As the mining industry forges ahead on its path towards innovation to improve efficiency, safety and sustainability, the past decade has witnessed a rapid move towards intelligent drilling, particularly anchored by the evolution of autonomous drilling, not only for enhanced precision and productivity, but also to advance efficiency and safety in opencast mines.
Among the global original equipment manufacturers (OEMs) leading this charge has been Sandvik Mining and Rock Solutions with its i-Series range of drills – under which the DR412i rotary blasthole drill falls. Designed for standard rotary drilling with optional down-the- hole (DTH) hammer drilling power, the DR412i is an automation-ready drill that replaced the previous KS-Series, a range of hydraulic drills which made its name in the market due to its robustness, confirms Trinity Nkosi, sales engineer, Surface Drills Department at Sandvik Mining and Rock Solutions.
“On the back of a trend towards intelligent machines, we responded by introducing the i-Series. As our platform of the future, the i-Series family comes with an impressive array of advanced features and customer benefits. One of the major talking points is the scalable surface drill automation architecture, which allows for a customised path to the level of automation each customer needs, when they need it. While the DR412i differentiates itself with its automation-ready capabilities, it retains the same robustness as its predecessor range, the KS-Series,” says Nkosi.
Suited for soft to medium/hard rock formations, the DR412i can drill 203 to 311 mm diameter blastholes with a single-pass capacity of 17,65 m or multi-pass capacity of 75,5 m. Primarily used in surface mining, it can also be deployed in oil and gas applications.
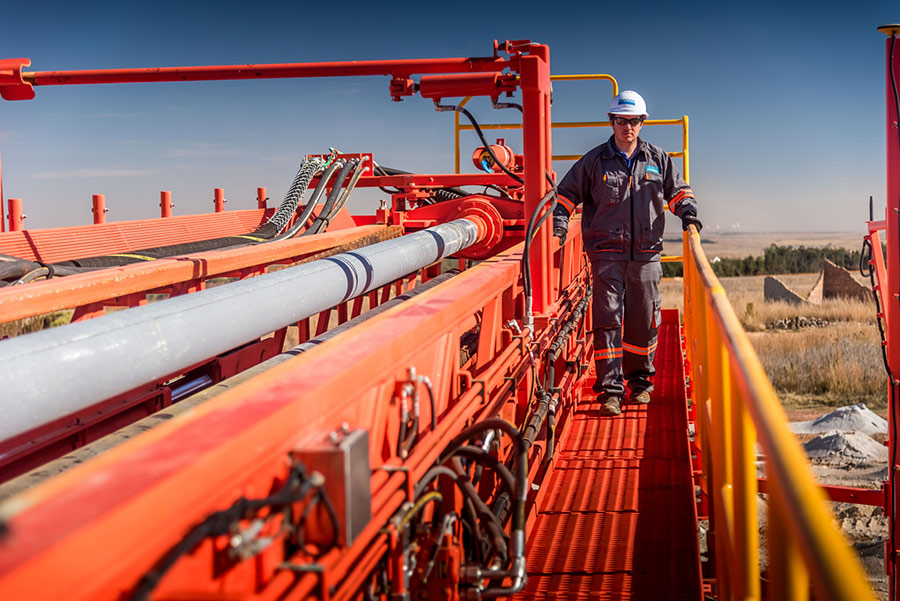
Intelligent drilling
One remarkable feature on the DR412i is the scalable surface drill automation which features flexible, customised automation capabilities that allow customers to add the automation modules they need, when they need them.
Sandvik offers various automation levels – iDrill (onboard operation) and AutoMine® (remote operation). Automated onboard functions allow the rig to work from partial to full autonomy . The operator monitors at fleet level and takes control only when required. The onboard automation functions of Sandvik’s i-Series rotary drill rigs form the basis for remote operation, minimising the risk of human error.
