As the quarrying industry adapts to the changing operational environment, quarry owners are increasingly looking to digital technologies to enhance productivity, efficiency and take people out of harm’s way. Eeje van Jaarsveld, business line manager – Technology and Digital at Epiroc South Africa, tells Quarrying Africa that the uptake of digital solutions at quarries in southern Africa is largely being driven by contractors.
“Most of our digital technologies in the local quarrying space are adopted by drilling contractors, because quarries in the region generally outsource their drilling functions to contractors,” he says.
While quarries generally lag behind their mining counterparts when it comes to digital transformation, Van Jaarsveld believes that as the industry transitions through the current crisis and aims to thrive in the ‘new normal’, there is a window of opportunity to accelerate digital transformation and advance the future of quarrying.
The 6th Sense is Epiroc’s way to optimise the industry’s value chain through automation, system integration and information management – enabling smart, safe and seamless operations. With 6th Sense comes a great focus on system connectivity, using interoperability to unlock the full potential of automation for production gains at lower operating costs.
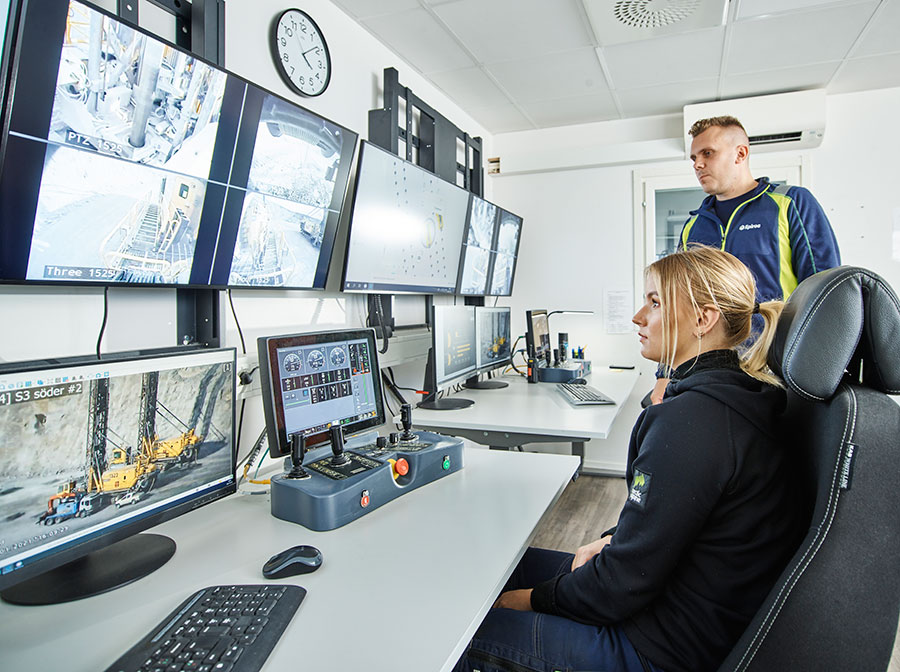
6th Sense in detail
The 6th Sense entails three major legs – Machine Automation, Process Automation and System Integration, explains Van Jaarsveld. Three foundational elements – Insights, Control and Optimisation – are key to achieving Machine Automation, Process Automation and System Integration.
The system outputs of Epiroc’s 6th Sense approach are increased productivity, efficiency and safety. To achieve these outputs, Epiroc’s implementation focus considers people, processes and technology maturity.
“Machine automation entails various systems developed to ensure that an individual machine performs optimally, while process automation is all about systems developed to ensure the process performs optimally. System integration means that systems are developed to tie together the optimised portions of the value chain to operate as an ecosystem,” explains Van Jaarsveld.
Insight – transparent information in support of good decisions – is the starting point to reaching the three pillars of digitalisation. Data, stresses Van Jaarsveld, is key in the modern world. The massive amounts of data being generated in daily operations only turn into true value if retrieved, stored and analysed in a timely manner.
