In July 2023, ELB Equipment announced that it was adding the MDS range of heavy duty static and track trommels to its stable, ‘closing the circuit’ for its minerals processing customers in southern Africa. Speaking at the launch of the MDS M515 track trommel on November 2, 2023, Desmond van Heerden, CEO of ELB Equipment, said the MDS range of heavy-duty track trommels had generated increased global attention, especially following the company’s 2021 acquisition by Terex.
“I had the privilege of looking at some of their products at CONEXPO-CON/AGG in the United States earlier this year and I was thoroughly excited by what I saw. Following extensive investigations and analysis of the product by our team, we decided to add MDS to our product portfolio. We believe that this addition complements the existing offering in our Mining Division and closes the circuit for our mineral processing customers,” says Van Heerden.
Raheel Qamar, business development manager at MDS, says ELB Equipment is a logical partner for MDS as the company already represents other Terex brands, such as Powerscreen scalpers and screens in southern Africa. Given the vast amount of mining activity on the continent, Qamar tells Quarrying Africa that Africa has always been a market of interest to MDS International.
“I am very excited to partner with ELB Equipment, a flagship name in the southern African mining industry,” says Qamar. “Our products will benefit from the high levels of service and support that ELB Equipment is renowned for. We have a niche product that will introduce a totally new way of doing things.”
Equally excited about the new partnership is ELB Equipment’s divisional director, Wakefield Harding, who says that the addition of MDS trommels speaks directly to ELB Equipment’s strategy to expand its offering into new crushing, screening and environmental industries with products that complement its existing portfolio.
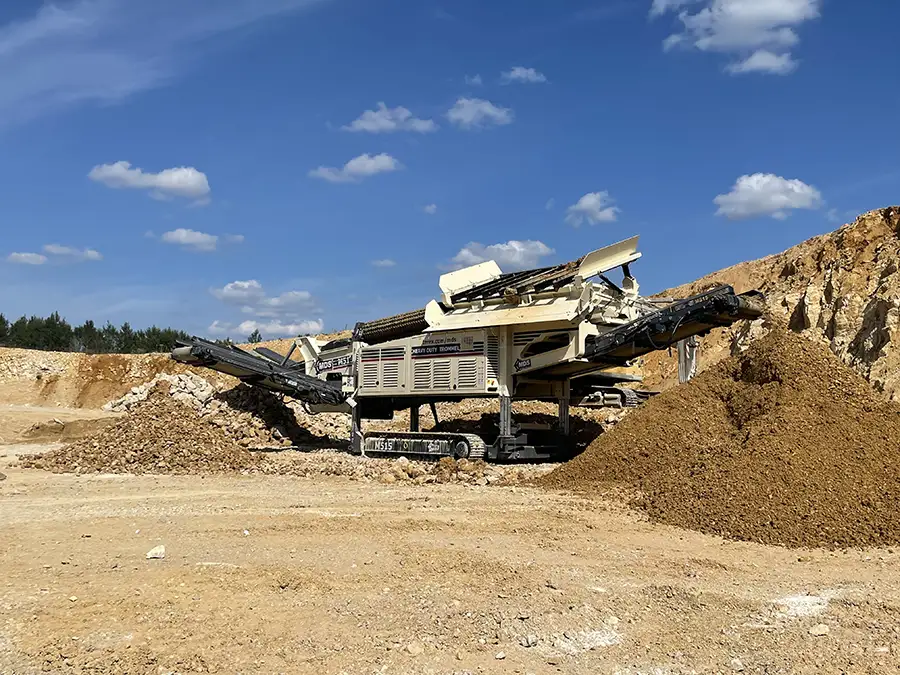
First machine
The first MDS machine on ELB’s arrival lounge is the M515, said to be the only heavy-duty track trommel of its nature in the world. The MDS M515 – the best-selling model in the range – is ideally suited for quarries, mines and construction, confirms Qamar. In quarrying, the machine excels at crafting riprap, gabion stone and armour rock, as well as reclaiming rocks entangled with clay and other sticky materials.
The sheer size of material that the machine can take and process sets it apart, says Qamar. With a hopper capacity of 20 tonnes (t), the MDS M515 can take a feed size of up to 800 mm and process it down to various size ranges between 100 and 450 mm at a production capacity of up to 500 tonnes per hour (tph). “Traditionally, trommels of this size are static. We are the only company in the world that offers mobile heavy-duty trommels of this size,” says Qamar.
The machine comes complete with three fold-out conveyors – the fines conveyor, the mid-product conveyor with a maximum rock size of 450 mm, and the oversize conveyor with a maximum rock size up to 800 mm. What sets this machine apart is that the biggest rock size you can channel through the fines conveyor is 200 mm.
