That proximity detection systems have traditionally been deemed a ‘grudge buy’ in the surface mining industry is no overstatement. However, Anton Lourens, CEO of leading PDS and CPS provider Booyco Electronics, tells Quarrying Africa that there is an apparent change in attitude, with surface miners working hard to comply well ahead of the compliance deadline. By Munesu Shoko.
With legislation set to compel surface mining operations to install proximity detection systems (PDS) and collision prevention systems (CPS), Booyco Electronics believes the industry has already gone down the PDS route well ahead of the regulator’s compliance deadline, which is expected to be announced soon on the back of increased fatalities at South African mines.
Having recorded 51 deaths in 2019, the lowest number of mine fatalities in the history of the South African mining industry, the sector witnessed a regression of 18% and 23% in 2020 and 2021, respectively, according to figures provided by the DMRE. Consequently, the regulator is expected to compel the mandatory use of PDS and CPS at surface mining operations as a matter of urgency.
“The Minerals Council South Africa has over the years been working closely with the industry, PDS suppliers and original equipment manufacturers (OEMs) to review the technology and making the necessary recommendations to the regulator. The industry should be commended for the apparent mindset shift towards PDS technology. Traditionally, it was viewed as a ‘grudge buy’, but that is no longer the case. Surface mining companies are busy making strides to comply, well ahead of the enforcement date of the legislation,” he says.
When Booyco Electronics was founded some 16 years ago, recalls Lourens, installation of PDS solutions was largely driven by corporate social responsibility – it was just the ‘right’ thing to do. The industry eventually developed to a point where installations were all about complying with the legislation.
“Despite the lack of certainty around the enforcement of the legislation, there is a growing acceptance in the surface mining industry that the legislation is coming. As a result, lots of work is happening in the background to make sure that mining operations do comply with the legislation well before the compliance deadline. I believe that there has been a change in attitude; the grudge purchase stance has been replaced by an understanding of the value proposition of this technology and overall solution,” says Lourens.
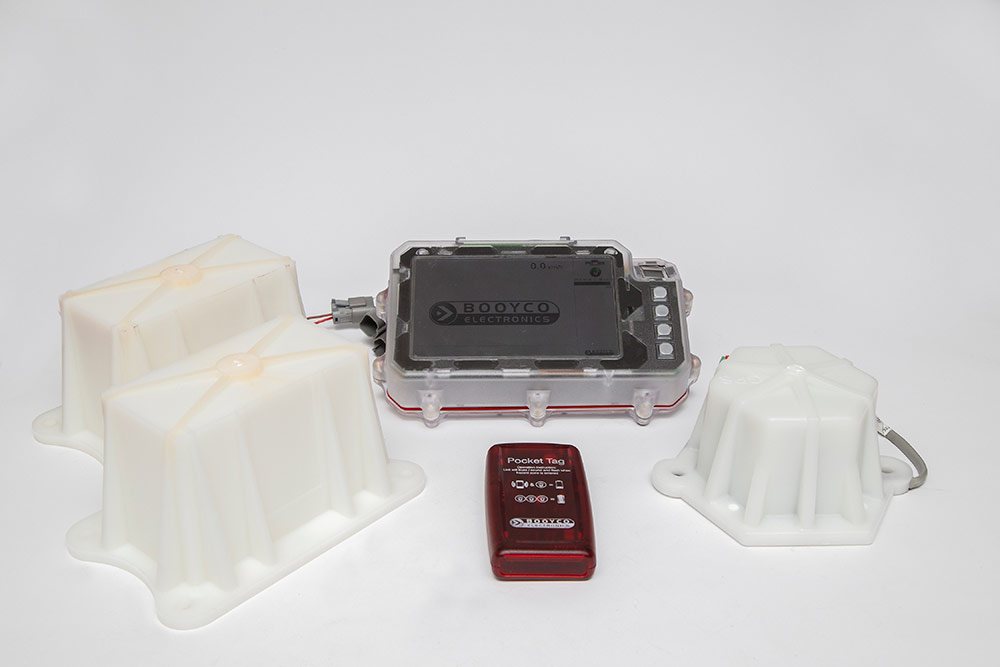
Significant headway
The industry has over the years made significant headway with regards to the testing of the technology. The Minerals Council, says Lourens, has worked closely with PDS suppliers to review the functional requirements of PDS specifications. Several operations have done their risk assessments and, where significant risk exists, deployed the technology in mitigating those significant risks.