The 6th Sense Insight product family therefore comprises solutions for collecting, transferring, storing, visualising and analysing the data, transforming it into useful information for better decision making. These include My Epiroc, Telematics, Analytics, Rig Remote Access, Measure While Drilling, MineRP InterOp, Mobius for Drill and Surface Manager.
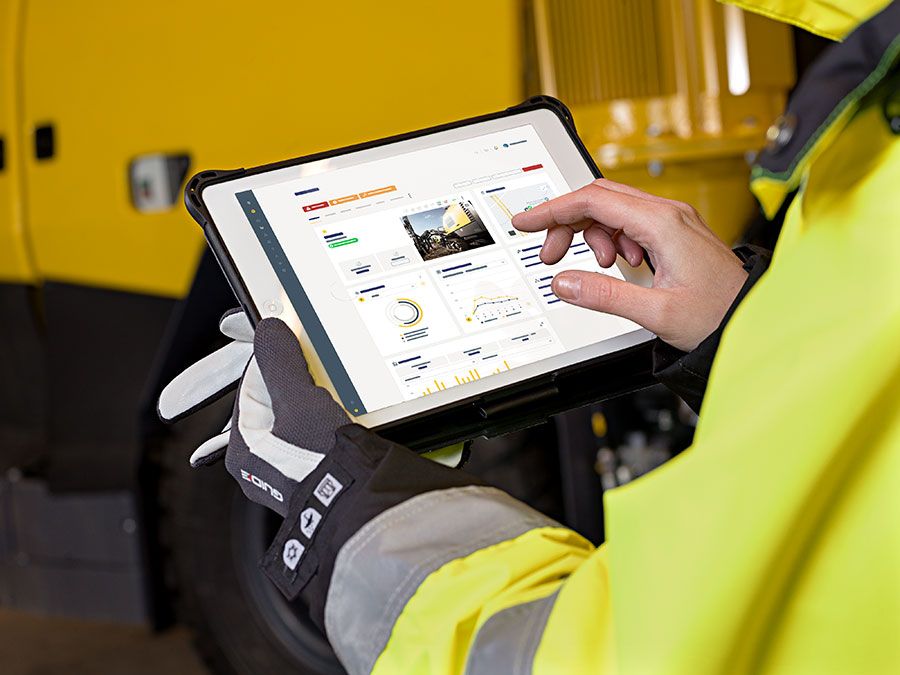
Automation
As part of the Control pillar, quarry operators can use various machine automation technologies from Epiroc to increase productivity in a safe, consistent and predictable way. “Automated and tele-remotely controlled operations can significantly increase productivity and improve safety at the same time. Automation can also increase consistency of daily operations and provide predictable results,” says Van Jaarsveld.
One example of Epiroc’s automated solutions that can be of great benefit to the quarrying industry is the fully autonomous SmartROC D65 surface drill rig. SmartROC D65 consistently delivers high-quality blast holes with accuracy and precision. It is loaded with smart features such as automated drilling and rod handling. The automation-ready platform also includes an Auto Feed Fold option. With a single action, the Auto Feed Fold enables the operator to fold the feed for tramming or position it for drilling.
