It is common knowledge that no one runs a business with the goal of losing money, but when it comes to profit margins, those for crushing contractors in South Africa are among the smallest in the world. In such a volatile and competitive market, Danoher Group, a major contractor which operates some 50 crushing and screening plants in southern Africa, does not leave anything to chance when it comes to the selection of its equipment – critical assets which are key to the success of its business.
Since its inception, Danoher Group has established itself as a household name in the southern African quarrying/mining industry, providing a full basket of contracting services from drilling and blasting to crushing and screening (mobile and static). One of its key success factors, notes CEO Scott Danoher, has always been the careful selection of its equipment and optimisation of asset performance to ensure efficient operations.
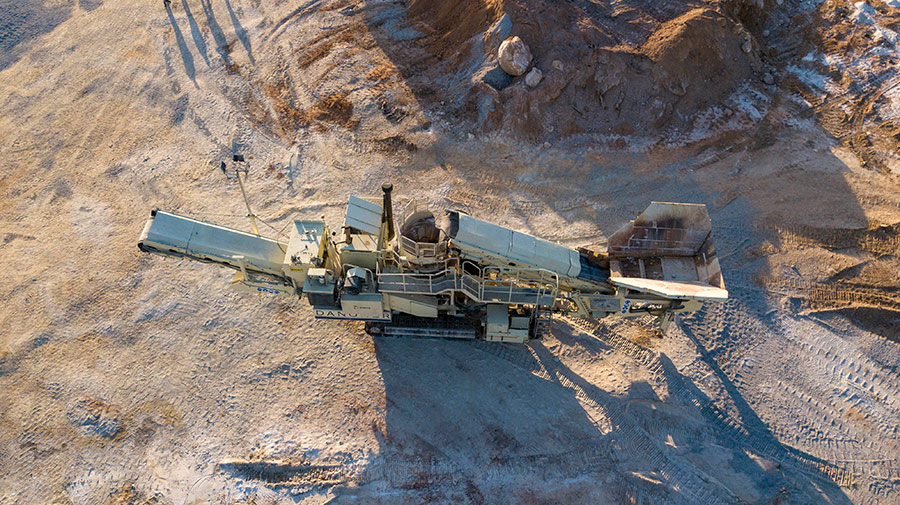
What informs buying decisions?
Commenting on what informs the company’s buying decisions, Danoher says, first and foremost, the company runs an established standardisation policy. Trusted brands such as Metso (crushing and screening) are preferred and maintained to the highest standards, ensuring optimal plant availability.
Since its inception, Danoher Group has always positioned itself as a premium service provider and this is projected through the equipment it runs and the condition in which it is kept. Reputation, stresses Danoher, is everything for the company and this is mirrored by the service it delivers.
One of the fundamental factors that informs buying decisions, however, is equipment longevity. While there are various factors that affect the longevity of equipment, Danoher says the principal ‘raw material’ is the design of the machine, an area where the Metso product excels.
“We do not necessarily buy a crusher or a truck, for example, for whatever amount, we buy the number of hours that it gives us,” he stresses. “For us, it is also not about the price tag, it is more about the cost per tonne or cost per hour – ‘cradle to grave’, which is a totally different dynamic. We are prepared to pay a premium upfront for, say 30 000 trouble-free hours out of our crushing equipment.”
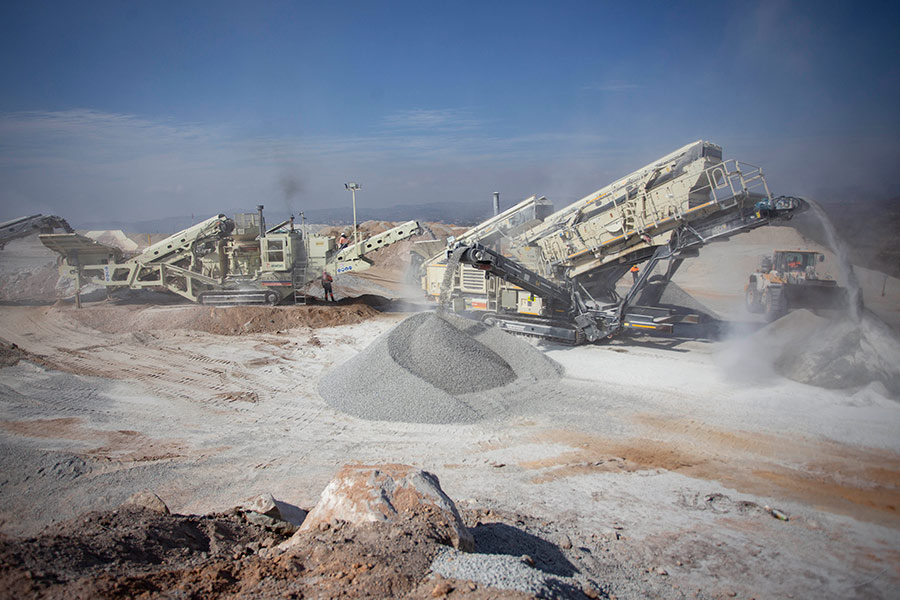
Longevity redefined
Based on this approach, for the past 15 years Danoher Group has neither retired nor scrapped a machine within its crushing and screening fleet.