The AutoMine product group – Line-of-Sight, Control Room and Autonomous – offers autonomous and remotely operated drilling. It allows operators to simultaneously control and monitor multiple surface drills from the comfort and safety of a remote control room.
One operator can control multiple drill rigs simultaneously, either by a line-of-sight setup from a van or trailer close to the operating area. Alternatively, a Control Room option may be selected to operate the drill rigs from any location, be it on the mine site, or even from another city. This reduces exposure to noise, dust, vibration and exposure to hazardous environments. The operator monitors the fleet and can easily switch to control the rig requiring detailed attention.
The AutoMine system and intelligent rig control system ensure accurate and efficient drilling operations. The intelligent system helps to use the drill rig’s full potential in the many ways it is designed to be operated. AutoMine includes a safety system designed in accordance with international functional safety standards. This is critical for mines, where operator safety is of paramount importance.
When it comes to data monitoring, the MySandvik data portal is available in three subscription levels to access telemetry reports and dashboards. MySandvik Insight is the entry level package, which offers performance reporting for the machine. With insights on fuel consumption and metres drilled, fleet owners can follow production and understand the efficiency of their drilling operations.
MySandvik Productivity gives fleet owners access to fleet utilisation, alerts and service indicators. With this package, customers can follow production, understand efficiency, know their fleet, understand performance, identify bottlenecks and review work practices. My Sandvik Onsite is a monitoring solution that transforms real-time data generated by Sandvik’s i-Series’ surface drill rigs into actionable insights for productivity improvements. The on-premises solution works on a local network and can be integrated into any surface mining system.
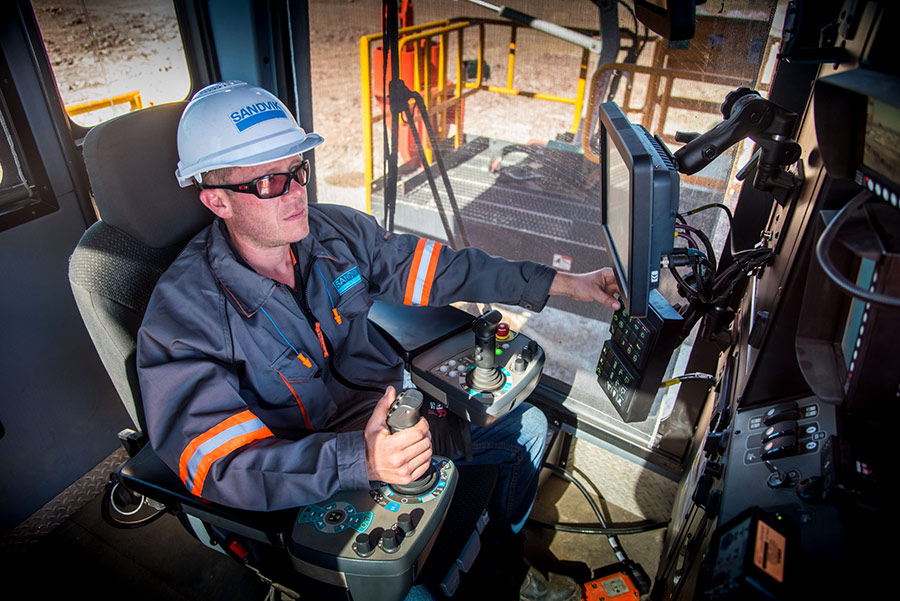
Key differentiators
With productivity in mind, the Sandvik DR412i uses a CAN bus controlled hydraulic system to monitor the machine, allowing for timely preventative maintenance and delivering higher availability.
Durability is another key design parameter, anchored by the chain-driven feed system. “Whereas most competitors use a cable-driven feed system, which is prone to slippage and has a short lifespan, we make use of a chain-based feed system, which requires less adjustment and has self-tensioning capabilities. The chain feed system delivers cleaner holes, which improve blast quality at a lower cost,” he says.