Lourens has seen increased testing and implementation in the surface environment than ever before. Traditionally, he says, the underground environment has had a much higher compliance rate than surface mining.
“Surface miners have largely implemented Level 7 and 8 systems, with further tests being conducted on Level 9 systems. Of note is that the industry is accelerating its risk assessments, which are crucial in informing the level of risk on each site. In some surface mining environments, there are low risk vehicles that do not require fitments of PDS units. Therefore, it is crucial that every operation performs its own risk evaluation to identify its specific PDS needs,” he says.
In the quarrying industry, for example, risk evaluation done at industry level has identified that the vehicles posing most risk are typically articulated dump trucks, front-end loaders and light-duty vehicles (bakkies). This has enabled the industry to approach PDS unit suppliers for quotes on units that can warn of possible collisions (level 7), identify and advise on corrective actions (level 8), or implement a ‘slow-down and stop’, a level 9 engineering control intervention.
Out of the enquiries that Booyco Electronics is getting, Lourens notes that there is limited assumed risk on people detection. “We see a big focus on vehicle-to-vehicle risk, with limited interest in the people protection aspect of PDS installations. We are not sure if the approach is informed by internal risk assessments or the fact that mines have put in place measures to separate people from machines.”
As part of their risk assessments, several operations have implemented pedestrian walkways as a means of separating people from moving machinery. While Lourens acknowledges that PDS technology is no silver bullet to the quest for Zero Harm, he believes that as an engineering control, the technology has proven its mettle in mitigating risk at mines.
Although initial focus has been on Level 7 and 8, Lourens notes that there is significant uptake of Level 9 interventions at surface operations. According to a survey conducted by the Minerals Council, he says, there are over 300 machines running Level 9 units in surface operations across South Africa.
“There are some sites that have implemented Level 9 successfully, while some are still conducting tests, with a view to adopting,” says Lourens.
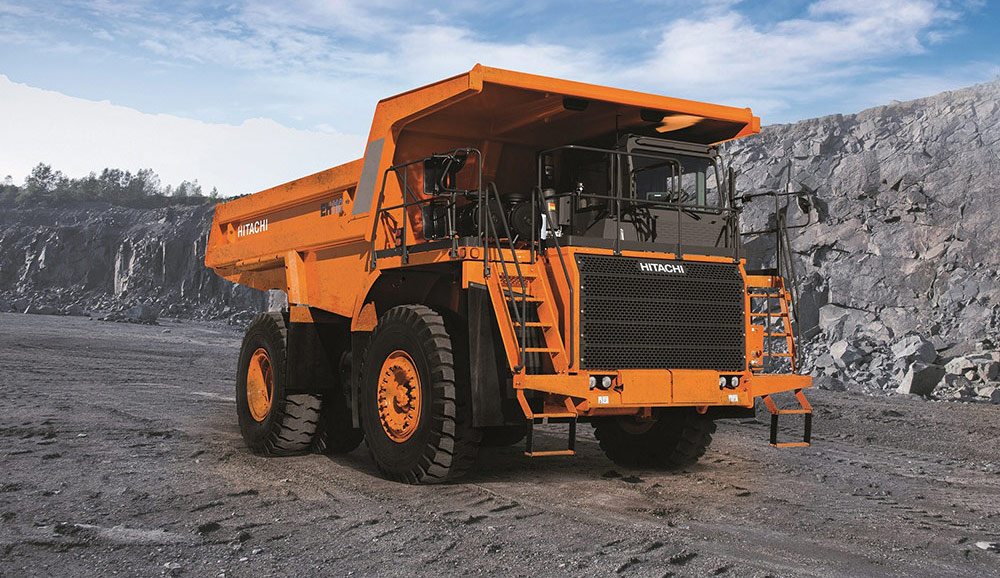
Testing
Some three years ago, PDS suppliers had to undergo simulation testing at the University of Pretoria, as well as a trial run in a mining environment to demonstrate the capabilities of their solutions before submitting their technical files to the DMRE. The Minerals Council managed this process.