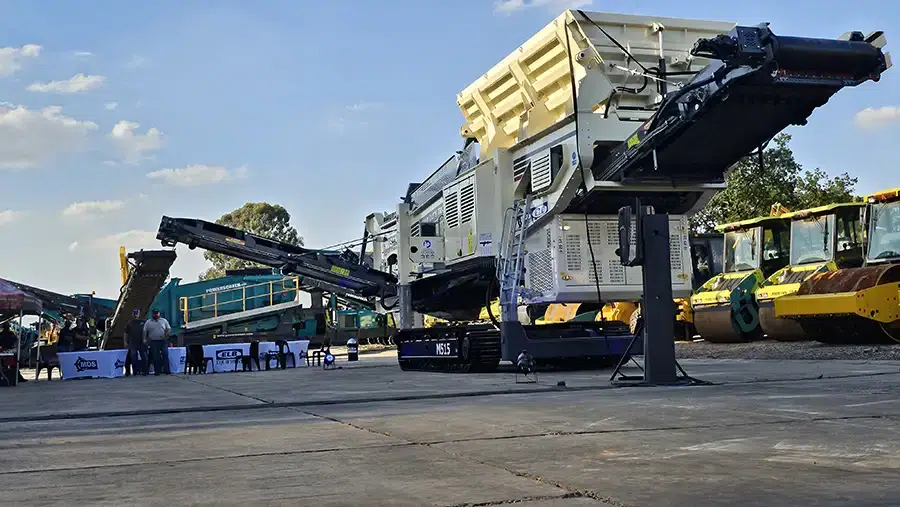
Place in the market
Heath Dickson, product and applications manager – Mining Division at ELB Equipment, believes there is a place for mobile trommels in the local market. “The machine can take up to 800 mm and separate it into 100-, 200-, 300- and 450-mm sizes, which no conventional screen can do,” says Dickson. “To provide context, the biggest mobile screen in our stable is the Powerscreen Warrior 2400, and the biggest size that it can screen down to is only 270 mm.”
Dickson says the MDS M515 will therefore usher in a new screening era in a range of applications. For example, it will come in handy when producing dump rock for road construction, which ranges between 65 and 300 mm. It is also ideally suited for producing riprap or armour rock, an effective solution for building dams and protecting coastlines and structures from erosion by the sea, rivers or streams. Dickson says that no screen can produce the required sizes for riprap and armour rock, which are generally between 450 and 800 mm. Traditionally, he says, these products are hand-selected with excavators and grabs.
“We also see big potential for this machine in the diamond fields. Diamonds by their very nature are below 50 mm in size, yet 70% of the feed could be bigger than 50 mm. Diamond mines can therefore run the feed through this big trommel before sending anything below 50 mm onto the processing plant,” explains Dickson.
Other features
One of the key features of this machine is its ease of mobility, which allows it to be tracked around the site and transported from mine to mine if need be. The machine is also easy to set up and can be up and running in about ten minutes of arrival on site.
In addition, the updated design incorporates new elements that enhance accessibility and stockpile capacities. Maintenance is a breeze with the engine’s swing-out feature, along with a convenient access platform that simplifies access. Both the fines and mid-product conveyors have been extended to elevate stockpile heights. Furthermore, the engine’s new side placement allows for easy fitting on smaller bed trailers, reducing transportation expenses for customers.
A range of drum configurations is also available, including frames with interchangeable screens or fully welded drums. “The drum cleaner is effective for cleaning clay-bound rock, and rocks mixed with limestone and other tricky materials, in preparation for crushing. Where many conventional machines fail in wet, harsh mining conditions, especially in areas such as Mozambique, this machine will thrive,” says Qamar.
Growth prospects
Van Heerden is confident that the MDS venture will be a success for ELB Equipment. The range will benefit from the company’s extensive aftermarket footprint of ten strategically located sales, service and support outlets, which is complemented by 60 service vehicles.
Qamar also believes that there is definitely a ready market for the MDS heavy duty trommel range in southern Africa. In the past, MDS has sold a few units in the region directly, without which, according to Qamar, is testimony to the interest in this range. In fact, there are four units already operating in the region – two in the DRC and one each in Mozambique and Madagascar.
In conclusion, Harding says the MDS range is bound to boost production volumes for local customers while increasing profitability on many new and existing plants in South Africa and the southern African region at large. “The plan is to put the first unit into operation in South Africa. We will bring in a smaller unit next year which we will deploy as a test unit to prove concept,” concludes Harding.