In response to the growing demand for comminution solutions that place high value on mobility and ease of deployment, Weir announced the reintroduction of its WMWP concept at the start of this year, which was followed by a customer launch event in the first half of the year.
While Weir’s TRIO® brand previously had a legacy range of wheeled plants, which made use of TRIO crushers, screens and materials handling solutions, the solution has been completely redesigned to suit new market dynamics. The WMWP concept now combines all the features and benefits of Weir’s TRIO and ENDURON® ranges of equipment in an easy to deploy and relocate, complete crushing and screening solution.
At Electra Mining Africa, which took place from 2-6 September at the Johannesburg Expo Centre, Weir demonstrated its first commercial unit which, according to Hakan Karlsson, Director Crushing and Screening at Weir, generated a lot of interest, signalling the acceptance the concept has garnered since its official introduction earlier this year.
On display at Electra Mining Africa was the Weir Modular Cone/Screen WMWSC36-5162, a combination of a TRIO TC36 cone crusher and a TRIO TIO 5162 double-deck screen on a single trailer. The solution can be operated as a standalone unit or as part of an existing plant. It can also be integrated as a fully mobile solution, highlighting the versatility of Weir’s wheeled modular plant offering. Soon after Electra Mining, the unit was destined to be deployed at a gold dump reprocessing and aggregate production operation in Gauteng, South Africa.
Jaco Kotzé, Team Leader Comminution Design at Weir, tells Quarrying Africa that the design of the unit was informed by customer feedback. The goal, he says, was to create and deliver a product that meets or exceeds customer needs and expectations.
“Following the customer launch event, we had good customer inputs and insights which, to a great extent, informed the design of the first commercial unit. We took the feedback to heart and fine-tuned the first unit, which we showcased at Electra Mining,” says Kotzé.
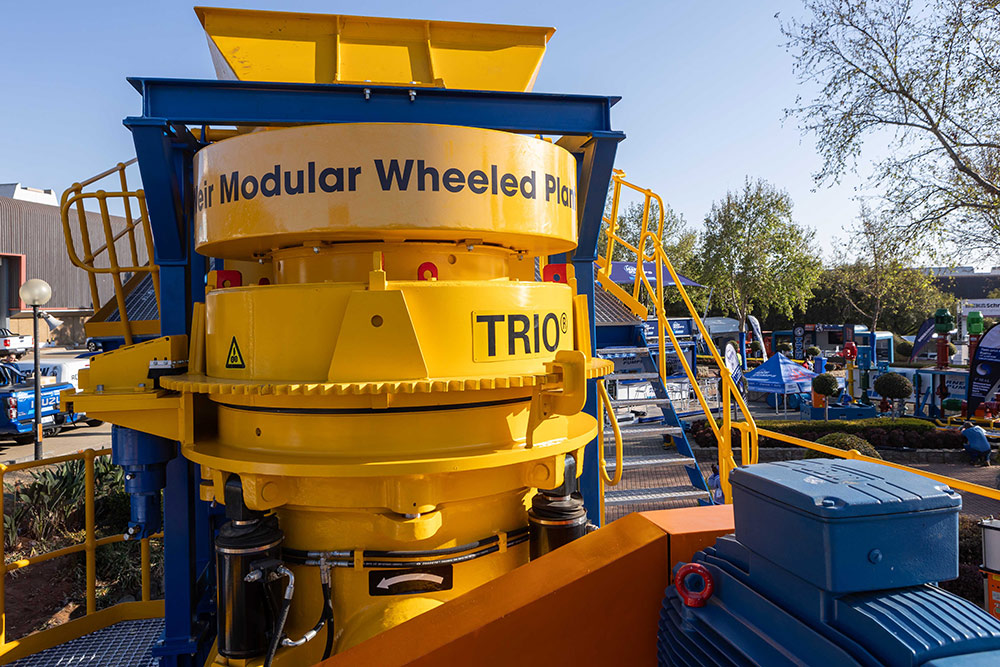
Customer input
From the onset, adds Kotzé, the introduction of the WMWP concept was aimed at addressing specific customer needs in the market. Based on Weir’s feedback collection, the most relevant and useful aspects of the design were always going to be mobility and ease of deployment – key parameters that allow contractors to move on and between production sites.