Lourens says the Minerals Council contracted the Vehicles Dynamic Group (VDG), part of the University of Pretoria, to develop a simulation model on how to evaluate PDS functionality. The simulation – developed at a lab scale level – was made for both surface and underground mining scenarios.
“We ran multiple tests while continuously improving on performance until we got to a point where we were progressing to single and multiple machine tests on site. These single and multiple machine tests are ongoing at a couple of surface mines, and we have been pleased by the results thus far,” he says.
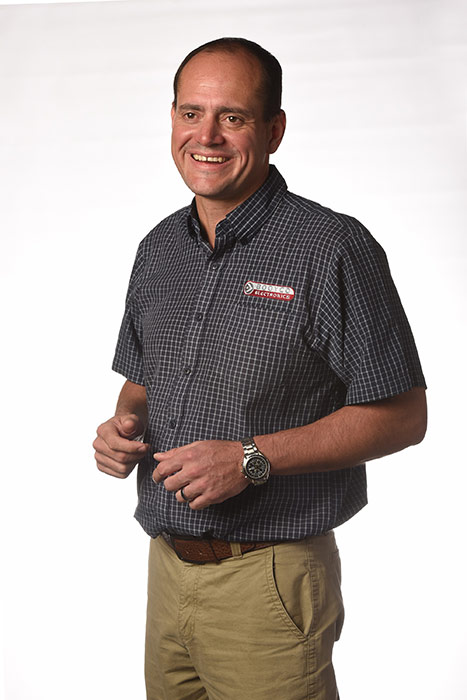
Integration
From an integration point of view, one of the recent key achievements, says Lourens, was the industry’s adoption of the ISO 21815-2 (2021) standard, which deals specifically with how a PDS solution should integrate with OEM offerings. It allows for a common interface between all PDS suppliers and the different OEMs.
“The adoption of the interface standard was a major coup for the industry. One of the important things we had to do before we even got to the single machine testing stage was to make sure that we complied to the standard, which allows our solution to interface with all the OEMs. It’s encouraging to have the standard adopted and approved to make sure that all industry players can work on a single interface,” he adds.
Technology partnerships
From an internal technology development perspective, Booyco Electronics is committed to continuous improvement. “While we have made some good improvements, we are currently not 100% where we want to be from a functional perspective. There is, therefore, some dependency on third-party information for us to perform the outstanding functionalities,” says Lourens.
To further optimise technology value for mines, Booyco Electronics has in recent years collaborated with various strategic technology partners. Each of the partners brings a different level of expertise and experience to the ecosystem.
The first partnership was with Australian-based automation systems provider, Remote Control Technologies (RCT), which brings to the table a third-party interface that enables Booyco PDS and CPS systems to speak to OEM machines. RCT has successfully implemented integration with multiple OEMs across the globe with their remote and automation offerings.
Booyco Electronics has also tied up with technology systems integrator, Ramjack Technology Solutions. Technological specialisation, says Lourens, now demands expertise, skill sets and hardware that extend far beyond what single multinational companies can provide. This invariably leads to silos of expertise developing on mines that require bridging. Booyco Electronics therefore works with Ramjack Technology Solutions to help mines to integrate their CPS and PDS solutions with other technologies effectively, in the interests of greater safety and productivity.
Booyco Electronics has also collaborated with another systems integrator, TecWise. TecWise’s in-depth knowledge of underground and open pit mining allows the two companies to deliver cost-effective, relevant, as well as technologically advanced and robust solutions in a safe manner.
The newest collaboration is with Wenco International Mining Systems, which is traditionally a fleet management systems provider.
“Wenco develops an integrated suite of solutions to support the digital transformation of the mining industry. Fleet management, asset health, data analytics and other technologies join together in the spirit of open interoperability to raise mine productivity and efficiency, lower routine costs and establish a safe and smooth mining operation. We saw it valuable to incorporate Wenco’s fleet management solutions with our PDS solutions to give the customer a turnkey solution,” concludes Lourens.
The article was first published in the January/Edition of Quarrying Africa.