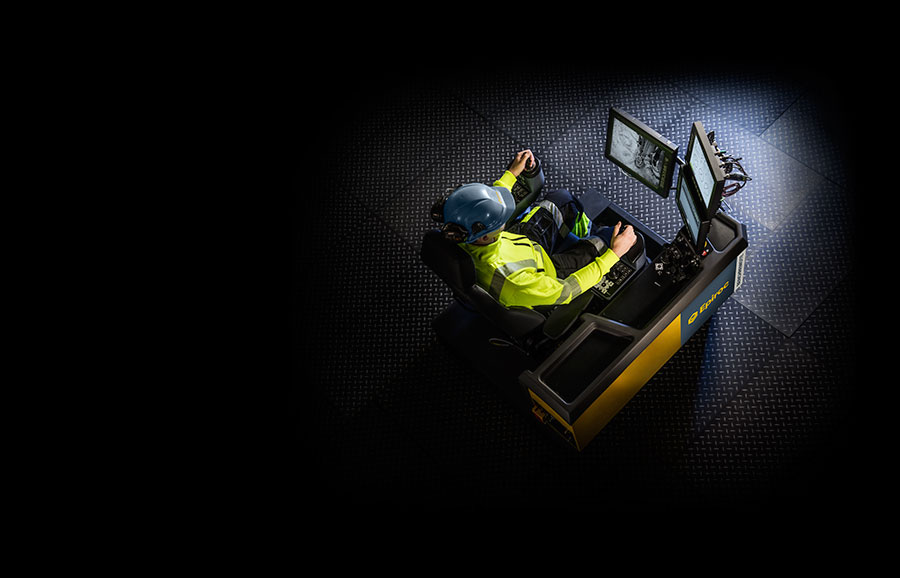
The BenchREMOTE option – a remote operator station designed to control SmartROC rigs – makes it possible to remove the operator from dangerous areas. It enables operators to work at a safe distance of up to 100 m. BenchREMOTE can handle up to three SmartROC rigs in parallel – taking productivity to a new level. Thanks to an automated drill cycle, BenchREMOTE can control up to three SmartROC rigs at the same time. This dramatically increases operator productivity. Each BenchREMOTE can be pre-programmed to recognise ten rigs, making the planning process easier.
Optimisation, one of the foundational elements in Epiroc’s digital journey, enables processes to be executed and equipment to be operated with full potential through improved efficiency and higher utilisation. Some of Epiroc’s products in the 6th Sense Optimise family include High Performance Development, Stope Optimisation, Transport Loop Optimisation and Application Expertise Services.
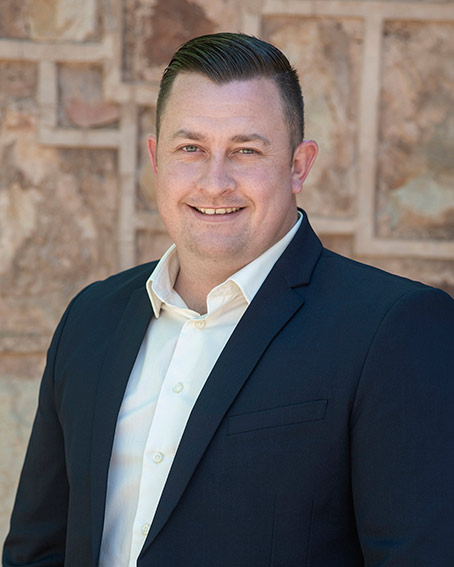
Implementation focus
For customers to achieve the required outputs of their digitalisation strategies, Epiroc considers three important elements as part of the implementation focus – people, processes and technology. People, says Van Jaarsveld, are central to the success of any digitalisation strategy.
“As part of the implementation focus, we look at the people. Before any technology implementation takes place, we need to understand the people working on site, because any strategy is only as good as the workers. It’s important to determine whether the people in the organisation understand the technology and identify areas of improvement necessary for the strategy to realise the desired value cases,” he says.
“Peter Drucker once said ‘culture eats strategy for breakfast’. Without people or culture alignment, the technology implementation will not get the desired results, because the people are responsible for executing the strategy,” adds Van Jaarsveld.
Processes are important in Epiroc’s implementation focus. Before the technology rollout, Epiroc looks at the operation’s existing processes. For example, does the quarry use a drill plan in its drilling process? This helps to establish the level of process maturity on site or within the organisation.
“It’s important to understand the current processes and capabilities on site. People and processes determine whether the technology implementation will be successful or not – there is no magic fix. If a site has the necessary people-culture alignment and the processes are mature, it becomes easy to adopt digital technologies,” concludes Van Jaarsveld.