“Given that the design of the WMWP concept addresses specific customer pain points, we have seen good acceptance in the market. In addition to mobility and ease of deployment, the concept offers the flexibility of a mobile plant and the productivity of a static plant. From an economic point of view, customers can enjoy the mobility of the plant without the complexity associated with additional maintenance obligations of components such as diesel engines and tracks related to mobile tracked units,” says Karlsson.
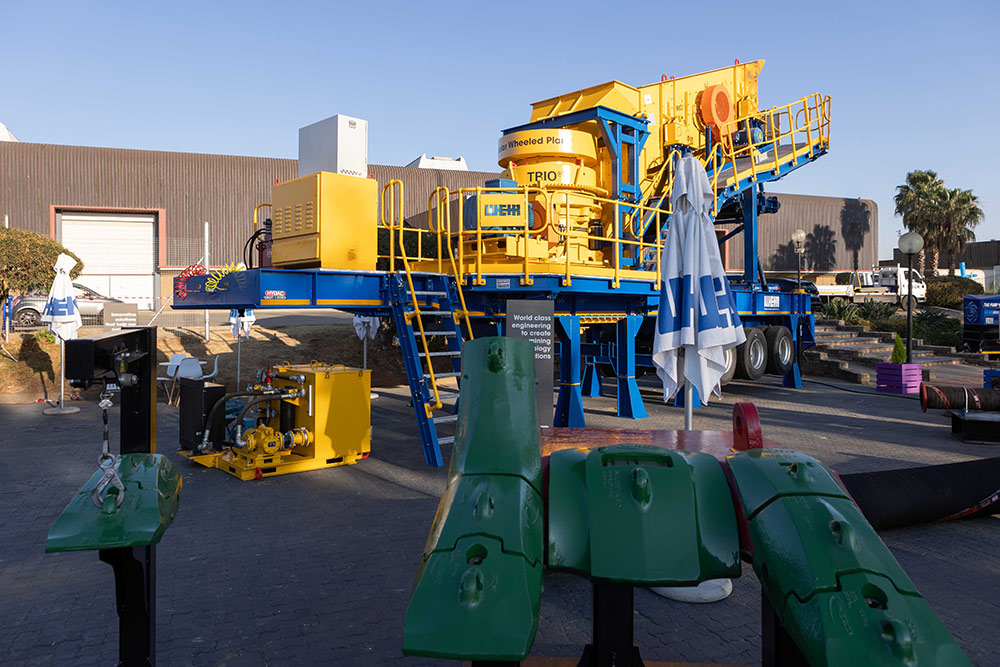
The concept
While Weir displayed a cone/screen combination at Electra Mining, the company’s wheeled plant concept will soon be available in various configurations, starting from primary crushing solutions comprising a hopper, a vibrating grizzly feeder and a jaw crusher, to secondary crushing and stations which consist of a vibrating screen and a cone crusher. To combine these solutions, one can use Weir Modular Conveyors to configure a plant that is capable of producing aggregates for various end-use requirements.
More importantly, Weir utilises equipment that is within the dimensions and weights that can be accommodated on a multi-axle trailer. With that comes the limitation of the amount of mass that can be accommodated per axle, in addition to legal road limits on overall combination length, width and height. The machines that Weir uses for its wheeled plants are in the 100 to 350 tonnes per hour (tph) range. Once the throughput gets bigger than that, says Karlsson, the equipment becomes too heavy, and the solution loses the sense of mobility and resembles a fixed plant.
Commenting on some key features of the system, Kotzé makes special mention of the unique hydraulic and mechanical deployment system which requires minimal truck-mounted cranage during site installation. Its purposefully designed leg system raises the plant from wheels, levels it and installs main supporting legs without any cranes being required.
“The ease of mobilisation on site is a major feature of our wheeled plant concept; no expensive cranage is required. To provide context, we mobilised the unit which we displayed at Electra Mining with the help of a truck-mounted crane and within half a day, the unit was fully assembled,” says Kotzé.
When in operation, the plant is supported by structural support legs with the operational load removed from wheels/axles and hydraulic lifts for working safety and structural stability, as well as resulting in reduced noise and vibration. All connections are done with structural pins and bolted connections, resulting in seamless integration of all components.