The travelling centraliser reduces drill pipe wobble to produce straighter holes faster, extend component life and reduce unplanned maintenance. This feature, says Nkosi, increases the life of drilling pipes.
To withstand harsh operating conditions, the DR412i benefits from a heavy steel body and powerful engine. “Compared with competitor offerings in this size class of pedestal drills, the DR412i is much heavier, largely due to the massive steelwork and a bigger engine. While there might be a concern that a bigger engine uses more fuel, that is not the case. This is made possible by the advanced compressor management system reduces the load on the engine by isolating the compressor during non-drilling applications in order to maximise efficiency and reduce fuel burn. The Compressor Management System can save customers up to 30% on fuel, with a proportional reduction in carbon footprint and extension of both engine and compressor life,” explains Nkosi.
Equipping the drill with a large engine, he adds, also means that the motor is not frequently used close to its capacity load. The DR412i therefore averages a 70-80% load on the engine, whereas most pedestal offerings in the size class peak around 95% load range, which not only increases fuel consumption, but also negatively affects engine life.
Putting operator comfort and control to the fore, the new-generation ergonomically designed cab includes controls on the armrests, touchscreens, angled windows to reduce glare and a safari-style roof to keep the cab cooler.
The wider, 360-degree walkways enable superior drill access for easy pre-shift inspection and routine maintenance. An optional hydraulic main-access stairway can be mounted to provide a parallel step onto and off of the drill.
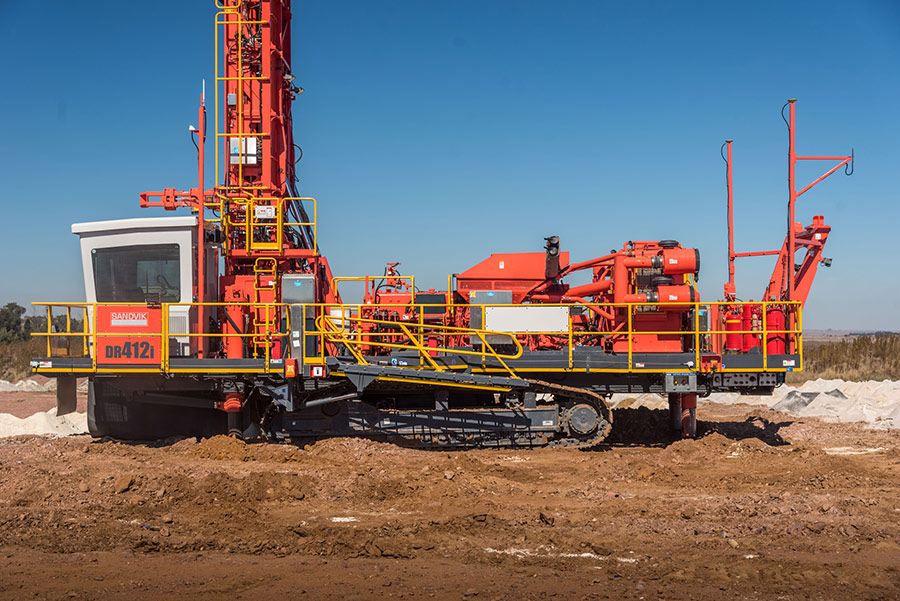
Proven capabilities
The first DR412i in Africa has been hard at work in a coal application in South Africa for the past two years, and the customer is particularly happy with the power, precision, productivity and efficiency of the machine.
In a massive feat, a mine in the Mesabi Iron Range in northeastern Minnesota drilled over 1 000 m in a day using a 271 mm drill bit. This was made possible by the drill’s robustness and powerful build.
“In Australia, a coal mining operation increased its penetration rate by 18 m per hour by deploying the DR412i, which in turn resulted in a 43,4% reduction in fuel consumption per metre compared to other drills – a big factor in the mine’s ability to reduce its cost of operation,” concludes Nkosi.