Over the years, the machine, a Metso LT300HP crusher with over 30 000 hours, has been deployed on some flagship projects in South Africa and Botswana. In fact, it has been in Botswana on four occasions during the past 12 years, where it executed some major projects at flagship mines such as Debswana’s Orapa Diamond Mine and Khoemacau, a long-life, copper-silver mine located in the Kalahari Copper Belt. During its stay in Botswana, the machine has also been deployed at Danoher’s own Kgale Quarry in Gaborone.
Currently, this particular Metso LT300HP unit has been deployed at a major job in Mbombela, Mpumalanga, where Quarrying Africa was recently invited to see it in action. Here, the machine is working in a train with a Metso LT120 jaw crusher and a Metso LT330D cone-screen combination. The scope of the project entails the production of 350 000 tonnes of road stone for the rehabilitation and upkeep of the N4 Toll Concession. Material from this particular pit is supplied to five road contractors working on five sections of the road project.
After this project, Danoher tells Quarrying Africa that the machine will be deployed at another job near Malalane in Mpumalanga to crush material for the other four sections of the N4 road rehabilitation and maintenance project.
Asset care
Every asset, says Danoher, has an optimum operating period of peak performance. After a certain period of use, wear and tear takes its toll as the asset ages. Eventually, this calls for some interventions at certain stages of the asset lifecycle.
“We basically expect 30 000 hours out of the motor during the first life of the machine. The crusher itself would probably come out for minor refurbishments a few times before the 30 000-hour mark. The electronics are probably the least robust components of the machine and thus need ongoing work during the life of the machine. The hydraulics, if looked after properly, can last for the whole life of the machine,” explains Danoher.
While the Metso LT300HP machine is still due for a second life overhaul, it has already been afforded a midlife refurbishment. Key factors that determine the time for a midlife are the cost per hour and availability.
Capital equipment is costly even at the best of times, says Danoher. Given the tight profit margins in the contracting fraternity, it is even more challenging or downright impossible to purchase new equipment at this stage, unless one is confident in the equipment delivering sufficient hours to make it profitable. Consequently, the company finds comfort in its Metso gear which, according to Danoher, provides unmatched long-life in the industry.
“Ultimately, it becomes a mathematical exercise as to what the second life is going to cost and how many hours more it will provide, versus buying a new machine,” he says.
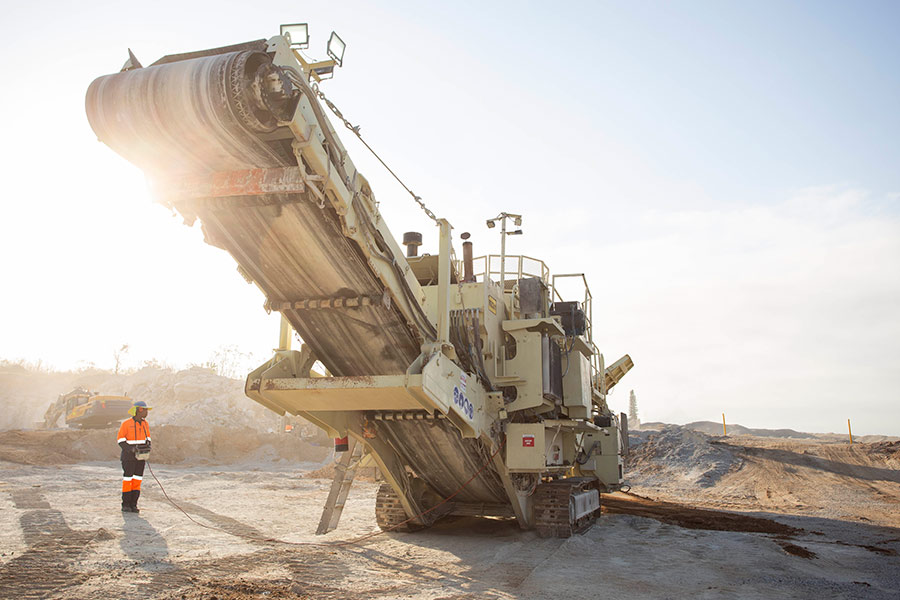
Maintenance regime
Apart from midlife and second life interventions, Danoher’s equipment generally benefits from a well-executed maintenance regime. Site teams are trained to focus their efforts on keeping the assets in good working condition to ensure efficiency and productivity, using preventative maintenance programmes, regular inspection schedules and regular routine maintenance.
“The backbone of our machine longevity is our maintenance philosophy. We instil in our site teams that their core job is maintenance. With a good maintenance regime, production takes care of itself,” explains Danoher. “We always try to be proactive when it comes to wear checks. We have an online maintenance system where faults are checked and recorded twice a day. Although these interventions are not 100% ‘silver bullet’ solutions, they contribute to machine longevity,” says Danoher.
With a similar approach to its capital purchases, Danoher buys a large percentage of its spares directly from the Metso OEM supplier, Pilot Crushtec International. The company also spends significantly in its own spares stockholding at site level to ensure machine uptime.
Over the years, Danoher and Pilot Crushtec have built a strong working relationship, a key parameter in Danoher’s buying decisions. “Relationships play a crucial role in what we buy. While a good product is principal, we also place value on the relationship with the equipment supplier and the people – that is very important. For us, Pilot Crushtec are more than just suppliers: they have become trusted business partners. Their parts stockholding is impressive and we are generally happy with their technical backup capabilities as well,” concludes Danoher.