The modular primary jaw crushing units are fed directly with excavator or front-end loaders, with optional standalone hopper extensions for direct dump truck feed. The jaw-wheeled units include an integrated overband magnet system for removal of tramp metal. A surge hopper unit with an integrated belt feeder could be added in circuit to ensure proper choke feeding of cone crushers for optimal crushing quality and performance.
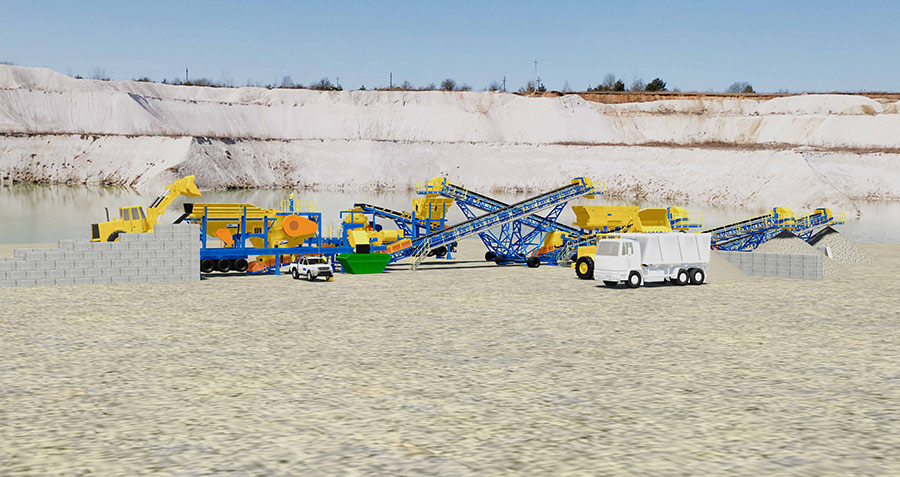
Benefits
One of the major benefits of the Weir wheeled plant concept is that it eliminates the complexity of having a diesel engine as part of the unit as well as tracks which require additional maintenance, over and above the crushers and screens themselves. Consequently, customers can focus their maintenance attention on equipment that is core to their operation – crushers and screens – as the availability of these machines is what earns them money.
“By their nature, our wheeled plants are portable crushing and screening solutions with minimal civil requirements, which translates into both time-savings and reduced operational costs for customers,” says Kotzé.
These solutions can be transported on road with standard horse kingpin connection (South African road transport requirements) or containerised (subject to main equipment size) for shipping to remote sites where sea freight is more economical. Currently, says Kotzé, the plants are designed to meet road legal requirements for southern African countries, but this can be tailored to meet requirements in any other region.
“In addition, these plants are designed with safety in mind and ease of maintenance as the highest priority. Various crushing and screening wheeled plant modules seamlessly integrate together with the Weir Modular Conveyor System (WMCS), all could be powered from a central generator/master control wheeled unit, with cable racking and routing allowance already provided for,” says Karlsson.
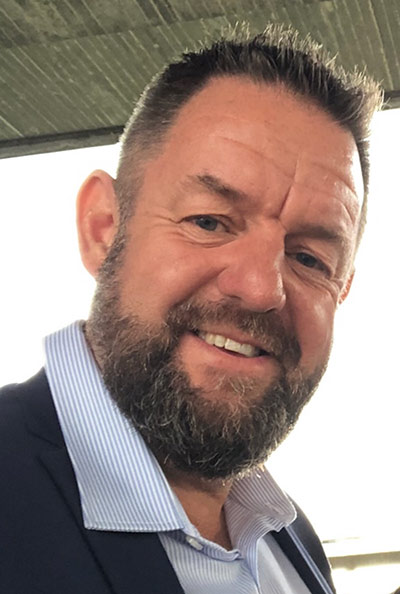
Solid foundation
With the development of the first unit, Kotzé says Weir has laid a solid foundation for the success of the WMWP concept. The next step is to broaden the range with other solutions such as jaw crushers, horizontal shaft impactors and vertical shaft impactors (VSIs). However, every plant will be tailored to each customer’s operational needs.
“We recently had a specific enquiry about switching out a cone crusher for a VSI to meet the customer’s material shaping needs for an aggregate application. We are therefore broadening the range to cater for the various needs of the market. We already have a full scope of what we want to offer, from primary to secondary and tertiary crushing,” concludes Kotzé.