on one single chassis means that the machine is powered by a single engine, thus one less machine to maintain. Having a closed loop on a single chassis also makes it easy to transport the machine to site.
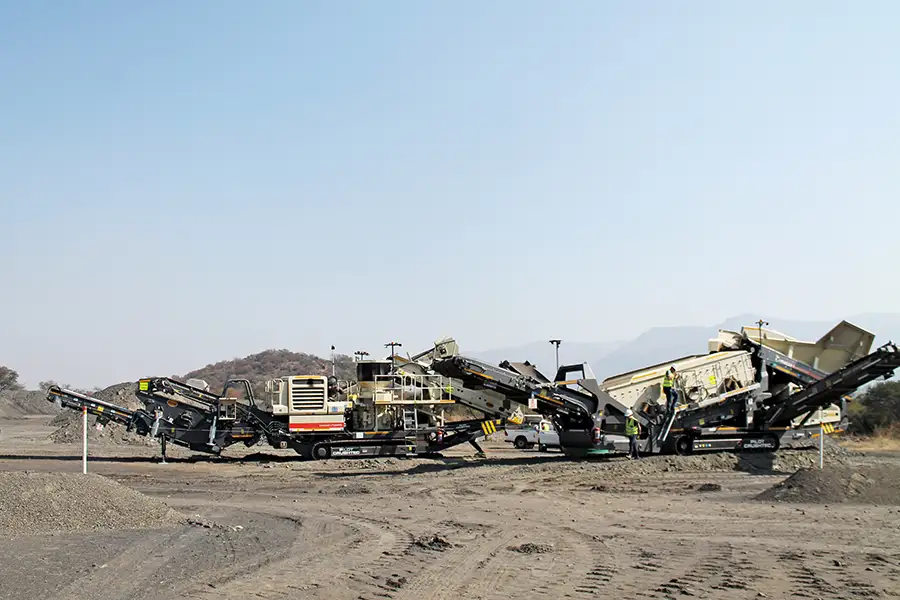
Why Metso?
Zizwe currently boasts a mobile fleet of 24 crushers and 15 screens, comprising various brands. Of the 35 machines, nine are Metso units – six jaw crushers, two cone crushers and one scalping screen. The company generally replaces its crushing equipment at 15 000 hours. In future, confirms De Beer, Zizwe is looking at standardising its whole fleet with Metso equipment.
Why Metso? Several factors, he says, are central to the decision, but more importantly it is the proven reliability of Metso machines. To provide context, Zizwe’s first Metso machine, a Lokotrack LT105 jaw crusher purchased in 2012, has clocked over 30 000 hours and is still going strong at one of the company’s crushing sites.
“The main reason behind our preference for Metso is the durability and performance of the machines,” says De Beer. “Added to that is the unparalleled aftermarket support we get from Pilot Crushtec. Worth mentioning is the parts availability, which is key to our machine uptime. Downtime is the enemy of success in our line of business. We therefore value a partner that we can trust for the long haul, while offering the best deal possible.”
De Beer makes special mention of Pilot Crushtec’s SupportLink service offering, which provides equipped, qualified and experienced personnel to professionally service and repair all the equipment supplied by Pilot Crushtec.
According to Marais, Pilot Crushtec has, over many years, reiterated its commitment to customer service by investing heavily and continuously in service infrastructure, spares and wear parts as well as in the continuous training of its people.
“We train, develop and retain the skills necessary to keep customers’ equipment up and running – to avoid costly downtime that could threaten their contracts and reputations,” says Marais. “This includes our 15 full-time service technicians, who travel over a million kilometres a year to see customers and deliver quality support.”
Underpinning these levels of service – which are available 24/7, 365 days a year – is the company’s parts and aftermarket infrastructure, which is similarly always open for business. This starts with a large stockholding of around 93 000 individual items, including about 2 500 wear parts alone. There are 20 dedicated parts personnel to efficiently manage this valuable resource, dispatching on average about 6 800 parts every month.
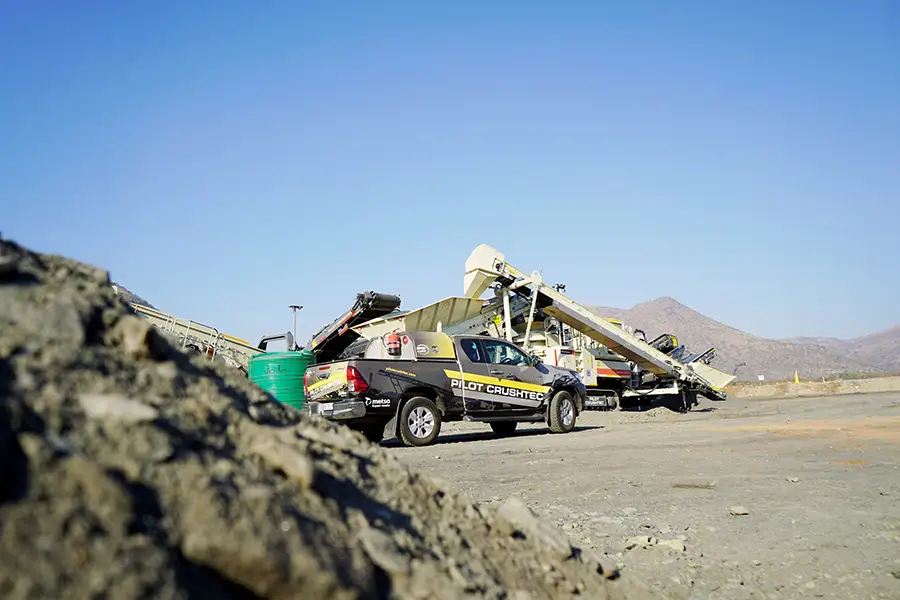
Peace of mind
Zizwe also places value on the industry first, standard 5-year/ 10 000-hour EPS warranty offered on all Metso crushers and screens. De Beer says the extended warranty is a true reflection of Metso’s confidence in its product and Pilot Crushtec’s service commitment to the brand.
“Warranty is a valuable component of any capital equipment purchase, especially mission-critical equipment such as crushers and screens. A long product warranty gives us some extra coverage for our big-ticket assets, along with a little more peace of mind,” concludes De Beer.